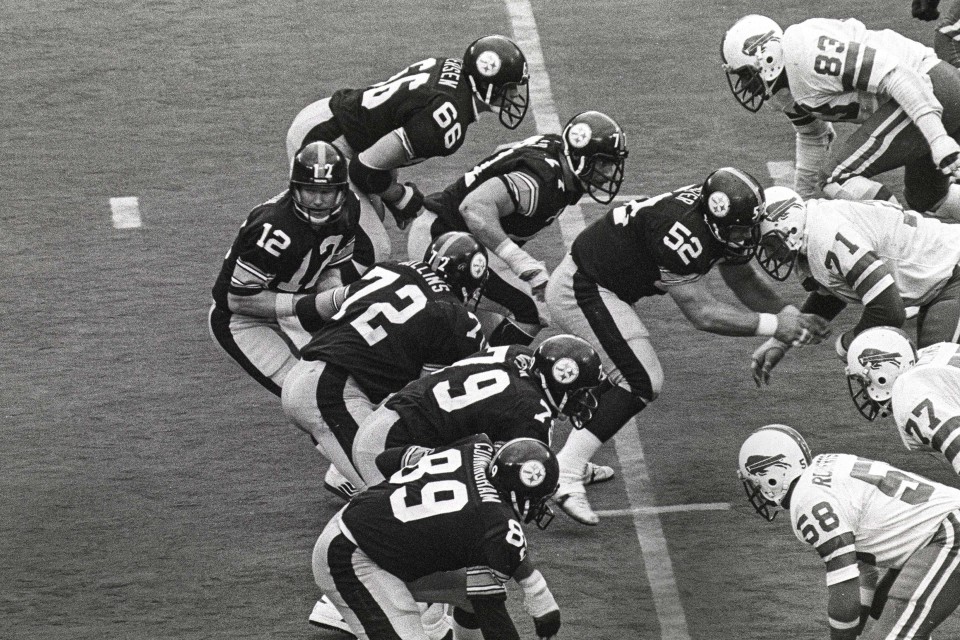
Aus Burghausen in die NFL
01.10.2019 Lesezeit: ca. MinutenMinute
Play smart, play safe
Um die Athleten beim American Football besser vor Schädel-Hirn-Traumta und deren Langzeitfolgen zu schützen, haben zwei US-Unternehmen einen neuartigen Helm entwickelt. WACKER unterstützte sie dabei mit der 3D-Druck-Technologie von ACEO®.
Die Fans der Footballmannschaft Pittsburgh Steelers nannten ihn Iron Mike – wegen seiner Zähigkeit und seiner Härte, auch gegen sich selbst. Michael Lewis Webster, 16 Jahre lang als Profi aktiv, gewann zwischen 1975 und 1980 mit den Steelers vier Mal den Super Bowl. Trotz seiner Aufnahme in die „Pro Football Hall of Fame“ sind es aber nicht seine außergewöhnlichen Leistungen im Spiel, die ihn außerhalb der Fanszene und auch außerhalb der USA bekannt gemacht haben. Sondern es ist sein tragisches Schicksal, aufgegriffen im Film „Concussion“, der in Deutschland unter dem Titel „Erschütternde Wahrheit“ in die Kinos kam.
Iron Mike litt nach seiner aktiven Sportlerkarriere unter Störungen der Sprache, des Gehörs, der Konzentration und des Gedächtnisses, hinzu kamen Handzittern und Depressionen. Er wohnte zeitweilig in seinem Auto, schlug sich im Wahn die Zähne aus und starb schließlich im Alter von 50 Jahren, offiziell an Herzinfarkt.
Der nigerianische Pathologe Dr. Bennett Omalu – im Film gespielt von Hollywoodstar Will Smith – untersuchte Websters Gehirn und das eines weiteren Footballspielers und stieß auf ein Krankheitsbild, das Mediziner als chronisch-traumatische Enzephalopathie (CTE) bezeichnen. Hervorgerufen wird CTE, so die heute gängige Lehrmeinung, durch mehrfache Gehirnerschütterungen oder leichte Schädel-Hirn-Traumata. Oft zeigen sich die Symptome erst 10 bis 20 Jahre nach den Verletzungen. Nicht nur bei Football-Spielern, sondern beispielsweise auch bei Boxern tritt CTE gehäuft auf.
