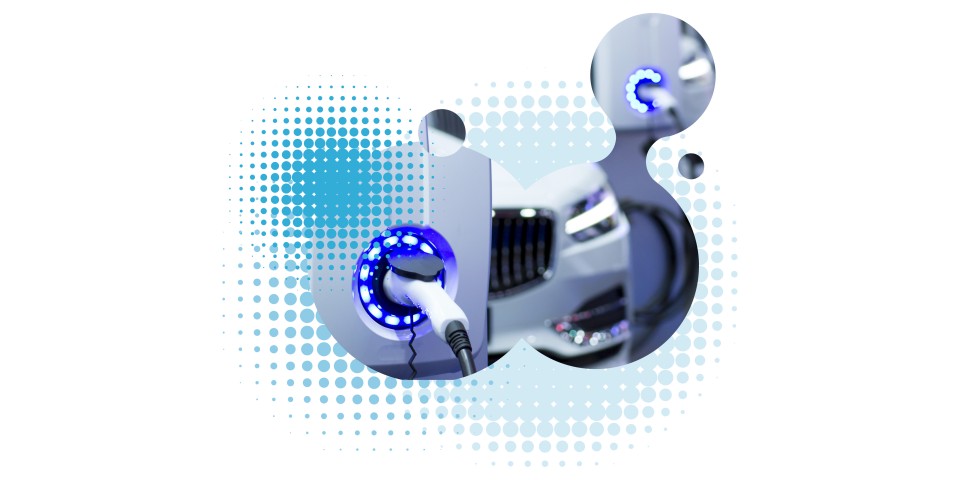
E-Mobility
Electrical connectors, thermal interface materials and two-component parts
Oct 04, 2022 Read time: approx. MinutesMinute
Materials Simply Made for EVs
Electric vehicles (EVs) are boosting automotive-sector demand for high-performance materials – and that means silicone elastomers. These resist high temperatures and charging currents, do an excellent job of conducting heat and reliably seal components over the course of many years. Here we present an overview.
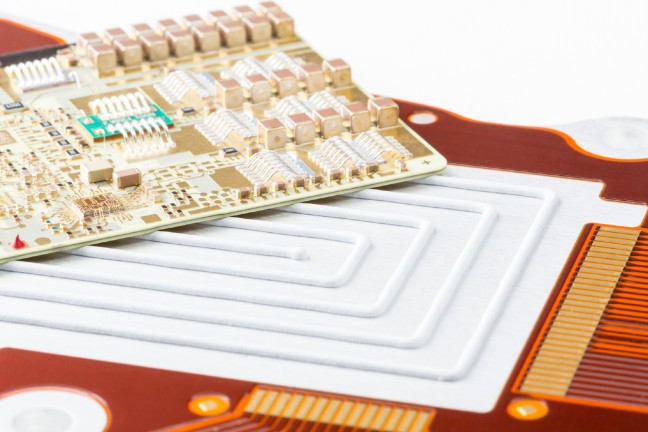
Thermally conductive silicone gels make ideal gap fillers, taking the waste heat produced by electronic components and dissipating it efficiently to a heat sink.
In 1964, a typical car made do with 180 meters of cables and a couple of connectors. By contrast, today’s models, whether hybrid or fully electric, contain 3,000 meters of the former and up to 200 of the latter. With the growing electrification of vehicles, it is not just the number of cables, on-board electrical systems and electronic control elements that is growing, but also the demands imposed on these components and their constituent materials.
Through its portfolio of ELASTOSIL®, SEMICOSIL® and WACKER SilGel® silicone rubber compounds, WACKER offers a wide range of solutions for meeting the challenges facing the automotive industry as it transitions to electromobility. The fact that its Burghausen (Germany) and Zhangjiagang (China) production sites are IATF 16949 certified for certain parts of the company puts WACKER in a position to supply automobile manufacturers with silicone products directly.
