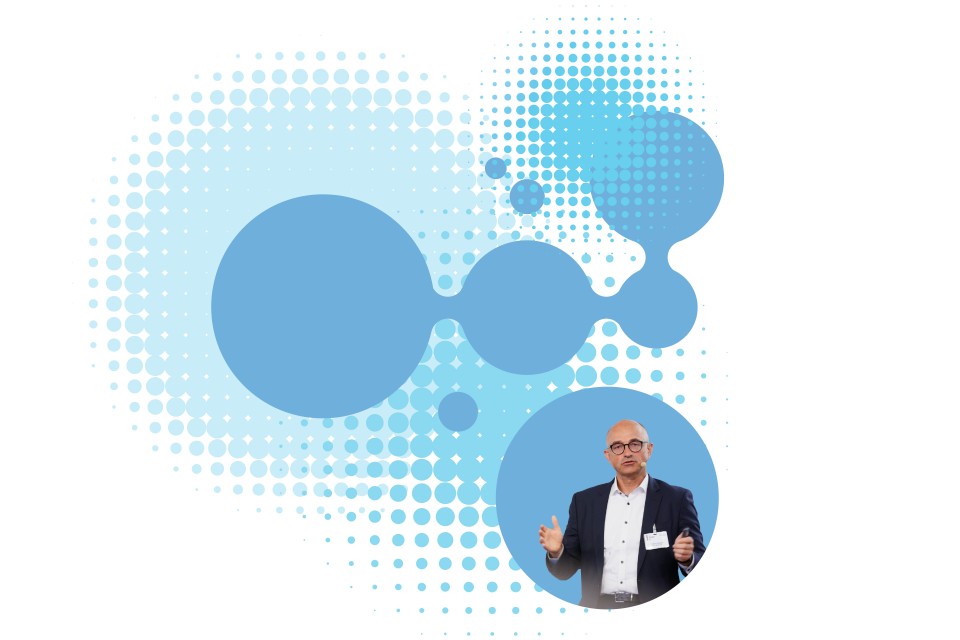
Strategy
Interview with Dr. Robert Gnann, head of WACKER’s silicones business
Silicones Are Enablers
Dr. Robert Gnann, head of WACKER’s silicones business, talks about the planned capacity expansions and the indispensable role of silicones in mitigating climate change.
WACKER Magazine: For about two years now, demand for silicones has outstripped supply – on markets all around the world. Naturally, this is a highly unsatisfactory situation for those customers that rely on these materials. How is WACKER, the world’s second-largest silicones manufacturer, responding to the shortage of installed capacity?
Dr. Robert Gnann: By accelerating growth. The WACKER Group, and especially its silicones business, has performed very positively in recent years. The company is on a sound financial footing and has plans to turbo-charge growth all over the world. A number of expansion measures have been launched in the recent past. For example, over the next several years, we will be investing 100 million euros alone in expanding our solid and liquid silicone rubbers production capability. By the end of the decade we intend to have installed enough new capacity to have doubled our divisional sales.
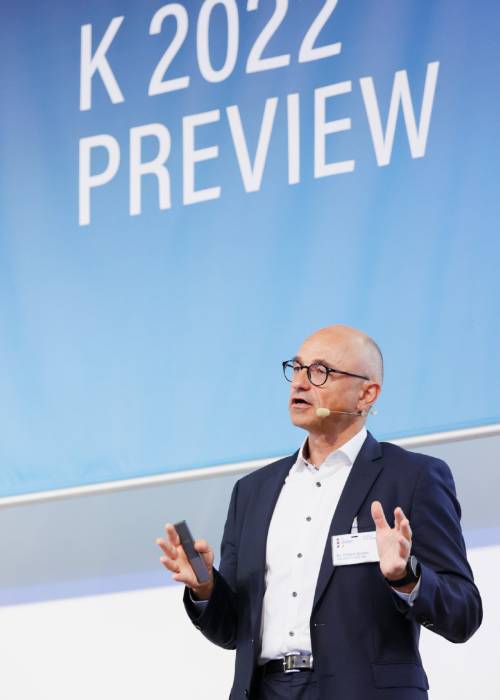
Dr. Robert Gnann, a chemist, has been president of WACKER SILICONES, the company’s largest division, since 2016.
“By the end of the decade, we intend to have doubled our divisional sales.”
Dr. Robert Gnann, President of WACKER SILICONES
The 100-million-euros program is essentially aimed at downstream capacity. What is the situation with upstream production, where precursors are involved, i.e. silanes and siloxane?
We are drawing up plans for the long-term construction of a new fully integrated site in Charleston, Tennessee, in response to the equally strong demand growth we are seeing for silicones in the USA. This is initially likely to take the form of midstream and downstream investments in the order of 200 million dollars. Some of that will be earmarked for high-performance rubber compounds and silicone sealants. We already have a production facility for polysilicon and HDK® pyrogenic silica in Charleston and so the prerequisites for an efficient silicones production setup are already in place.
Which silicone products are in particularly short supply on the market at the moment?
There is a particular shortage of liquid silicone rubber and high-consistency, i.e. solid, silicone rubber compounds in the Americas and Europe as well as in parts of Asia. Our expansion plans are designed to address precisely this need. Additional capacity has now become available at our production site in Burghausen and, from next year, expansion measures at our Adrian site in Michigan, USA, will come into play as well.
What about high-consistency rubber?
