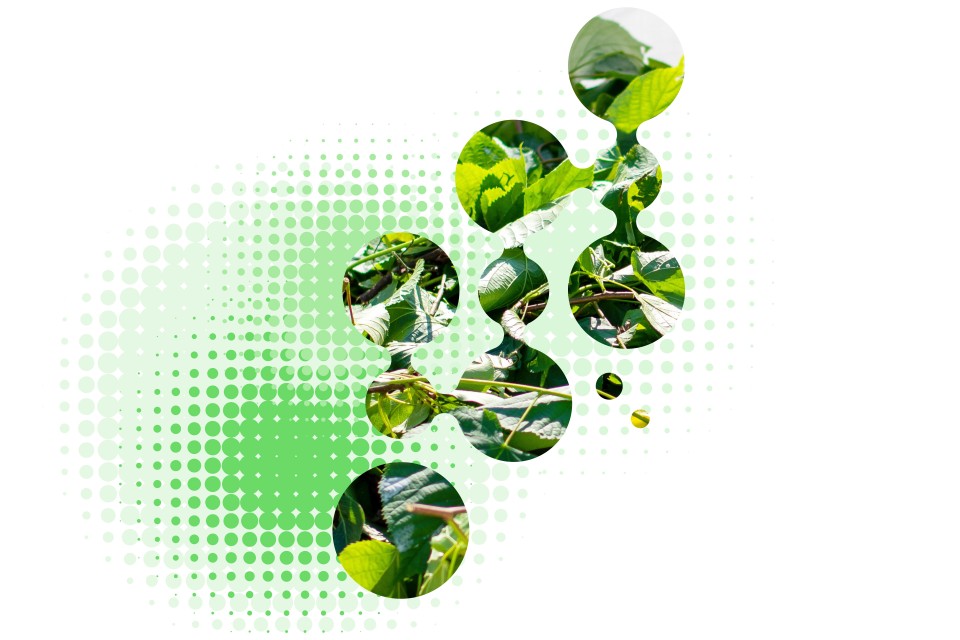
Renewable Raw Materials
Oct 06, 2022 Read time: approx. MinutesMinute
Eight New Additions
WACKER’s eco silicones are considered particularly resource-efficient since they use biomethanol from waste vegetable matter in the production process. The silicone rubber brands ELASTOSIL® and SILMIX® are now also available as eco products.
The chemical industry is committed to continuously reducing its use of fossil raw materials. One strategy here is to replace these with identical materials from renewable resources – an option best implemented using the mass balance approach. This method allows manufacturers to process raw materials from fossil-based and renewable sources at the same time, later assigning them to specific products according to the proportions in which they were used. The mass balance approach ensures that the “bio-based” label is applied only to those products that can be verified as being based on renewable raw materials.
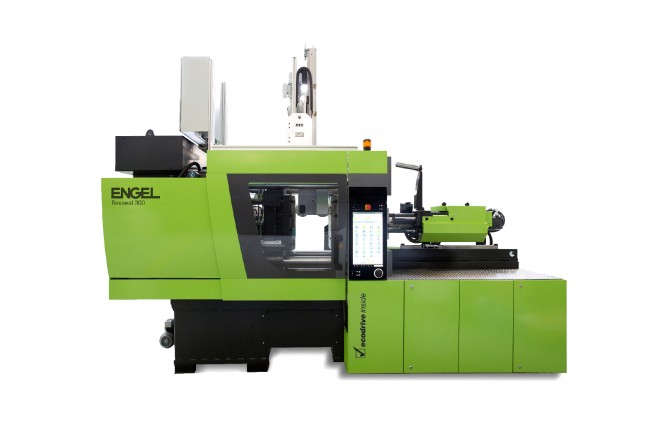
WACKER will use this Engel injection-molding machine at the K 2022 tradeshow to produce lemon presses from a biomethanol-based, food-grade silicone rubber.
The most important raw materials for silicone manufacturing are silicon and methanol. Methanol is first converted to methyl chloride and then reacted with elemental silicon via the Müller-Rochow process to form a mixture of various methylchlorosilanes – intermediates that play an important role in the production process.
In 2018, WACKER began producing methyl chloride from methanol it had generated from both petrochemical and plant-based resources, always applying the mass balance approach to the amount of biomethanol used. The method that WACKER employs for its mass-balanced products is certified at regular intervals by TÜV Nord in accordance with the REDcert² standard, ensuring that the amount of eco product sold always corresponds to the amount of biomethanol that goes into the process.