“The unique properties of silicones have an important role to play in electromobility and, it follows, in sustainable transportation for the future,” says Dr. Martin Bortenschlager, head of the WACKER SILICONES Engineering Silicones business team and responsible for the regions of Europe, Middle East, Africa and Latin America. “Silicone rubber compounds do more than just make electric vehicles more reliable – they make them last longer too. They also reduce the need for repairs and replacement parts, which helps prevent waste. And on top of that, their ease of processing supports automated mass production.”

Electrical Connectors
Electrical lines have to be connected and disconnected during assembly and maintenance work. The fastest and most reliable way to do this is with electrical connectors. These often have a silicone seal to prevent ingress of moisture, dust and de-icing salt. The most common seals are single-wire, radial and mat types.
For applications like these, WACKER offers both liquid and solid silicone rubber products that continuously bleed silicone fluid after they have cured. Also available are products with oil-free yet lubricating surfaces. These are perfect for electric vehicles.
The products in the ELASTOSIL® LR 38xx line are of the oil-bleeding type and can be used to reliably seal connectors. These liquid silicone rubber products can be processed by injection molding. Just shortly after curing, the rubber starts exuding a thin fluid film, yielding lubricating properties that make it easier for the connector to slide into the desired mounting fixture. ELASTOSIL® LR 38xx products offer low-temperature flexibility and heat resistance and can be used in the range from -55 to +210 °C. These liquid silicones also contain very little in the way of volatiles, an achievement made possible by the ultramodern processing technologies used by WACKER during production.
Alternatively, automakers that do not wish to use oil-bleeding elastomers, yet are keen to mount their connectors efficiently in a fully automated process can make use of silicone products with low coefficients of dynamic friction, such as ELASTOSIL® LR 3065. Another option for connectors is ELASTOSIL® LR 3005.
This is the ideal product whenever a low coefficient of friction is not absolutely necessary. All the aforementioned products have low compression set at high service temperatures, even when non-postcured. Postcuring is therefore superfluous.

When in use, the lithium-ion batteries in EVs generate vast quantities of heat that have to be dissipated by means of thermally conductive silicones.
Batteries – New Approaches to Performance and Safety
With the growing adoption of electric vehicles, battery makers face numerous challenges when it comes to improving battery performance and safety. The focus of attention here is on the following fundamental aspects:
— The batteries must be compatible with high-volume, cost-efficient assembly and mass-production processes.
— For efficient thermal management, innovative approaches have to be found. Keeping the cells at their ideal temperature is central to the safety and durability of a vehicle battery. And is the only way to ensure optimum performance.
— Safe operation must be ensured even if extreme events occur. This includes thermal runaway in the battery.
WACKER offers various silicone solutions for keeping the battery temperature within the optimum range, for boosting battery safety generally, and especially for preventing thermal runaway.
Gap Fillers Prevent Premature Battery Failure
Electric vehicles frequently employ lithium-ion batteries as their power source. These are usually installed below the passenger compartment, where they occupy most of the floor space. A thermally conductive gap filler is needed to provide thermal coupling between the battery modules and the heat-dissipation system. It must be aging-resistant to prevent premature battery failure and must lend itself to rapid application to large surfaces.
One particular challenge consists in ensuring that the bottom of the battery cell fits tightly to the heat sink. The resulting narrow gap of a few hundred micrometers has to be completely bubble-free in order that the heat may dissipate unhindered. For this, WACKER has developed a flowable gap filler that can be injected quickly and yields perfect results even on large areas, thereby facilitating high-speed industrial production.
High Outlay on Fire Safety
Automakers go to great lengths to ensure the safety of their electric vehicles, especially of their batteries. They install flame-resistant fire-protection mats and coatings to prevent heat and flames from raging through the vehicle in the event of a battery fire. However, current safety strategies have advantages and disadvantages. Fire-protection mats, for instance, take up more space than intumescent coatings. These, for their part, are designed to swell up extensively in the event of a fire, and that could cause damage to individual cells.
