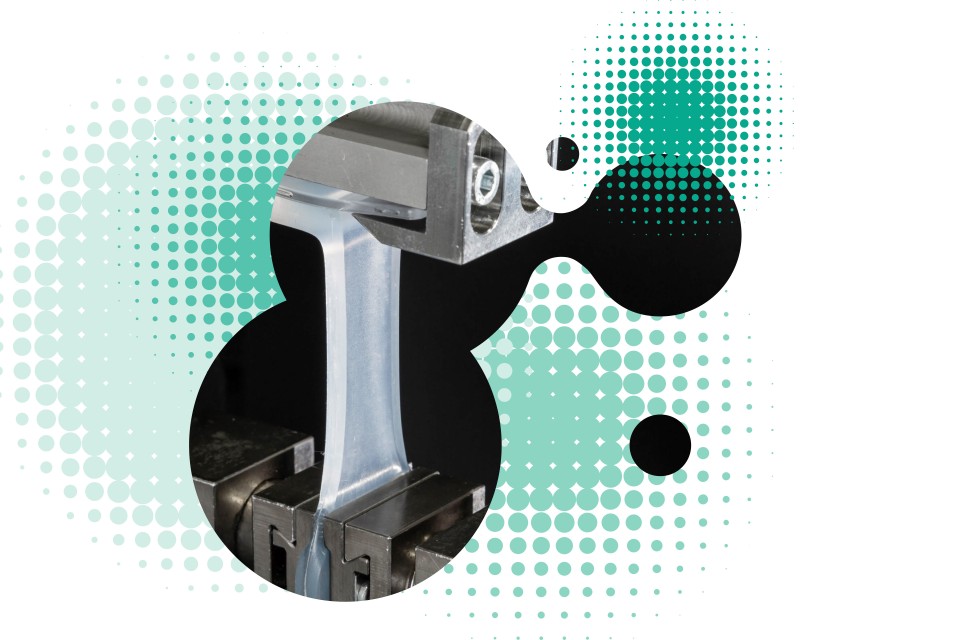
Plastics Technology
Oct 11, 2022 Read time: approx. MinutesMinute
A Strong Bond – Without Any Pretreatment
Before now, polycarbonate was a particularly tough nut to crack when it came to creating a hard/soft combination with silicone. But thanks to ELASTOSIL® LR 3078, neither priming nor, for example, plasma treatment is necessary. This liquid silicone rubber offers excellent adhesion to polycarbonate and is a cinch to process on two-component injection-molding machines.
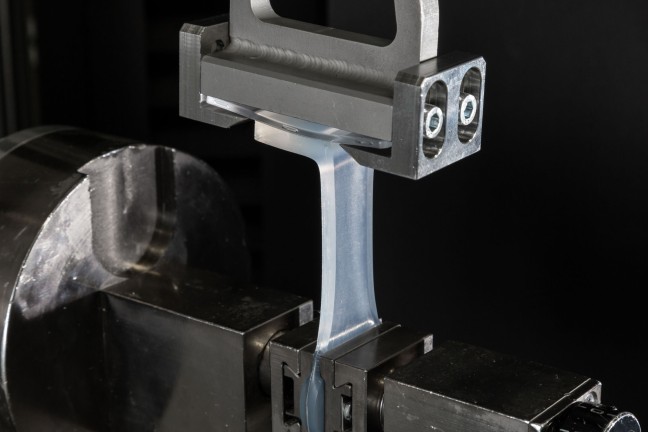
Molded plastic parts very commonly consist of two components: one hard, and the other soft and elastic. The hard component for such hard/soft combinations is usually a rigid thermoplastic and provides the strength. By contrast, the soft component functions as a seal, absorbs vibrations or sounds or improves the tactile properties of the molded article.
Product designers tend to choose a polycarbonate if the hard component is not only expected to exhibit high impact strength, heat resistance and transparency, but should also lend itself to medical products. For the soft component, they are increasingly turning to silicone elastomers, especially where the property set offered by silicones is needed: chemical and biological inertness, flexibility at low temperatures and resistance to heat and aging.
