- Home
- About WACKER
- WACKER at a Glance
- History
Our History
Join us on a journey through over 100 years of history. A success story from 1914 to the present day – with groundbreaking innovations and pioneering ideas to forge ahead in the 21st century.
Anniversary:
30 Years of WACKER in China
Along with business partners and government representatives, WACKER celebrated the 30-year anniversary of its subsidiary in China. What began as sales offices has long since developed into an extensive network of production, research and service sites. WACKER now employs a staff of around 1,700 in China.

WACKER Celebrates 75 years of Silicones
From pioneering silicone development in Europe to being the world’s second largest manufacturer of silicone products today: WACKER has a 75-year success story worth celebrating.

WACKER Purchases ADL BioPharma
WACKER has strengthened its biotechnology business through the acquisition of this Spanish CMO for the foods, pharmaceuticals and consumer goods industries. ADL BioPharma employs 300 people and offers roughly 2,000 cubic meters of additional fermentation capacity. The purchase sets the stage for further growth.

New Production Facility in India
In Panagarh, India, WACKER opened a production site for manufacturing silicone rubber and silicone rubber compounds for electromobility, medical engineering and electricity supply. The site is part of the Group’s new growth strategy. Some 100 new jobs will be created during the first expansion phase.

Construction of the Technical Competence Center for mRNA Actives in Halle
A symbolic ground-breaking ceremony launched the construction of the Technical Competence Center for mRNA actives in Halle. At the Weinberg Campus, four production lines were initiated for active ingredients based on mRNA, such as vaccines for coronavirus. Production capacity in Halle will more than triple. The number of employees will be more than doubled. WACKER is investing more than 100 million euros in these projects.
Sustainable Development Goals
WACKER presented its new, ambitious sustainable development goals. Not only will WACKER select sustainable suppliers for its raw-material procurement, it will also make its consumption of energy and water even more efficient. WACKER continues to invest in expanding its portfolio of specialty products. These help our customers to market climate-friendly and resource-saving solutions. WACKER Sustainable Solutions manages the product portfolio in line with defined sustainability criteria. By 2030, WACKER’s entire portfolio is to meet these criteria and greenhouse gas emissions are to be halved, regardless of volume growth. The company intends to achieve net zero by 2045.
WACKER Sustainable Solutions
New Production Facility in China
WACKER acquired a 60-percent stake in SICO Performance Material Co., Ltd., a specialty silane manufacturer. Based in Jining, China, SICO is a leading producer of organofunctional silanes for high-performance adhesives, sealants, coatings and composite materials. This acquisition sees WACKER further expanding its portfolio of high-quality specialty products in Asia.

Expansion of Biopharma Operations
WACKER increased its influence in the biopharma market by acquiring Genopis Inc., a pharmaceutical contract manufacturer. Renamed Wacker Biotech US Inc. , it produces pDNA for innovative therapeutic agents, including nucleic acid-based gene therapies and vaccines.

Changes on Executive Board
Dr. Christian Hartel Dr. Christian Hartel has been Wacker Chemie AG’s new president and CEO since May 2021, succeeding Dr. Rudolf Staudigl, who retired at the end of the Annual Shareholders’ Meeting. Angela Wörl was appointed to the Executive Board as personnel director.
Executive BoardCoronavirus Pandemic
WACKER plays its part in the fight against coronavirus and donated some 11,000 liters of isopropyl alcohol to make 15,000 liters of disinfectants for Bavarian hospitals and care facilities.

New Production Plants
WACKER invested in its production facilities for biologics, LMPs (live microbial products) and vaccines at its Amsterdam site.
Wacker Chemie AG expanded its Chinese polymer activities by investing around US$100 million in building two new production plants at its Nanjing site.
WACKER Global
-
2023
-
2022
-
2021
-
2020
Expansion in South Korea
After a 20-month construction phase, Wacker Chemie AG starts up a new spray dryer for producing dispersible polymer powders in Ulsan, South Korea. The new facility is part of the site’s ongoing expansion to increase the company’s production capacity for dispersions and dispersible polymer powders in Asia.

Research on Silicon-Based Materials
Wacker Chemie AG intensifies its research into silicon-based materials for high-performance batteries, acquiring a stake in British battery specialist Nexeon Ltd. Powerful lithium-ion batteries are vital for applications in mobile devices, such as smartphones and tablets, and in electric vehicles.