WACKER is currently contributing to battery safety by developing an innovative coating that meets all the technical and safety aspects of fire protection, efficient use of space and process-automation needs. The coating is a novel silicone rubber blend that is applied to the internal face of the battery housing and ceramifies completely when exposed to heat. Although it is is just a few millimeters thick, the ceramic layer can withstand temperatures higher than 1,000 °C. Should thermal runaway occur, a coating like this protects the housing and so boosts vehicle safety substantially.
Cables
Voltage, charging currents and the resulting waste heat of battery-operated vehicles are constantly on the rise, with voltages of up to 800 V and charging currents of up to 350 A no longer uncommon. To make cables, the automotive industry therefore needs extrudable materials that will reliably retain their electrical insulation properties over a very broad range of temperatures and over long periods of time. It applies very high standards: the only cables that may be installed are those that can be used for at least 3,000 hours at temperatures between 180 and 200 °C.
Silicones such as ELASTOSIL® R plus 4305, a rapid-curing, two-part, solid silicone rubber compound, are an ideal fit for applications such as these. When formulated with a corresponding heat stabilizer, the product can withstand temperatures of up to 200 °C, without substantial changes in either the mechanical properties or the electrical characteristics of the elastomer.

Thermal Interface Materials
Efficient heat management of components is a pressing issue in electric vehicles. One reason for this is the increasing level of miniaturization and the resulting higher energy densities. Among the important roles that they play, thermal interface materials fill the gaps between heat-generating assemblies and the heat sink, taking the place of air, which is a poor heat conductor. Silicones filled with inorganic heat-conducting materials are ideal for this task, as their properties remain virtually unchanged at temperatures ranging from -45 to +180 °C. They also resist aging and act as flame retardants.
The SEMICOSIL® 96xx TC line of room-temperature-curing silicone rubber products, for instance, is suitable for the thermal coupling of printed-circuit boards to a heat sink. They are easy to dispense and can be applied in no time to large surface areas – and without any flaws. This renders them perfect for coupling battery modules to a heat-dissipation system, even in a mass-production scenario. Depending on the specific design involved, thermal gap fillers such as SEMICOSIL® Paste 40 TC are suitable for fixing and cooling components, while thermally conductive adhesives such as the SEMICOSIL® 97xx TC line create a thermal coupling between components and the heat sink in question.
The power control units in EVs, in particular, are becoming increasingly compact and energy-dense, and are generating more heat. This needs to be removed efficiently if the components are to stay at the desired operating temperature. Thermally conductive compounds such as ELASTOSIL® RT 76xx TC are a new class of materials for encapsulating or immersing printed-circuit boards fitted with discrete devices, such as transformers, chokes, coils and other electronic components.
Seals in Fuel Cells
The debate surrounding sustainable drive trains is currently focused on battery-powered electric vehicles. But there are other drive designs that may equally serve the purpose of electromobility in the future. One such example is fuel cells. These are attractive because they make it possible to achieve a long range. They are already the preferred sustainable alternative to ICE trucks, because they enable drivers to transport loads over long distances, which is not the case for battery-powered vehicles.
Such a system consists of single fuel cells connected together through what are known as bipolar plates. WACKER supplies specially developed silicone rubber grades for sealing these plates: ELASTOSIL® LR 3025 for injection molding and room-temperature-curing ELASTOSIL® RT 624 for dispensing. Both silicone rubber compounds are characterized by extremely low compression set – even when in contact with coolants.
Die-cut seals made from ELASTOSIL® Film 624 represent an additional option. Consisting of ELASTOSIL® RT 624, these silicone rubber films are produced with incredible precision to thicknesses between 150 μm and 400 μm. Deviations from target thicknesses amount to less than 5% across the entire range. This, along with the typical silicone properties of the film, makes the product very attractive to fuel-cell manufacturers.