Good adhesion is essential for creating hard/soft combinations that function reliably and for manufacturing such articles cost-effectively on a large scale. “A particular challenge as regards adhesion is the polycarbonate/silicone pairing,” says Dr. Florian Liesener, head of an applications laboratory for liquid silicone rubber at WACKER in Burghausen. “With conventional silicones, the only way to achieve reliable adhesion is to either coat the surface of the polycarbonate with a primer or activate it with a plasma treatment.” For the parts manufacturer, this represents an additional, costly step, he adds.
“Our patented, self-adhesion technology has been specially developed for polycarbonate/silicone combinations.”
Dagmar Rische, Marketing Manager, Engineering Silicones
Fully Automated Processing
The new line of ELASTOSIL® LR 3078 silicone rubber products developed by WACKER provides strong adhesion to polycarbonate with no need for treating the thermoplastic substrate ahead of time. “These self-adhesive silicones are capable of being used on fully automated two-part injection-molding machines,” says Dagmar Rische, marketing manager in WACKER’s Engineering Silicones department. “This capability stems from a novel, patented self-adhesive technology that has been specially developed for the polycarbonate/silicone combination.”
As a result of this technology, which is deployed in the ELASTOSIL® LR 3078 series, the adhesion builds up rapidly – reaching high levels even as the part is still inside the mold. However, the silicone does not stick to the metal mold and the multicomponent part is easy to demold. No secondary finishing is needed and the parts can be processed further straight away. The hardness values of these product grades cover the range (20 to 70 Shore A) specified by parts designers for the soft component of the polycarbonate/silicone combination.
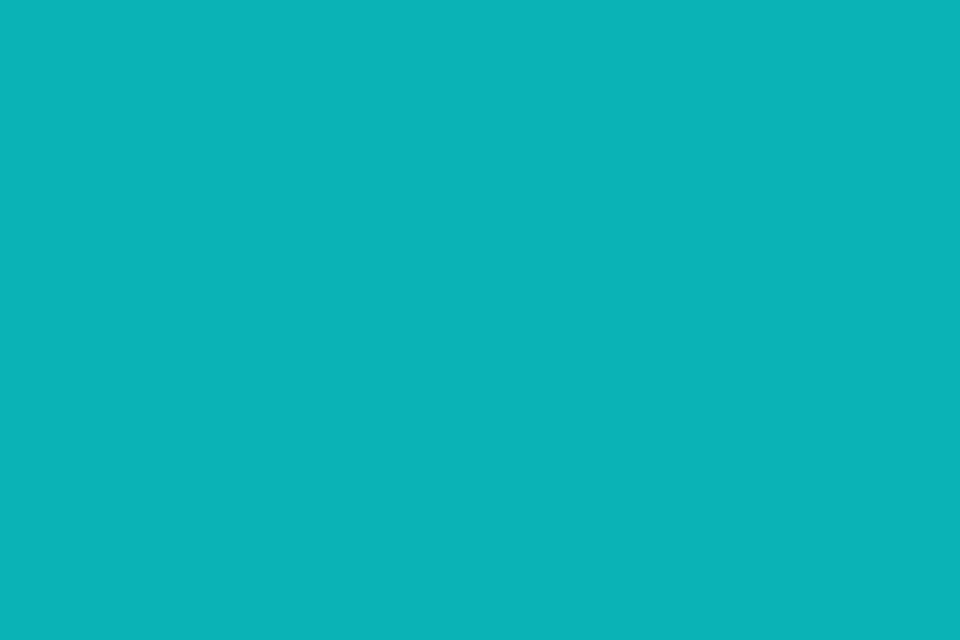
Compression Set
If deformed over a long period of time, an elastomer seal will no longer return to its exact shape after release, instead remaining more or less deformed. The extent of this sustained deformity depends on how greatly the elastic recovery of the material decreases under the prevailing storage conditions – deforming forces, the medium that is impacting the material, and the temperature. This information is provided by compression set, a parameter that is determined in a standardized testing procedure.