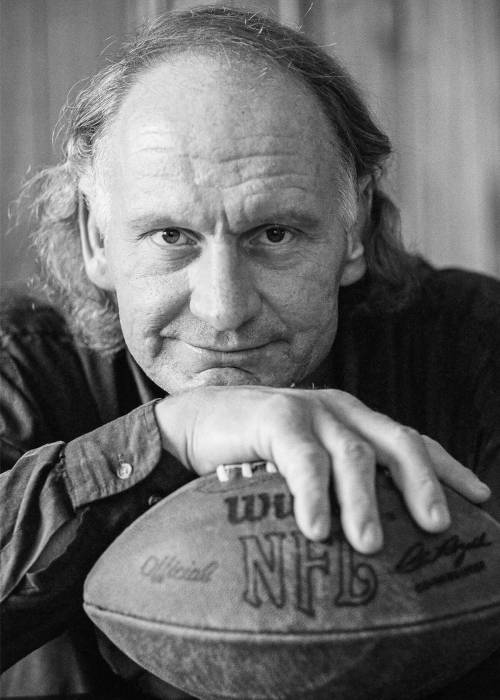
Michael Lewis Webster, auch bekannt als „Iron Mike“, litt nach seiner Profikarriere an chronischtraumatischer Enzephalopathie. Als Ursache dafür gelten mehrfache Gehirnerschütterungen oder leichte Schädel-Hirn-Traumata, die bei Footballspielern häufig vorkommen.
Besserer Schutz
Mittlerweile fördern die Funktionäre der National Football League (NFL) aktiv Maßnahmen, die darauf abzielen, Verletzungen mit möglicherweise lebenslangen Folgen – wie Gehirnerschütterungen – zu verhindern oder wenigstens wirkungsvoll zu behandeln. 2016 lancierten sie die Initiative „Play Smart. Play Safe.“ und sagten 100 Millionen US-Dollar für die medizinische Forschung und technische Fortschritte zu. Zudem schrieben schrieben und schreiben sie „HeadHealthTECH Challenges“ aus – einen Wettbewerb, der Unternehmen dazu auffordert, Verbesserungsvorschläge für Footballhelme und andere Schutzausrüstungen einzureichen.
An Runde zwei dieses Wettbewerbs beteiligte sich Ende 2017 Baytech Products, ein Unternehmen aus Asheville in North Carolina. Robert T. Bayer, Gründer und CEO, hatte einen neuartigen Helm ersonnen. Unterstützt hatte ihn dabei Brad Maloney aus South Carolina, der mit seiner Firma HelmetComp im Auftrag der Helmindustrie Produkte für diverse Sportarten, Militär und Polizei entwirft.
„Das Bahnbrechende am Design unseres Footballhelms ist, dass seine äußere Schale aus zwei Teilen besteht“, betont Maloney. „Dabei ist der obere Teil über flexible Streben mit dem unteren Teil verbunden. Daher kann er sich bei einem Stoß unabhängig vom unteren Teil und vom Kopf des Footballspielers verschieben und verdrehen.“ Diese Konstruktion trage dazu bei, dass der Helm die einwirkenden Kräfte streue und absorbiere, bevor sie auf den Kopf einwirken könnten. „Nach dem Stoß kehrt die obere Schale dann wieder in ihre ursprüngliche Position zurück“, erklärt Maloney weiter.
Beim Wettbewerb traten Bayer und Maloney mit einem Prototyp an, den sie im 3D-Druck-Verfahren angefertigt hatten, sowie mit ersten Testergebnissen aus dem Labor. Die Jury war davon so angetan, dass sie Baytech zu einem Sieger der Runde erklärte. Zudem stellte die NFL 178.000 US-Dollar für die Weiterentwicklung des Helms bereit.
Seitdem arbeiten Bayer und Maloney als Partner daran, ihre Helmtechnologie, die sie HitGardTM nennen, zu verbessern und zur Marktreife zu bringen. Nach dem Sieg im Wettbewerb begannen sie, die Schalen des Helms per Spritzgussverfahren zu fertigen, in einer Innenschale besonders schlagabsorbierende Schaumstoffe einzusetzen und die Gesichtsmaske neu zu entwerfen. Immer im Blick hatten sie dabei die strengen Anforderungen der Labortests, mit denen die NFL prüfen lässt, wie sicher und robust ein Helm wirklich ist. Dazu gehört, dass Druckkolben mit großer Energie auf bestimmte, festgelegte Punkte des Helms einschlagen.
