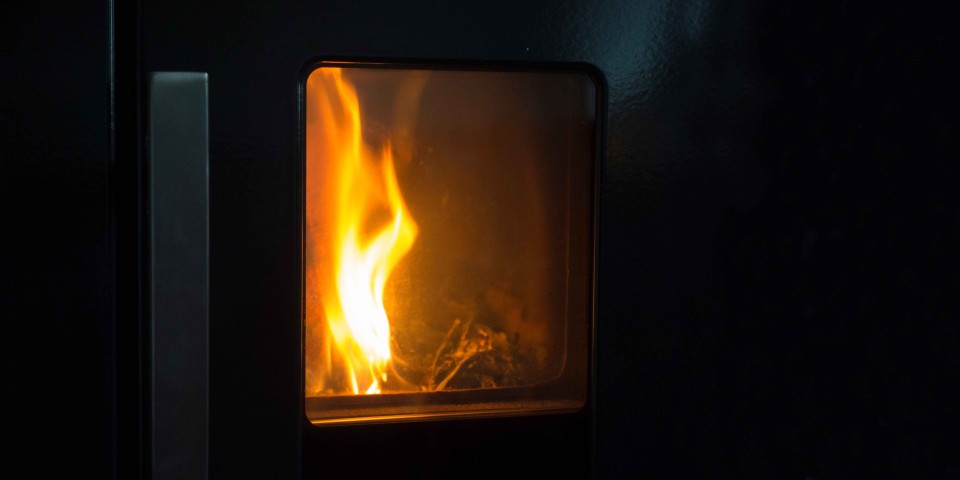
Heat-resistant coatings
Mar 09, 2023 Read time: approx. MinutesMinute
Turn up the Heat
Silicone-based paints and coatings withstand temperatures of up to 600 °C. WACKER now presents two new binders for heatresistant coatings: SILRES® M 51 E and SILRES® IC 900. Manufacturers can use these to expand their portfolios to include water-based coatings, as well as both high-solids and high-build formulations.
When Germans want to say that something is less valuable or attractive than it used to be, they say “the paint’s come off.” And for commercial goods, a flawless surface with a high-quality coating is indeed a sign that the product works as it should and has high value. But for this to be the case, a coating has to be fine-tuned to the surface on which it is applied and to the environmental conditions – heat, for example – to which it will be exposed when the product is used. Specialized, heat-resistant coatings lend themselves well here. After all, unsuitable coatings would flake off from the substrate or be destroyed by oxidation after a short time.
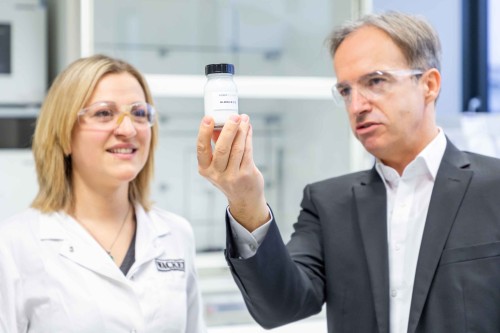
Sabine Hanke and Christian Putz check a test filling of SILRES® M 51 E, which is a water-based formulation.
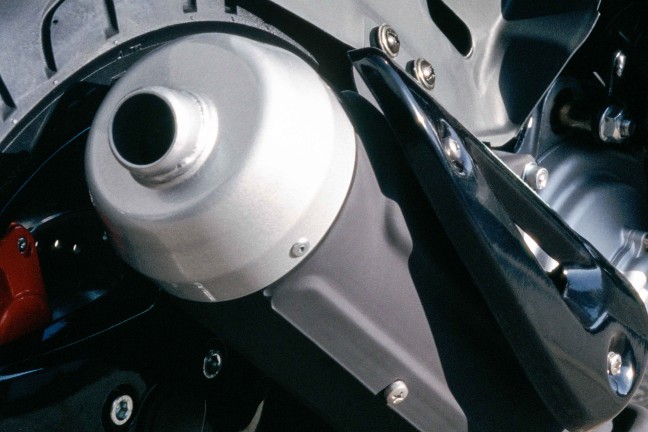
Coatings formulated with this material nevertheless adhere excellently to metallic surfaces such as steel or aluminum after baking, making them ideal for applications such as exhaust systems.