Silicon-Metal Production in Norway
WACKER’s site in Holla, Norway, starts up a new silicon-metal production plant. The output of the new furnace, one of the largest of its kind in the world, increases the Holla site’s total capacity by more than 40 percent, enabling it to cover about one-third of WACKER’s demand at its German sites.

New Production Site in the Netherlands
WACKER acquired a Dutch production plant from SynCo Bio Partners Luxembourg S.à r.l. This Amsterdam-based facility is now called Wacker Biotech B.V. and produces biopharmaceuticals, probiotics and vaccines.

WACKER BIOSOLUTIONS
WACKER BIOSOLUTIONS began producing fermentation-based cystine at its site in León, Spain. At the same time, the division expanded its Jena site to include biologics production facilities.

Renewable Resources for Production
WACKER is the world’s first manufacturer capable of using renewable resources to produce commercial quantities not only of dispersions based on vinyl acetate-ethylene copolymer (VAE), but also of further VINNAPAS® brand products based on vinyl acetate.

Sale of Majority Stake in Siltronic AG
This strategic approach marked a shift in focus: WACKER will now concentrate on its chemistry and polysilicon business.

Visit from German President
German President Frank-Walter Steinmeier visited WACKER’s Nünchritz production site during his three-day tour of the Free State of Saxony. Accompanied by then Premier Stanislaw Tillich, he learned about WACKER’s role as an economic player in the region, as well as about technical recruiting, training, and maintaining a work-life balance.

Largest Investment in the History of WACKER
In Charleston, Tennessee, USA, the new production site for polysilicon started operation. Construction took five years, with the investment costing approx. $2.5 billion. Expansion of polysilicon capacity that had grown steadily since the start of the solar boom at the turn of the century reached its peak.

World Premiere:
First Industrial 3D Printer for Silicones
The process developed by four WACKER scientists is a milestone in additive manufacturing.

IPO of Siltronic AG and Company of the Year Award
The weekly publication ICIS Chemical Business named WACKER as its Company of the Year. IPO of Siltronic AG in the same year.

One Hundred Years of WACKER
The company celebrated the day of its founding at an event in Munich with some 500 guests, including Bavaria’s then Premier, Horst Seehofer.
75 Years of VINNAPAS® Dispersions
This success was celebrated with an anniversary exhibition held in a modified freight container for 12 months, featuring many events on three continents – and online with a dedicated microsite – “75 years of VINNAPAS® dispersions.”

50 Years of Silicone Resin Emulsion Paints
The discovery of these water repellent, yet water-vapor-permeable paints was a truly pioneering achievement on the part of our researchers and developers. Today, SILRES® silicone resin emulsion paints set a standard in sustainable coating solutions.

Opening of the Shanghai Center
Opening of the new company headquarters for the China region, including marketing, sales and administrative functions as well as R&D and applications laboratories.

Backward Integration Down to Metallurgical-Grade Crude Silicon
WACKER acquired a site in Holla, near Trondheim in Norway. Silicon that’s 98.5% pure is produced from sand and coal at this site. The subsequent upgrading to hyperpure polycrystalline silicon with a purity level of 99.99999999% takes place at the WACKER POLYSILICON sites in Burghausen, Nünchritz and, since 2016, also in Charleston, USA.

Silicones Production Site
WACKER and Dow Corning joined forces to launch the world’s largest silicones production site in Zhangjiagang, China.

-
2019
-
2018
-
2017
-
2016
-
2015
-
2014
-
2013
-
2012
-
2010
Commissioning of Production Plant for Dispersible Polymer Powders in Nanjing
The Nanjing plant can produce 30,000 metric tons of polymer powders a year, and is the largest of its kind in China. WACKER is the sole supplier of polyvinyl-acetate-based polymer dispersions and dispersible polymer powders with production sites on all three key continents.

Manufacture of Silicon Wafers in Singapore
In Singapore, Samsung and Siltronic’s joint facility started manufacturing 300 mm wafers from hyperpure silicon.

IPO in Frankfurt
A new era began for the WACKER Group in April 2006. Wacker Chemie AG shares were traded on the Frankfurt Stock Exchange for the first time on April 10. The IPO saw WACKER placing 14.99 million shares with institutional and private investors. At €80, the issue price was set at the upper end of the price range. Advance demand was huge. The shares issued were over-subscribed more than 18 times. Since the IPO was held, the family shareholder continues to keep its majority stake in the company.