Einer dieser Punkte befindet sich in dem Bereich, der die Stirn schützen soll: Gerade beim Football stoßen die Spieler oft frontal zusammen. Direkt unter diesem Punkt ist die Gesichtsmaske im Helm verankert – auch dort können bei einem Zusammenstoß enorme Kräfte wirken. Die HitGardTM-Konstrukteure sahen daher in diesem Bereich des Helms den Einsatz eines speziellen Dämpfers aus thermoplastischem Polyurethan (TPU) vor. „Doch dieses Material splitterte während der Laborprüfungen bei Schlägen auf die Gesichtsmaske, weil es die Energie nicht genügend absorbieren und sich nicht verformen konnte“, berichtet Brad Maloney.
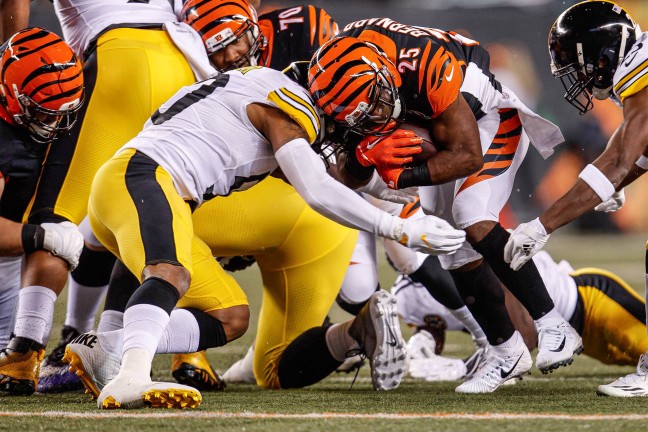
Wegen seiner physischen Härte besteht beim American Football ein hohes Verletzungsrisiko.
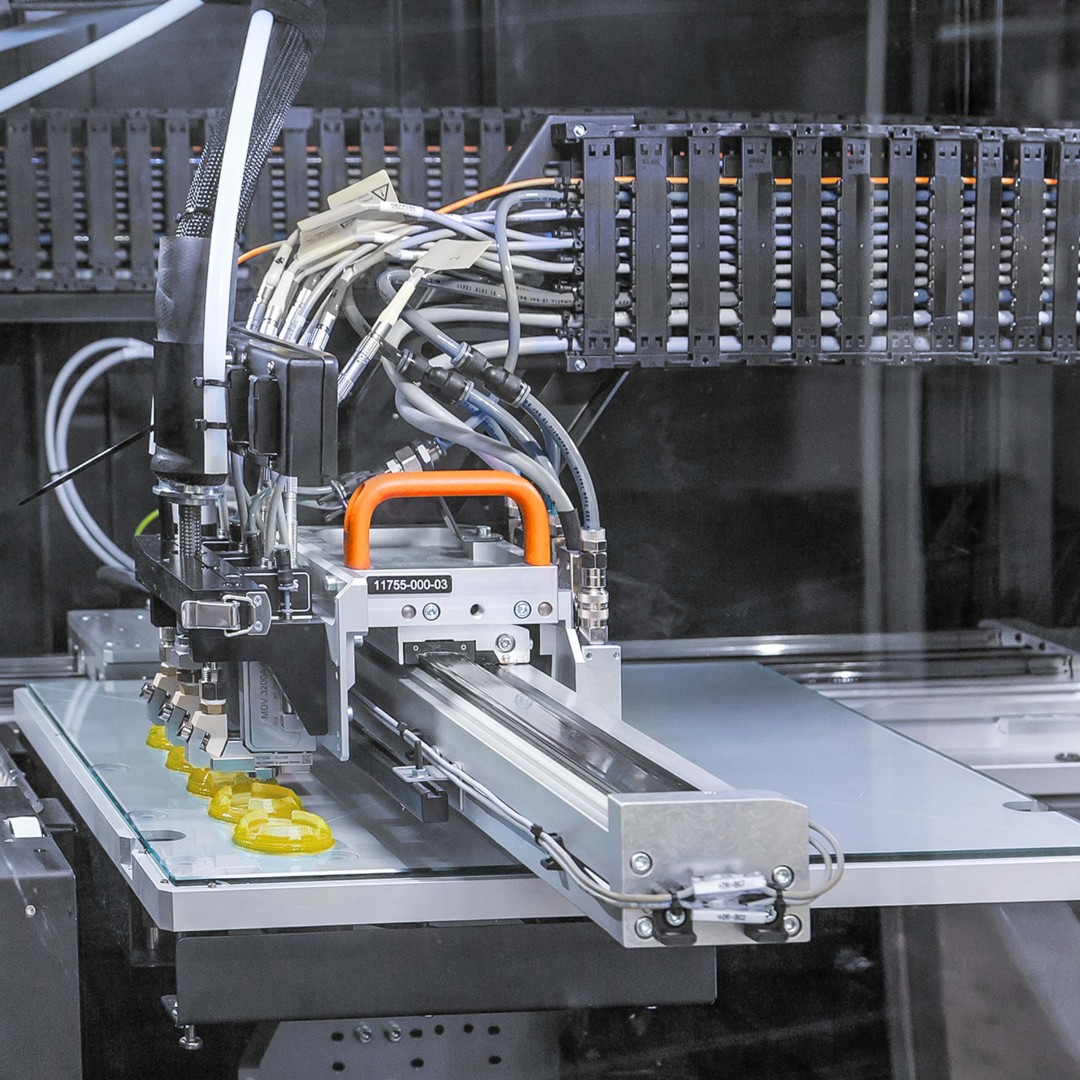
ACEO® bietet von seinem Standort in Burghausen aus einen weltweiten Service für den 3D-Druck von Siliconelastomeren. Dort entstand auch in kürzester Zeit der Silicondämpfer für den neuen Helm.
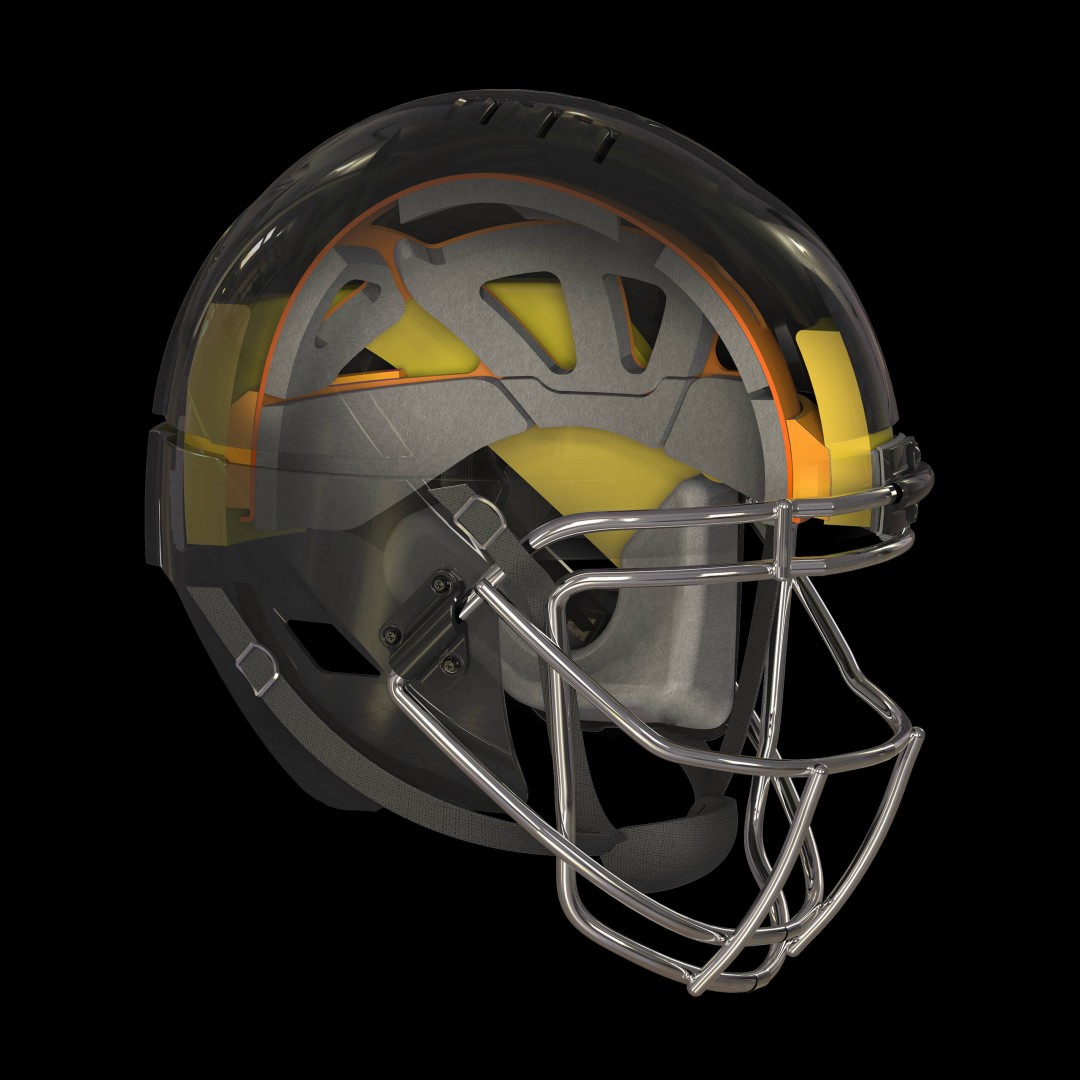
Der HitGardTM-Helm besteht aus zwei Schalen, die sich bei einem Aufprall unabhängig voneinander verschieben können und so den Kopf besser vor Verletzungen durch Erschütterungen schützen sollen.
Dämpfer aus Silicon