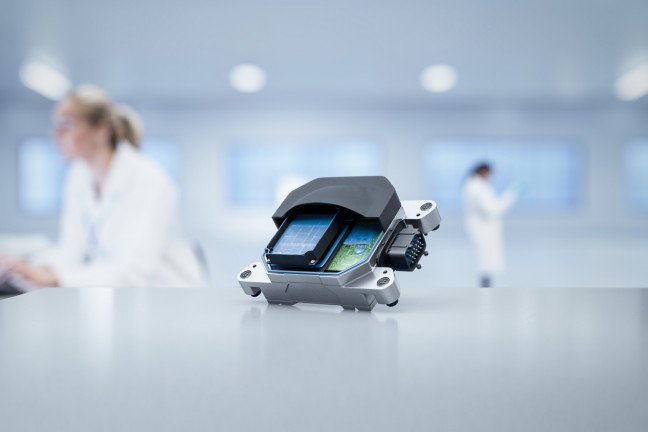
Silicone encapsulants reliably protect sensors and sensitive electronic components in vehicles against vibration, dirt and moisture.
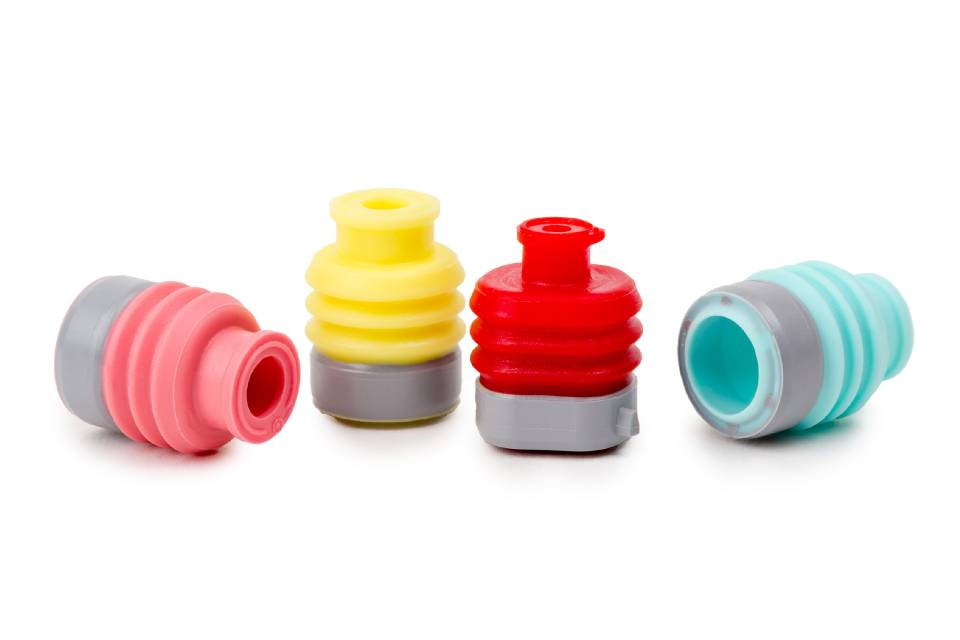
Two-Component Parts
Thermoplastics such as polyamide and polyester can be combined in an injection-molding machine with liquid silicone rubber for an efficient method of producing multicomponent parts in which the silicone performs a sealing or protective function. For this to work, however, the liquid silicone has to adhere perfectly to the thermoplastic.
ELASTOSIL® LR 3070 and its oil-bleeding counterpart ELASTOSIL® LR 3072 are ideal for this application. Because they adhere well to many metals, they open the door to cost-effective production of metal-silicone-elastomer components, even on a large scale.
Contact
For more information on this topic, please contact:
Mrs. Claudia Berghammer
Senior Marketing Manager
Engineering Silicones
+49 8677 83-86745
Send message