Knowledge Management for Customers, Partners and New Employees
Founding of the VINNAPAS® ACADEMY. This later became WACKER ACADEMY, which is currently operating at 15 sites across the globe, providing on-site knowledge transfer about handling WACKER products and their applications.

Founding of the WACKER Relief Fund
A charitable organization that provides aid for victims of natural disasters. The aim is to provide fast and unbureaucratic aid. The main focus is helping children by building or repairing schools or orphanages.

Construction of Pilot Plant for Granular Polysilicon
These innovative little pellets are needed to manufacture silicon monocrystals. As they are easy to meter, they constitute a considerable improvement to the “poly chunks” used before. These serrated, irregular pieces had to be filled into the crucible by hand.

-
2009
-
2008
-
2006
-
2005
-
2004
A New Site in Saxony, Eastern Germany
By purchasing a plant in Nünchritz, Saxony, WACKER acquired an important new site for silicones – and created ideal conditions for the production of innovative silicone products. Over the following decade, the site was gradually expanded. Today, it is one of the three WACKER sites worldwide that produce hyperpure polycrystalline silicon.

WACKER SILICONE AWARD for the Fathers of Silicones
Richard Müller and Eugene Rochow were honored with the WACKER SILICONE AWARD. From 1942, independently of each other, both developed direct synthesis for dimethyldichlorosilane – the forerunner of WACKER’s over 3,000 different silane and silicone products.

WACKER Moves to New Headquarters
Group HQ has been based in the Neuperlach district of Munich ever since.
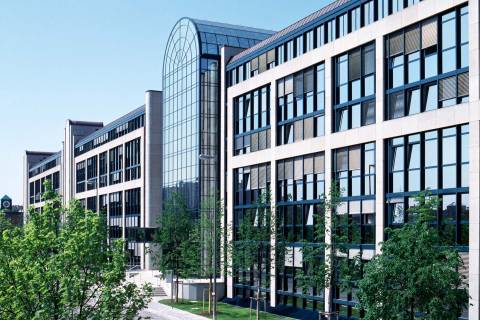
Production of Bioengineered Products Begins
The inauguration of the biotechnology research center for manufacturing compounds for the pharma, food and agricultural sectors heralds the age of biotechnology.

-
1998
-
1992
-
1990
Founding of DRAWIN Vertriebs-GmbH
In May 1987, DRAWIN Vertriebs-GmbH was founded as a wholly-owned subsidiary of Wacker Chemie AG. It took over some areas of WACKER SILICONES business division's logistics and distribution planning. DRAWIN’s product range now includes around 1,000 different silicone products supplied in over 100 countries worldwide. Its strengths are fast shipping, flexible combination of different types and quantities of products, and a wide, readily available product range.

Silicone Scientists Honored
The first WACKER SILICONE AWARD was presented. To date, this prize ranks among the world’s most prestigious awards in organosilicon chemistry. It was first awarded to Prof. Peter Jutzi and Prof. Robert Auner.

Expansion of the Biological Wastewater Treatment Plant in Burghausen
Designed for a capacity of up to 300,000 inhabitants, the plant now also treats wastewater from Burghausen and neighboring communities in Austria.

Entry into Asian Markets
Founding of Wacker Chemicals East Asia Ltd., Tokyo, Japan. A counterpart in Singapore was established a year later.

WACKER Silicon Conquers Space
Research in zero gravity: semiconductor experiments with silicon were conducted for WACKER and Chemitronic during the Spacelab mission.

WACKER Silicone Rubber Goes Liquid
Following the launch of WACKER’s first RTV (room-temperature-vulcanizing) and HTV (high-temperature-vulcanizing) grades on the market in the early 1950s and their constant enhancement, a new class emerged: LSR (liquid silicone rubber) products were introduced to the market.

-
1987
-
1985
-
1983
-
1980
The Birth of Siltronic
Wacker Siltronic Corporation was founded in Portland, Oregon, USA, for the manufacture and sales of semiconductor raw materials. The name Siltronic was used here for the first time.

A Dedicated Environmental Protection Department Established at the Burghausen Plant
The new department comprising Emissions Control, Wastewater Management and Residual Waste Management initiated the construction of a biological wastewater treatment plant.