Availability will improve here, too. We will still need a little more time for major capacity expansions in solid rubber. But we have introduced measures at short notice to eliminate bottlenecks. Our new production site in Panagarh in India set the ball rolling on the expansion of capacity for high-temperature-curing (HTV) silicone rubber in July. Additional quantities will come on stream early next year at our sites in the Czech Republic and Japan. And our big integrated site in Zhangjiagang, China, will be in a position to deliver even more HTV from 2024 on. Taken all together, this 100-million-euro investment will enable us to match the growth of our elastomer customers and to achieve double-digit growth for several years to come.
“I would even venture that, without silicones, we would find it hard to reach our climate goals.”
Dr. Robert Gnann, head of WACKER’s silicones business
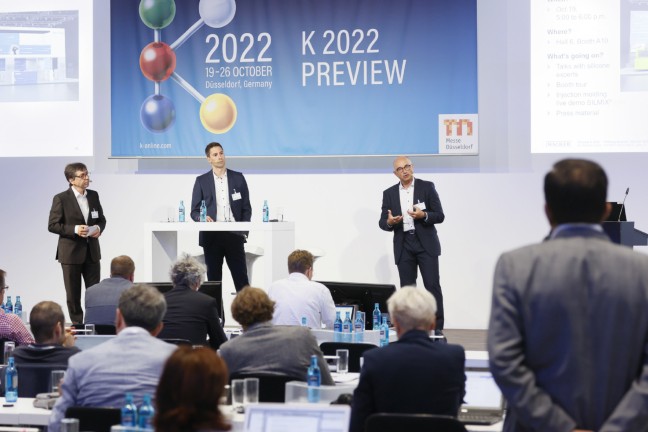
Dr. Robert Gnann (3rd from left) at a preview event where WACKER unveiled its innovations for the K 2022 plastics and rubber tradeshow to journalists.
Where will WACKER rank in the silicones market when these expansion stages are complete?
By carrying out these measures, we are consolidating our position as the global number two in the silicones business and investing more particularly in the production of high-quality silicone specialties that are tailored to the specific needs of our customers. Our goal is also to be the number one in high-consistency silicone rubber. While some of our competitors are disengaging more and more from this market, we are resolved to keep investing in quality and new capacity. Our products are formulated to contain up to 35 percent by weight HDK® pyrogenic silica. That is what makes our HTV products among the best in their class. WACKER is the only major silicones supplier to have its own vertical integration and a strong proprietary technology for pyrogenic silica in this area. For HDK®, we can call on capacity in Europe, China, and the USA.
Is WACKER SILICONES investing primarily in the elastomers business?
In general, our plans for expansion extend much further than elastomers. Specialty silicones are being rigorously expanded across all areas and in all regions. We will be the ones supplying the requisite raw materials and precursors. The acquisition of SICO in China, which produces organofunctional silanes, has also strengthened many areas of our specialty additives portfolio, e.g. our specialty adhesives business.
What supply chain challenges is WACKER currently facing?
In principle, the same ones as our customers and competitors. We are struggling with rising energy and raw-material prices, reduced transport capacity, unreliability and longer transport times. However, we are fortunate in having our own plant in Holla, Norway, which covers a substantial amount – roughly one third – of the silicon metal we need for producing silicones and polycrystalline silicon. This makes us less vulnerable to supply problems and rising prices for this key raw material. And, we are even planning to expand capacity there as well – right at the start of our supply chain.
By how much?
We have commissioned a feasibility study for a new furnace in Holla that will boost the site’s capacity for metallurgical-grade silicon by about 50 percent, relative to its current level. We are also looking into ways of replacing the coal used as a reducing agent in the manufacture of silicon metal with renewable materials, such as charcoal or pellets. The goal here is to save up to 430,000 metric tons of CO2 a year in Holla. So, our Norwegian site, too, has quite a key role to play in helping WACKER reach its sustainability goals. Ultimately, we intend to have halved the entire company’s greenhouse-gas emissions in absolute terms by 2030.
Sustainable processes in production are one aspect. What about the product aspect and the contribution which silicones make to sustainability and to mitigating climate change?
Silicones rank among the most important enablers of climate-change mitigation. I would even venture that, without silicones, we would find it hard to reach our climate goals. Silicones are employed in many key industries and are simply irreplaceable when it comes to the development of innovative, sustainable technologies. This applies as much to wind power and photovoltaics, where silicones seal and protect parts and components, as it does to electromobility, consumer electronics and areas such as the insulation of buildings and windows. The European Silicones Centre, CES, has calculated that the greenhouse-gas savings arising from the use of silicones outweigh the carbon emissions generated during the production and disposal of silicone products by a multiple.
What makes silicones such enablers of climate-change mitigation?
There are a number of reasons. Because of its heat resistance and its insulation properties, silicone rubber is essential for electromobility. Only silicones can deliver the high standards of performance needed for the insulation of high-voltage cables, applications in battery safety, and heat-conducting bonded joints. Our ultra-thin precision silicone film and the NEXIPAL® laminates that we make from it will be used for fuel cells and novel, electrically active actuators and generators in the future. These can also be used to generate electricity. The list of applications could go on and on. Silicone rubbers, then, are highly versatile materials that offer extreme performance and adaptability and have any amount of development potential. They are therefore just what processors and product developers need for developing the innovative and sustainable products and technologies of tomorrow. So, we are not over-promising when we say that, by 2030, our entire product portfolio will be geared toward supporting defined sustainability criteria.