To determine the compression set, an elastomer test specimen (whose shape and dimensions are defined in testing standards) is placed in a compression mechanism, where it is compressed to a previously defined extent and stored in this state for a specific period of time under the testing conditions. Once the test specimen is released, it will no longer return to its original thickness. The thickness of the test specimen is measured before and after compression as well as after relaxation. The compression set is the ratio expressed as a percentage of the reduction in thickness following relaxation and the thickness to which the test specimen was compressed. A low compression set is favorable – this shows that the material has high elastic recovery.
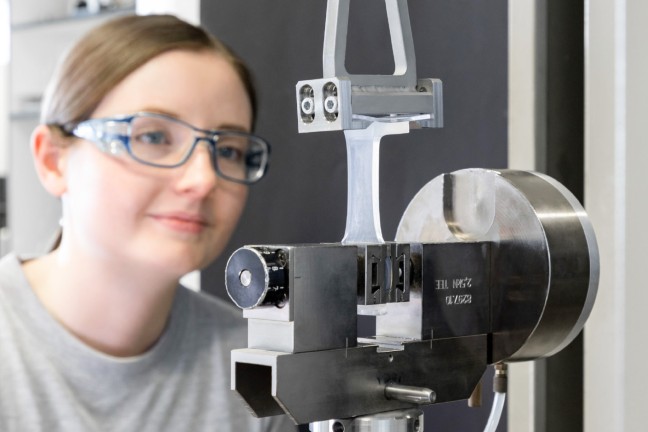
Peel testing stresses samples of multicomponent materials to their breaking point. In samples made of ELASTOSIL® LR 3078 and polycarbonate, it was the soft silicone component which consistently tore. The bond between the hard and soft components remained intact.
Very Good Peel-Force Values
The bond strength of the new product range has been thoroughly tested in WACKER’s applications labs where To test the bond strength, the WACKER engineers carried out 90° peel tests based on the ISO 813 standard. This involves preparing test strips of the material and determining the force needed to peel off the silicone layer at an angle of 90° to the polycarbonate substrate. The peel force needed to separate the two serves as a measure of adhesion. The tests showed that a peel force of at least 10 newtons per millimeter, and in many cases much higher, was needed. These are generally accepted to be very good peel-force values.
Dr. Liesener’s team also studied the failure mode in those samples which failed the peel tests. They wanted to identify the weak point in the bond: did the tear occur in the interface of the hard and soft components or did it form inside the soft component? It transpired that the silicone had suffered cohesive failure – in other words, the soft components had torn during peeling, but the bond between the hard and soft components had remained intact. This result, together with the high peel-force values, serves as proof of the excellent adhesive strength.
“The lab tests and injection-molding trials also show that the ELASTOSIL® LR 3078 range scores points for ease of processing,” marketing manager Rische is keen to stress. The liquid silicone rubbers cure very quickly and the injection-molding cycle times are short, even at relatively low processing temperatures. “This means that converters can adapt their processes to the limited heat-deflection temperature of the hard component and still achieve high productivity,” she says, further emphasizing her point.
Another plus point for ELASTOSIL® LR 3078 when it comes to injection molding is that the silicone rubber formulations have a very low tendency to form deposits in the mold. When these build up, the molds have to be dismantled and cleaned. The use of ELASTOSIL® LR 3078 more or less rules out such production interruptions altogether, with the result that fully automated processes are possible.
“Even in the non-postcured state, ELASTOSIL® LR 3078 materials possess very good mechanical properties.”
Dr. Florian Liesener, Technical Manager, WACKER SILICONES
Miniaturization of Parts on Trend
ELASTOSIL® LR 3078 can also be used to produce intricate designs and will reproduce the finest of details with great accuracy. The new product series thus goes some way toward meeting the trend to miniaturize parts.
Given the limited heat-deflection temperature of the thermoplastic hard component, polycarbonate/silicone combinations are not postcured before use, i.e. they are not heat-treated, as the polycarbonate would not withstand the thermal stress. “We have formulated our materials in the ELASTOSIL® LR 3078 series in such a way that they already possess very good mechanical properties without the need for postcuring,” underscores Dr. Liesener, a WACKER developer.