Byproducts Become Bestsellers
HDK® was produced for the first time at the WACKER plant in Kempten. This pyrogenic silica was originally produced from the silanes that accumulated as byproducts of the Müller-Rochow synthesis (silanes and silicones) and the Siemens process (polycrystalline silicon). WACKER HDK® and its range of products are among the most successful WACKER products of all time. They are used in various applications such as silicone rubber, paints, coatings, laser toner, tooth paste and tomato ketchup.

The 1970s
Internationalization Begins
WACKER establishes new sales offices across Europe to bring its products closer to customers. Today, the company generates 80% of its sales outside Germany.

-
1978
-
1974
-
1972
-
1970
Founding of Wacker Chemitronic Gesellschaft für Elektronik-Grundstoffe mbH
This later became Siltronic. Two new full-scale production plants with distillation columns more than 50 meters high went into operation manufacturing hyperpure polysilicon and distilling the starting product trichlorosilane.

Transition from the Coal Age to Petrochemicals
Opening of the new ethylene-based vinyl acetate monomer plant. Calcium carbide was no longer needed in Burghausen. The eight 50-meter carbide silos – Burghausen plant landmarks – were repurposed to store mainly metallurgical-grade silicon used to produce silicones and hyperpure silicon.

Successful Launch into the North American Market
Founding of Wacker Chemicals Corporation WCC in New York, USA. WCC acquired Monosilicon, a company based in Los Angeles, USA, where hyperpure silicon rods produced using the crucible pulling process were cut into slices or wafers, as they are more commonly known. The term “wafer” had not yet been coined.

New Site, New Processes
At the new WACKER plant in Cologne, a facility based on the 2nd WACKER process was the first worldwide to start producing acetylaldehyde from ethylene on an industrial scale. This secured a cheap raw-material base for acetic acid and its derivatives in the VINNAPAS® range.

-
1968/69
-
1965
-
1960
New facilities and buildings were erected, including a 19-meter-high crude silane column and a tank farm for pure and intermediate products in Burghausen. In the decade between 1957 and 1967, annual sales generated from silicon-based plastics increased almost fivefold to 37.8 million deutschmarks.

2nd WACKER Process
WACKER basic research scientists set up the production of acetylaldehyde and acetic acid using a new base raw material. Instead of using expensive acetylene made from calcium carbide, cheap ethylene from the petrochemical industry could be used to manufacture these products. Known as the 2nd WACKER process, this pioneering synthesis has been included in textbooks and has been licensed all around the world.

Instant Coffee Inspires a Bestseller Product
While enjoying a cup of Nescafé, Dr. Max Ivanovits came up with the idea of developing a water-free dispersible polymer powder from water-based dispersions. Powder production began in 1958; gradually, these powders revolutionized the construction industry and made WACKER the world leader in this field.

First Production of Hyperpure Silicon
Dr. Eduard Enk laid the foundation for WACKER’s semiconductor business. The first silicon rods were produced as early as 1955. Until 1961, several hyperpure silicon production plants went into operation.

-
1957
-
1953
Research Work into Silanes and Silicones Begins
Following his lecture on “Plastics Containing Silicon,” the young chemist Dr. Siegfried Nitzsche was hired on the spot. He later became the father of WACKER silicones. In 1949, Nitzsche and his colleagues successfully synthesized silane for the first time. Soon after, the first silane furnace was up and running.

Impending Closure
After the war ended, plant operations temporarily came to a halt as the Allies contemplated dismantling the company. The efforts of the WACKER management and workforce to prevent dismantlement were successful and the plant’s facilities gradually went back into operation. It was not until 1953 that the Allies relinquished control over WACKER as part of their “disentanglement” program, returning the company to its original owners.

Resistance to Destruction of the Plant
In the final days of the war, accountant Jakob Scheipel, senior factory foreman Ludwig Schön and foreman Josef Stegmair were sentenced to death in a drum-head trial and shot in the factory yard because they had attempted to prevent the National Socialists from destroying the plant.
“Foreign Workers” Replace Around a Third of the Core Workforce Called up for Military Service
A dark chapter for which WACKER takes responsibility: In 2000, WACKER became part of the “Foundation for Remembrance, Responsibility and the Future,” which made compensation payments to victims of forced labor and to foreign workers.