Heat-resistant coatings are needed in automotive engineering and the process industry, as well as in private households. In many vehicles, for example, heat-stable coatings are applied to the exhaust system and to various parts mounted close to the engine. Piping, furnaces, flues, smokestacks and heat exchangers in industrial processing plants need to be protected from high temperatures and, in most cases, from the elements. And in households, heat-resistant paints ensure that stoves, stove pipes, chimneys, water heaters, stove tops, barbecue grills and raclette sets still work well and look good after years of service.
For applications like these, WACKER will be presenting two innovative silicone resin binders to a broad industry audience at the 2023 European Coatings Show: SILRES® M 51 E, which is suitable for formulating waterbased coatings, and SILRES® IC 900, which is processed by conventional methods – using organic solvents – and can be used in high-build and high-solids coatings alike.
30 minutes is the time it takes for SILRES® M 51 E to crosslink at temperatures of 220 °C to 260 °C and form a strong bond with the surface to be coated.
Reducing VOC emissions
Many of the solvents still commonly used in the paints and coatings industry are volatile organic compounds (VOCs). “The use of organic solvents has come under increasing scrutiny, however, and is subject to government regulation as well,” says Philipp Haas, marketing manager for Performance Solutions at WACKER SILICONES. “This is putting the paints and coatings industry under intense pressure to reduce the use of solvents in their products.”
For companies working to comply with more stringent government regulations, water-based coatings represent an excellent alternative to conventional solvent-based products. This also applies to heat-stable liquid coatings. Among coating systems designed for high-temperature applications, liquid coatings hold a market share of over 80 percent. “But only a relatively small portion of heat-stable liquid coatings are currently water-based,” Haas explains. “Part of the reason is because there weren’t any suitable binders for those kinds of coatings.”
When WACKER comes to ECS 2023, it will unveil SILRES® M 51 E, a new aqueous, emulsion-based silicone resin binder promising relief. “Silicone resins like these, which are used as binders in heat-resistant coatings, generally crosslink at elevated temperatures to form a tough film that can withstand high temperatures,” explains Christian Putz, who heads up an applications laboratory for the Performance Solutions business unit of WACKER SILICONES. “That’s why as binders, they play the key role in curing the coating.”
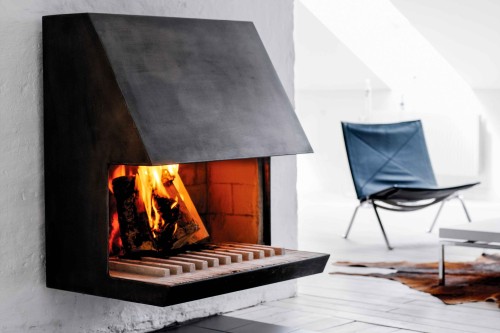
In combination with the right metallic materials and depending on the pigments used, silicone-resin-based paints can withstand temperatures of up to 600 °C, which can arise in applications such as wood-burning stoves.
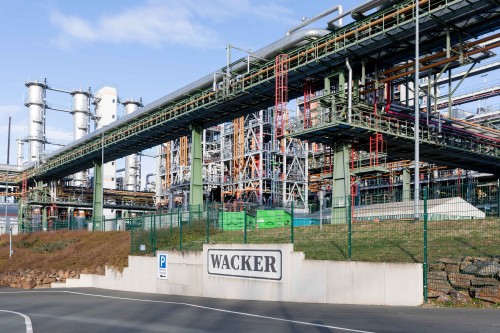
Pipelines in chemical plants need to be highly resilient and they have hard-to-access geometries – this is why they are obvious candidates for high-build coatings.
SILRES® M 51 E cures over a period of 30 minutes at 220 °C to 260 °C. The silicone resin envelops the solid particles present in the coating – pigments and fillers – and binds them, both to each other and to the substrate. “That produces a strong coating,” says Putz, “which protects the treated object against external influences.”