Daher begab sich der Produktentwickler im Frühling 2018 auf die Suche nach Alternativen. Bei seinen Recherchen stieß er auf den ACEO®-3D-Druck-Service mit Siliconkautschuk von WACKER. Über das soziale Netzwerk LinkedIn nahm er Kontakt mit dem ACEO®-Team auf. „Nachdem wir über seine Anforderungen an das Material gesprochen hatten, rückte Brad mit der Frage heraus, ob wir einen entsprechenden Dämpfer innerhalb von zehn Tagen fertigen und an HelmetComp liefern könnten“, berichtet Egbert Klaassen, Global Marketing Director für die 3D-Druck-Lösungen von ACEO® bei WACKER. Der Grund für die Eile: Es waren wichtige Tests mit externen Prüfern geplant.
Für ein Unternehmen, das Siliconteile auf herkömmlichem Wege – durch Spritzgießen – produziert, wäre Maloneys Anliegen schier ein Ding der Unmöglichkeit gewesen. Üblicherweise dauert es acht bis zwölf Wochen, bis ein solches Unternehmen aus den überlieferten Konstruktionsdaten (CAD Files) eine entsprechende – und recht teure – Form hergestellt hat. Diese muss dann vom Auftraggeber freigegeben werden, bevor das Silicon eingespritzt und so das gewünschte Teil produziert werden kann. Doch in Zusammenarbeit mit dem ACEO®-3D-Druck-Center in Burghausen wurde aus Maloneys Wunsch sehr schnell Realität. Einen Tag vor den angesetzten Tests erhielt er den Silicondämpfer, der sich in seinen Eigenschaften nicht von einem entsprechenden