-
1947
-
1945
-
1944
The Outbreak of World War II
Following the outbreak of the second World War, nearly all WACKER operations were deemed important for the war effort. This meant that production of base chemicals such as acetylaldehyde, acetic acid and chlorinated solvents continued unabated. Especially important during this time was the manufacture of high-quality metal alloys such as ferrochrome or ferrosilicon at the then WACKER plants in Mückenberg and Tschechnitz.

Patent Application for the Suspension Polymerization Process for PVC
Dr. Herbert Berg developed the process for manufacturing PVC. From 1935 until the business field was sold in 2000, WACKER PVC marketed under the VINNOL® brand turned into a growth engine that financed the development of modern production lines such as silicones and hyperpure silicon.
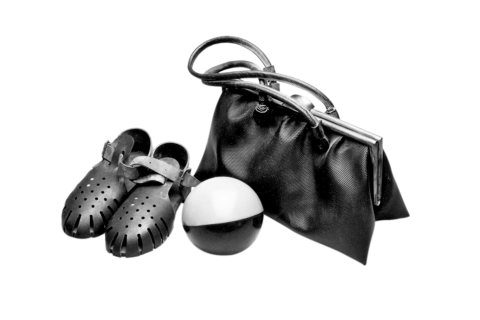
Start of VINNAPAS® Production
The managing director of the Consortium für elektrochemische Industrie, Willy O. Hermann, laid down the foundation for today’s WACKER POLYMERS business division back in the 1920s. Together with his team, he developed a process for producing vinyl acetate from ethylene and acetic acid on an industrial scale. In 1928, vinyl acetate went into production, followed two years later by polyvinyl acetate. Over the years, this would develop into the VINNAPAS® product line, ranging from adhesives in the wood industry to binders for construction applications, plastics, paper grades and woven fabric.
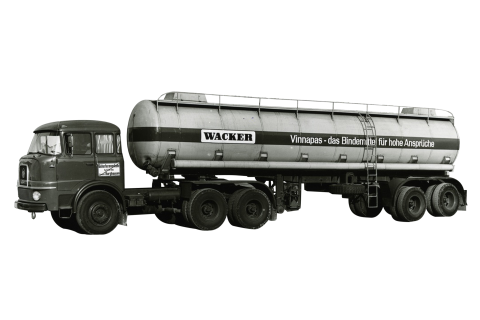
-
1939
-
1935
-
1930
Production of Intermediate and End Products from Acetic Acid
A bestseller that was in production for almost 100 years. Acetic anhydride is used for the manufacture of pharmaceuticals and crease-resistant textile fibers. Production stopped in 1997.

Company Founder Alexander von Wacker, Recently Raised to the Non-Hereditary Aristocracy, Dies at the Age of 75.
Born: May 29, 1846
Died: April 6, 1922

WACKER Shellac Made from Plastic
The first plastic made from acetylaldehyde produced in Burghausen contributed to the ever-increasing vogue of gramophone records at that time.

Founding of Alzwerke GmbH, Construction and Commissioning of the Alz Canal
The 16-kilometer Alz Canal that joins the Alz and Salzach rivers is WACKER’s lifeline. The tamed hydropower of the Alz River generates cheap, sustainable electricity – to this day. The amount of electricity obtained per year is equivalent to the power consumed by a town with some 80,000 inhabitants.

-
1922
-
1918–22
Start of Acetone Production
With 450 employees, the factory began producing acetone from acetic acid in Burghausen in the middle of the First World War. Suddenly acetone became important for the war effort: it was used to make synthetic rubber for sealing submarine batteries. This was the starting point on the trajectory to becoming an international chemical company.

Construction of the Plant in Burghausen, Upper Bavaria
The first products manufactured in December 1916 were acetylaldehyde and acetic acid, which WACKER chemists developed by reacting acetylene (made from calcium carbide) with water. This entered the annals of the chemical industry as the 1st WACKER process for producing acetylaldehyde. These products were in the WACKER portfolio until 2012.

October 13, 1914
Establishment of Dr. Alexander Wacker, Gesellschaft für elektrochemische Industrie, AG

Having trained as a cloth dealer and salesman, Alexander Wacker had by this time already earned a reputation as a successful businessman, and together with Sigmund Schuckert, he had made Elektrizitäts AG (EAG) in Nuremberg into a leading business in the electricity industry.
A visionary – even at the age of 68. His new business model: to build an industrial plant, covering applications ranging from electrochemicals through to organic chemistry.

-
1917
-
1916
-
1914