Thus, the new silicone grades are notable for having low compression set values in their non-postcured state. Elastomers that have low compression set feature high elastic recovery. Non-postcured ELASTOSIL® LR 3078 grades have compression set values far below 20 percent, as determined by 22-hour compression at 125 °C. These are very low values. Their significance is that sealing elements made from the new silicones will function reliably for long periods of time.
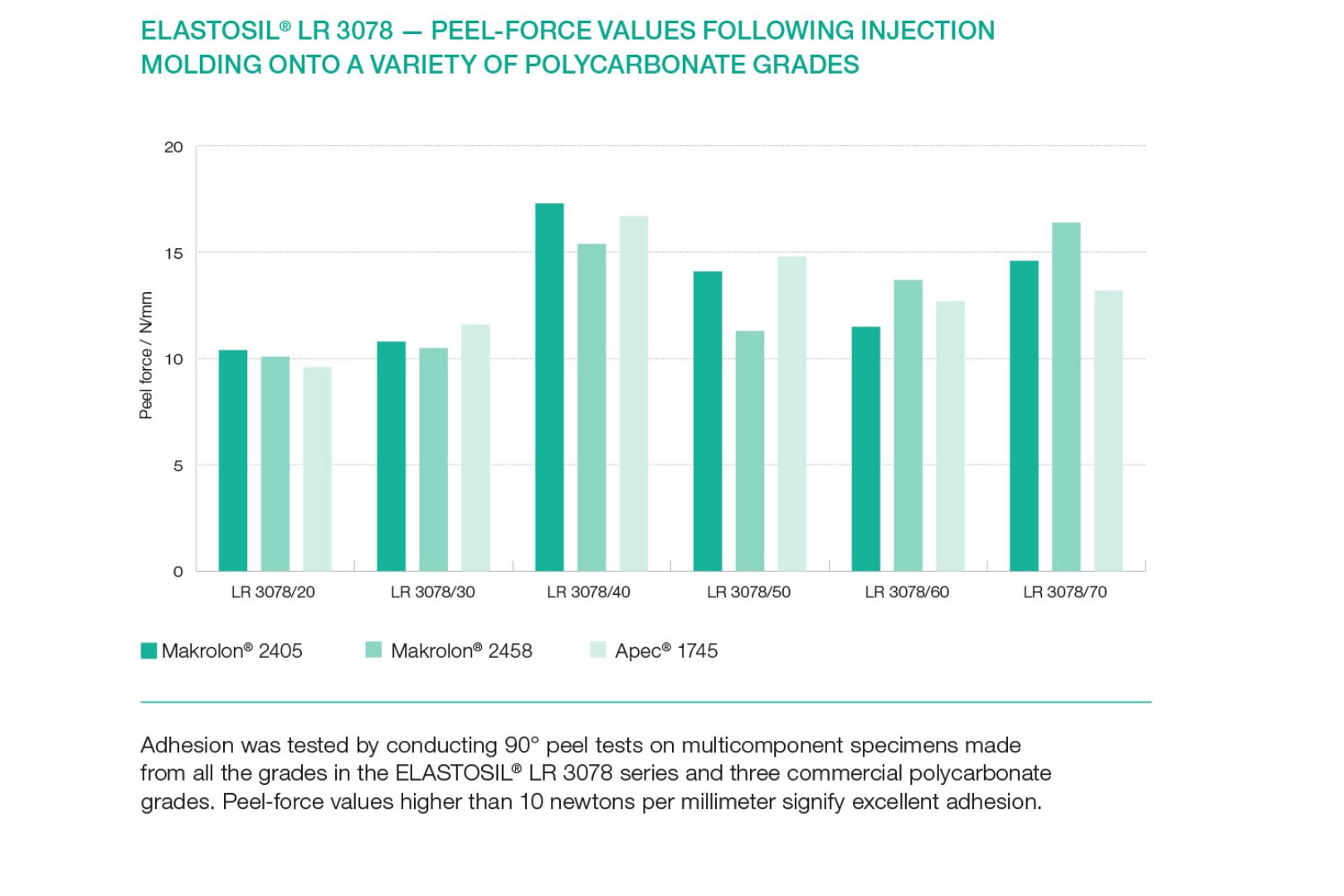
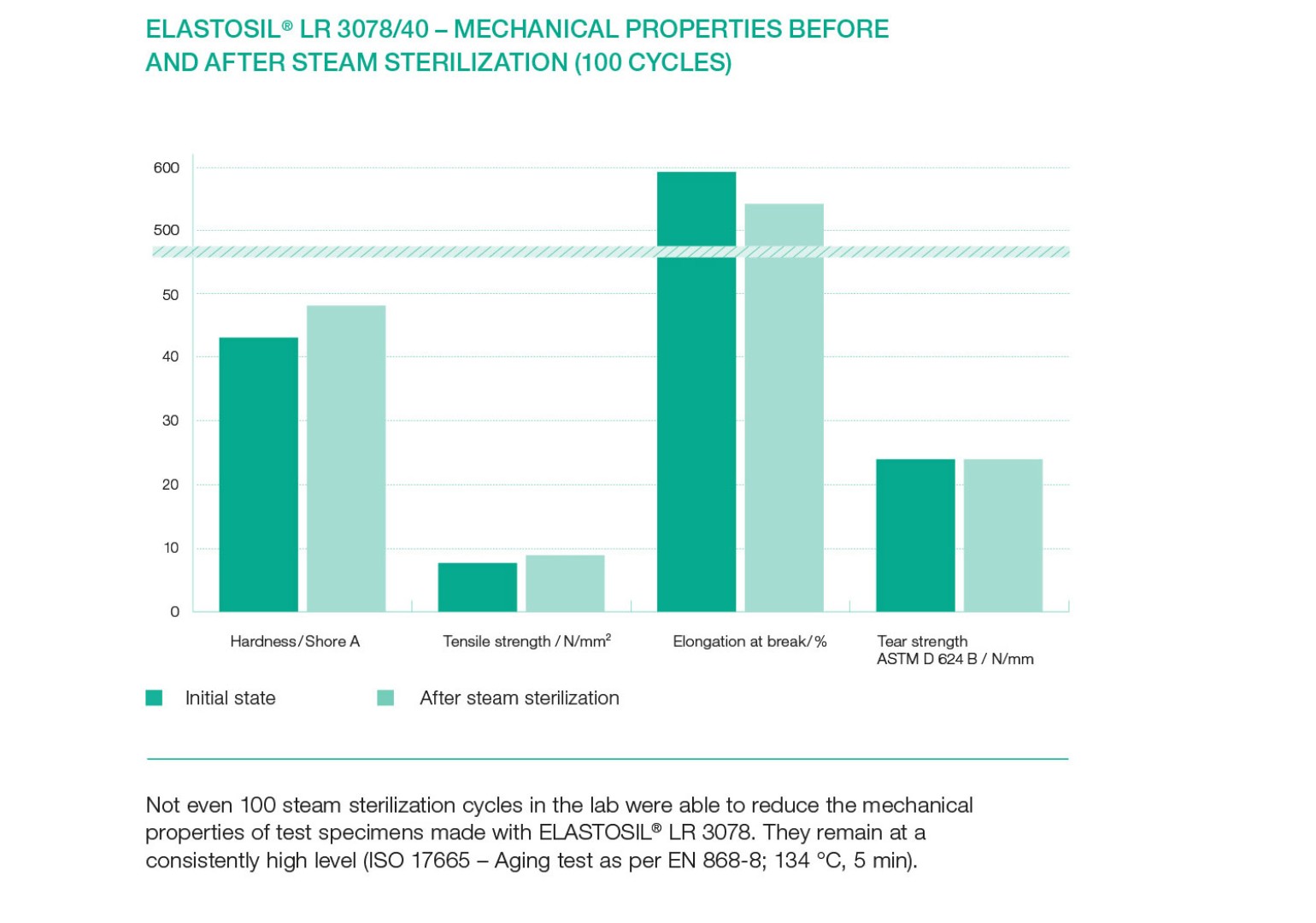
Cured rubber made from ELASTOSIL® LR 3078 is biocompatible, as demonstrated by various tests meeting ISO 10993 and United States Pharmacopeia (USP) Class VI standards. The materials have been tested in accordance with ISO 10993 for their cytotoxicity, pyrogenicity and sensitizing properties. And their acute systemic toxicity, intracutaneous toxicity, and short-term implantation have been assessed under USP Chapter <88> Class VI. Plus, the new self-adhesive technology does not contain any bisphenol A structures at all. WACKER’s decision to dispense with this class of substance is helping to boost the occupational safety aspects of the production and processing of the silicone rubbers while also serving to protect consumers.