spritzgegossenen Bauteil unterscheidet. Maloney baute ihn in den Helm ein, der daraufhin die Tests bestand. Maloneys Fazit: „Der ACEO®-3D-Druck-Service von WACKER hat sich während unseres Projekts als äußerst nützlicher Lösungsanbieter erwiesen und wird uns darüber hinaus bei unseren weiteren Entwicklungsarbeiten begleiten.“
Zeit und Kosten sparen mit 3D-Silicondruck
Der Helmdesigner ist ganz grundsätzlich vom Wert des ACEO®-3D-Druck-Verfahrens für die Entwicklung und Markteinführung von Produkten überzeugt: „Oft stellt man nach der Herstellung von Bauteilen fest, dass noch etwas am Design geändert werden muss. Mit dem 3D-Druck lassen sich dann einfach, schnell und kostengünstig optimierte Bauteile erstellen, während beim Spritzgießen ein aufwendiger Prozess ganz von vorn beginnt.“
Derzeit fehlt noch ein entscheidender Schritt, um Helme mit der zum Patent angemeldeten HitGard™-Technologie auf den Markt zu bringen: Bayer und Maloney müssen entweder einen etablierten Helmproduzenten als Partner gewinnen oder Geldgeber für eine eigene Produktion finden. Doch angesichts der Leistungsfähigkeit des HitGard™-Helms sollte das nur eine Frage der Zeit sein: schließlich gehören seine Prüfungsergebnisse zu den besten, die jemals in einem der drei großen akkreditierten US-Testlabore erzielt wurden.