After crosslinking, cured silicone resins are characterized by their extended, close-meshed silicon-oxygen backbone, i.e., by their silicone- resin network. Organic components – generally methyl and/ or phenyl groups – bond to this inorganic foundation, which exhibits extraordinary chemical stability. The organic groups’ key influence is on the coating’s properties before baking.
Pure methyl resins are also notable for their exceptional hardness, excellent mechanical resistance and very good resistance to chemicals and the elements. Thanks to their high concentration of inorganic components, products like these also develop far less smoke the first time they are heated than is the case for binders containing large quantities of organic components.
Methyl silicone resins have been used as binders in conventional heat-resistant, solvent-based coatings for a long time. The new SILRES® M 51 E coating binder likewise contains this type of silicone resin, which is finely dispersed in the form of tiny droplets within an aqueous medium.
What is new about this methyl silicone resin for heat-resistant applications is its form, Putz points out. As the WACKER developer explains, “By using suitable emulsifying systems and selecting just the right silicone raw materials, we’ve managed to formulate an emulsion with excellent storage stability.”
SILRES® M 51 E, which has a solids content between 50 and 53 percent, can be easily incorporated into coatings using familiar processes. Application testing carried out at WACKER laboratories in Burghausen show that SILRES® M 51 E is highly suitable as the sole binder for the manufacture of heat-stable coatings. Aqueous formulations of the new binder are tack-free after only about 20 minutes at room temperature.
After baking, example formulations of black paint were capable of withstanding temperatures between 550 °C and 600 °C. “These baked coatings adhere exceptionally well to metal surfaces like steel or aluminum,” Putz observes, summing up their advantages. “They exhibit very good chemical and abrasion resistance, lose hardly any gloss after exposure to thermal stress and stay hard, even in the heat. In other words, in terms of in quality, their technical properties are similar to those of heat-resistant coatings formulated with traditional, solvent-based silicone resin binders.”
Active ingredient in pure form
When a coating has to be highly resilient and processing conditions are difficult, for example, protecting chemical plants with complex geometries against corrosion, so-called high-build coatings are used. “High-build coatings do an especially effective job of protecting the metal substrate and are easier to use than conventional coatings, which have to be applied in relatively thin layers that can’t vary in thickness,” Haas explains. High-build coatings, in other words, make jobs such as maintenance work easier to carry out, especially in places that are difficult to access. For applications like these involving solvent-based, heat-resistant coatings, WACKER has developed SILRES® IC 900 – a pure, undiluted active ingredient that, depending on the application and the coating formulation, will crosslink at temperatures between 100 °C and 280 °C.

Sabine Hanke tests a black coating example formulation applied to sheet steel in the laboratory oven to see what temperatures silicone resin coatings can withstand.
“With SILRES® M 51 E and SILRES® IC 900, WACKER is unveiling two new developments that our customers can use to reduce the amount of solvent in their products.”
Christian Putz, Application Engineering, WACKER SILICONES
“Our methyl phenyl silicone resin is notable for its molecular structure, which forms a close-meshed network upon crosslinking, but which still exhibits a certain degree of flexibility,” explains Putz, whose applications laboratory was where these silicone resin grades were developed. "This flexibility prevents cracks from forming in the cured coating layer under thermal stress.” SILRES® IC 900 can therefore also be used to formulate coatings that are applied in thick layers. “SILRES® IC 900 marks the first time that the paints and coatings industry will have access to a silicone resin binder for high-temperature applications that will permit dry-film thicknesses of over 100 micrometers,” stresses Putz.
Thanks to its low viscosity, this alkoxy-functionalized methyl phenyl silicone resin can be used not only for formulating high-build coatings – it is suitable for developing high-solids coatings as well. These coatings, which have a solids content of over 80 percent and contain correspondingly low amounts of solvent, can be prepared as either one- or two-component formulations. Upon curing, they are highly resistant to chemicals, and their color remains stable. “In other words, with SILRES® M 51 E and SILRES® IC 900, WACKER is simultaneously unveiling two new developments that our customers can use to reduce the amount of solvent in their products,” says Putz, underscoring the achievement.
Contact
For more information on this topic, please contact:
Mr. Philipp Haas
Senior Marketing Manager Performance Solutions
WACKER SILICONES
Send message