What is more, polycarbonate/silicone combinations made with ELASTOSIL® LR 3078 and the right polycarbonate grades can be steam-sterilized, because the mechanical properties of silicone remain virtually unchanged even after 100 sterilization cycles involving exposure to steam heated to 134 °C.
They also continue to adhere well to Apec® 1745 after 100 cycles (5 minutes at 134 °C). Thus, ELASTOSIL® LR 3078/40, for instance, only exhibits a slight reduction in peel-force values after more than ten sterilization cycles. And, although the failure mode switches to adhesive failure once 50 cycles have been exceeded, the peel forces after 50 and 100 cycles, respectively, are still high, at 10 newtons per millimeter.
“A chemical bond created by ELASTOSIL® LR 3078 to polycarbonate offers considerably more design freedom than traditional mechanical joining techniques involving interlocking openings and undercuts,” says laboratory manager Dr. Liesener. In addition, the chemical bond prevents gaps from arising between the hard and soft components, where dirt can collect, or bacteria and mildew can form colonies.
Because it is a biocompatible and steam-sterilizable material, ELASTOSIL® LR 3078 is perfect for medical applications. The cushion in a respirator or anesthesia mask, for example, can be made with a soft grade from the ELASTOSIL® LR 3078 series. This kind of cushion molds perfectly to the facial contours, creating a reliable seal. Possible applications lie in automated drug-delivery systems that deliver active ingredients in the required dosage, or in devices for minimally invasive examinations and surgery.
But other industries, too, such as the automotive industry, stand to benefit from injection-molded combinations made of polycarbonate and silicone. Possible automotive applications are transparent covers with integrated sealing lips and transparent components for ambient interior lighting.
“No matter where our new self-adhesive silicones are used, they can serve to turn product ideas that were previously unthinkable into reality,” sums up marketing manager Dagmar Rische.
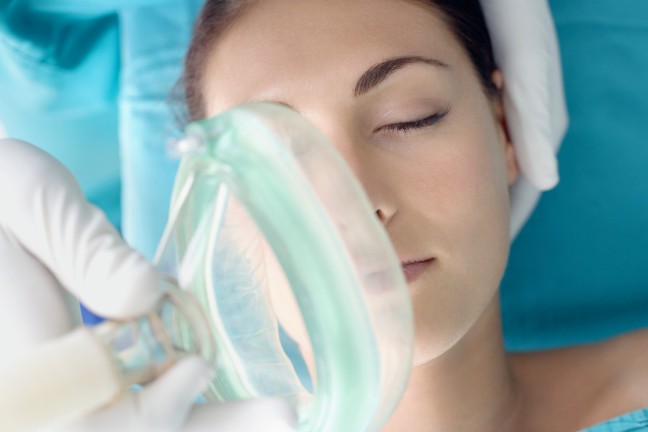
Respirator masks made with ELASTOSIL® LR 3078 fit snugly over the face thanks to the soft silicone component. What is more, the silicone creates a perfect seal.
Contact
For more information on this topic, please contact:
Mr. Dr. Florian Liesener
Industry Manager
Construction Solutions
+49 8677 83-3566
Send message