Das innovative zweiteilige Schalendesign hat, da ist sich Maloney sicher, nicht nur im Football eine Zukunft: Auch Radfahrer, Kletterer, Wintersportler und Reiter würden davon profitieren, wenn Helme besser als bisher die Kräfte und Drehmomente abfangen könnten, die bei Stoßeinwirkung auftreten. „Dabei kommt Siliconkautschuk aufgrund seiner bemerkenswerten Eigenschaften, seiner Vielseitigkeit und seiner Beständigkeit eine Schlüsselrolle zu“, betont Maloney.
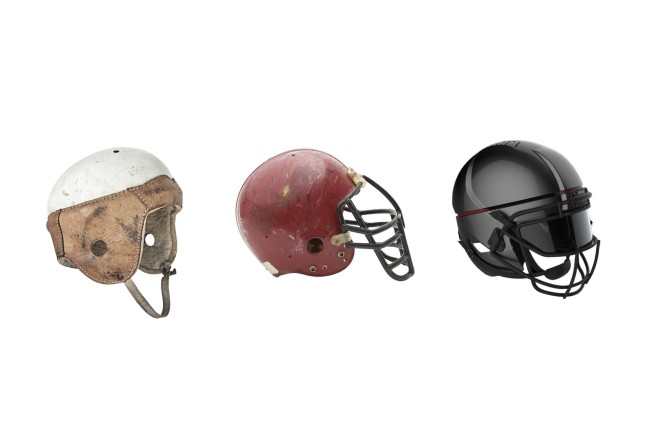
Vom Leder- zum Hightech-Helm (circa 1950–2019)
Wie es funktioniert
Die zum Patent angemeldete Technologie von HitGardTM ist ein bahnbrechendes Split-Shell-Design, das aus je einer äußeren Ober- und Unterschale und einem inneren Schalenaufhängungssystem besteht.
Die äußeren Ober- und Unterschalen sind durch stoßdämpfende Streben miteinander verbunden. Beim Aufprall kann sich die Oberschale unabhängig vom Kopf bewegen und so direkte Aufprallkräfte aufnehmen und verteilen, bevor die Energie auf den Kopf übertragen wird.
Die Oberschale absorbiert sowohl lineare als auch schräge Stöße, bevor sie in ihre Ausgangsposition zurückkehrt.
Das Innenschalenaufhängungssystem ist mit stoßdämpfenden Materialien an der äußeren Unterschale verankert. Der Kopf des Spielers befindet sich in der Innenschale, die von einem Luftporenraum umgeben ist und somit unabhängig von der direkten Aufprallenergie auf die Oberschale ist.
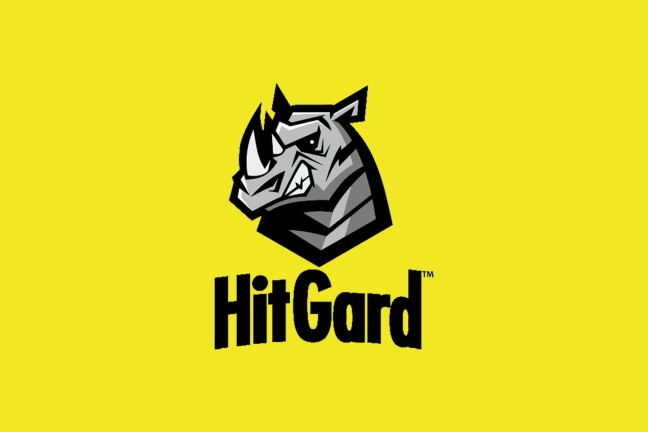
Kontakt
Mehr Informationen zum Thema erhalten Sie von
Herr Egbert Klaassen
Global Segment Manager
Wound Care, Orthotics & Prosthetics
+49 1520 935 2545
Nachricht senden