The mass balance approach is suitable for ready-to-use silicone products containing pigments or other organic additives. Such additives can be similarly offset by incorporating corresponding amounts of biomethanol. The REDcert² standard stipulates the exclusive use of raw materials obtained from renewable sources. The biomethanol in these processes is derived exclusively from plant residues suitable neither for food production nor as animal feed.
The first biomethanol-based silicones to be launched by WACKER in 2018 were silicone fluids and defoaming agents. Silicone sealants followed in 2020. Now, the ELASTOSIL® eco family, too, can announce new members.
“We can convert other silicone rubber products over to biomethanol at any time upon request.”
Dr. Martin Bortenschlager, Engineering Silicones
The New “eco” Silicones
Some eight silicone rubber alternatives based on biomethanol have been available since the fall. The first liquid silicone rubber to leave the starting gate is ELASTOSIL® LR 5040. The eco version (ELASTOSIL® eco LR 5040) of this extremely tear-resistant, non-postcuring grade will be available for order in six different hardness values. Customers wanting to conserve resources can choose between two lines of solid silicone rubber as well: peroxide-curing, general-purpose ELASTOSIL® R 401 (ELASTOSIL® eco R 401, hardness Shore A 40) and addition-curing, exceptionally tear-resistant solid silicone ELASTOSIL® R plus 4020 (ELASTOSIL® eco R plus 4020 with hardness Shore A 40).
WACKER also offers biomethanol-based solid silicone compounds on request; these are ready-to-use mixtures marketed under the SILMIX® eco brand name. Throughout the K 2022 international tradeshow, the processing of the SILMIX® eco R plus TS 40002 solid rubber compound will be demonstrated live at the WACKER booth from 9 a.m. to 6 p.m. on an Engel injection-molding machine (mold: Nexus; part design: Lékué).
“We can now offer our customers eco versions of two multipurpose solid silicone rubber grades and one non-postcuring liquid silicone rubber grade for exceptionally sensitive applications,” explains Dr. Martin Bortenschlager, director of WACKER’s Engineering Silicones business team. He has been aware of the increasing interest in resource-efficient, and hence more sustainably manufactured, products for some time and can therefore readily imagine an expansion of the eco portfolio. “Our first step was to demonstrate that we’re capable of offering resource-efficient versions of rubber products and of silicone compounds formulated to customer specifications. But that's just the beginning. We can also convert other products over to biomethanol at any time upon request.”
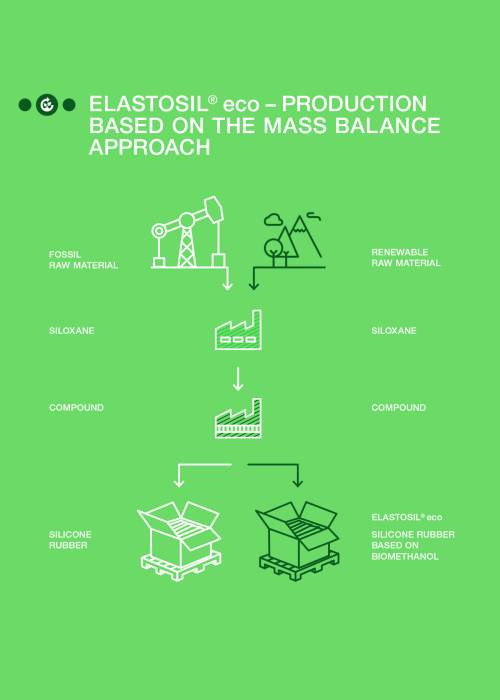
Making the switch to the new eco product line is straightforward, incidentally. Because methanol and biomethanol are chemically identical, the silicone expert points out, there is no difference between ELASTOSIL® and ELASTOSIL® eco products. “You can test out ELASTOSIL® eco whenever you want without having to run a complex, expensive series of tests. The properties of our biomethanol-based silicones are the same as those of fossil-based products, which means the processing techniques involved are identical too.”
Contact
For more information on this topic, please contact:
Mr. Dr. Martin Bortenschlager
Director Business Team Engineering Silicones
Rubber Solutions, WACKER SILICONES
+49 89 6279-1982
Send message