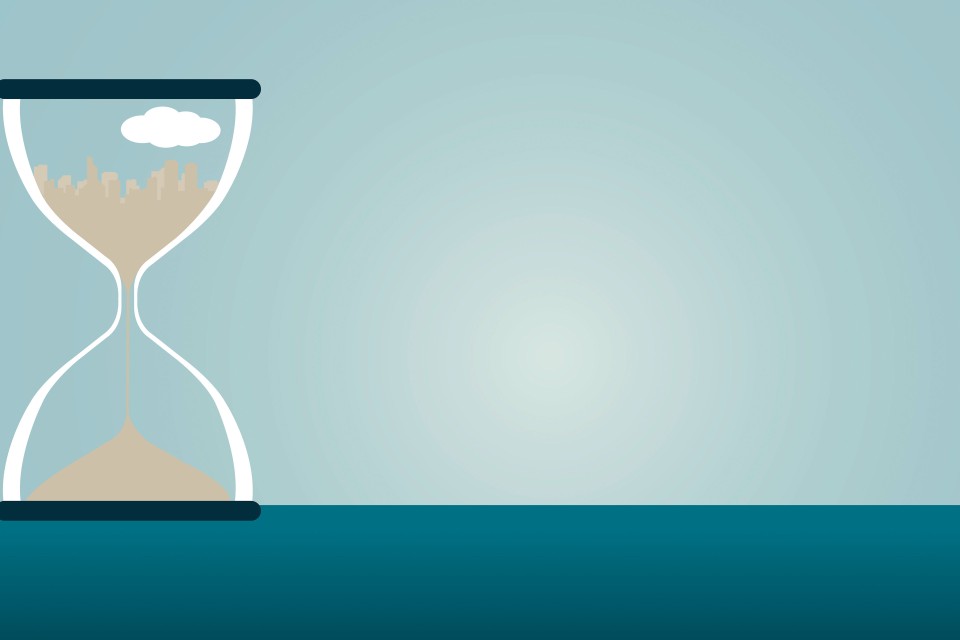
2.63 g/cm3 is the grain density of the silica sand that the WACKER chemists used as a reference sample for their tests.
Built on Sand
Sand is essential for many building materials, but it is also a finite resource. Which is why manufacturers around the world are on the look-out for alternatives. If ground to the right particle size, recycled concrete can replace much of the silica sand used in tile adhesives – without impairing the quality, as tests conducted by WACKER chemists have shown.
21.6
percent of materials consumed in an EU country like Italy are based on recycled raw materials
Despite all the green bins and yellow bags for recycling paper and plastic standing outside houses in Germany – the real recycling champion in the European Union is Italy. Exactly 21.6 percent of the materials consumed in that Mediterranean country come from recycled and reprocessed secondary raw materials, compared with 12.8 percent in the EU and 13.4 in Germany.
To promote the recycling of industrial and household waste even further, the Italian government is planning to introduce various incentives, such as a reduced VAT rate for recyclables. The reduced rate will be compensated for by increasing the levy for disposing of waste in landfills or incinerators. And construction companies bidding for public contracts in Italy are currently required to use 15 percent of recycled materials in their building materials.
“Such political interventions mean that manufacturers of building materials are now increasingly looking for recycled materials to serve as alternatives to the raw materials they use,” explains Carlo Jahr, responsible for the Building & Infrastructure business team for the Eastern Europe and Middle East region at WACKER POLYMERS. “Manufacturers are especially focusing their attention on sand.”

The concrete is crushed and then sorted according to its granularity.
50 Billions Tons per Year
he reason for this lies in the quantities consumed: every year, mankind processes around 50 billion tons of the stuff. Sand is found in cement-based systems, such as concrete, mortars and tile adhesives, as well as in in bricks, glass, in the substructure of roads and in dams for flood protection.
“Sand is the world’s most-heavily-traded solid resource,” says Jahr. “But, it is also a finite resource. It therefore makes sense to recycle building rubble and to use it as an alternative to sand.”
It might seem surprising to learn that not even sand as a raw material is as plentiful as the proverbial “sand on the seashore” – especially given such vast sandy deserts as the Sahara. Yet, Dubai, for example, had to import sand from Australia to build the world’s tallest skyscraper, the Burj Khalifa, because the desert sand on its doorstep was not suitable. Having been eroded over many millions of years, desert sand is usually too fine, too smooth, and too round to reliably provide the necessary cohesion in set concrete.
Serious Consequences
The United Nations Environment Programme (UNEP) too is calling for the extraction and use of sand to be reconsidered because of the possible serious consequences for rivers and coastal and marine ecosystems – including erosion, salination of groundwater, loss of protection from storm surges and of biodiversity.
The construction industry, in particular, is reliant on sand as a raw material because it processes vast amounts of it. It also generates enormous amounts of building rubble. While over 90 percent of this is recycled in Germany according to the Federal Environment Agency, that figure includes low-quality uses – such as filler material in landscaping, road substructures and landfill construction.
“From a circular economy point of view, however, it would be better to recycle concrete sourced from building rubble, for example, into applications that keep the value creation high,” explains Linn Mehnert from the WACKER POLYMERS sustainability team. “One option here would be to use recycled concrete in dry-mix mortars, specifically in tile adhesives.”
More Flexibility
Tile adhesives are a type of dry-mix mortar consisting of at least three components: binders, additives and aggregates. Besides cement, vinyl acetate-ethylene (VAE) copolymers of the kind produced by WACKER POLYMERS serve as the binders. “These VAE copolymers improve the bond between tiles and the substrate and give the tile adhesive greater flexibility,” explains Dr. Klas Sorger, who heads an applications laboratory for construction and infrastructure applications at WACKER POLYMERS.
Silica sand is the most important aggregate in a tile adhesive and typically constitutes 50 to 60 percent by weight of the finished product. “As much as half of this amount of sand can be replaced by fine-grained recycled concrete without any impairment to the properties of the tile adhesives – in fact, quite the opposite is true,” stresses Dr. Sorger, who has studied the subject in detail in his laboratory.
“Up to half of the sand can be replaced with recycled concrete without compromising tile adhesive quality.”
Dr. Klas Sorger, Application Technology, WACKER POLYMERS
Fine-Grained Fractions
The studies were performed on fine-grained fractions of recycled concrete comprising particles up to 1.25 mm in size. These fractions were produced by two different methods. The first involved taking crushed recycled concrete obtained from Ettengruber GmbH and passing it through a screen at the WACKER site in Burghausen. The second is economically more relevant, because it utilizes all the recycled concrete. Prof. Andrea Kustermann’s Laboratory for Building Materials and Construction Chemistry at the Munich University of Applied Sciences ground the recycled concrete supplied by Ettengruber to the requisite particle size.
The crystalline phases of the ground samples were then determined with an X-ray diffractometer. The analysis showed the composition of the material to be calcite/silica/dolomite in a 40/20/30 ratio by weight, along with an amorphous component (10). It follows that the finegrained fraction of the recycled concrete consists of gravel (limestone, dolomite/calcite), sand (silica), carbonated fractions of portlandite and amorphous calcium silicate hydrate phases from set cement. The team from the Burghausen analytical laboratory failed to find any appreciable amounts of cement or gypsum that had not set.
The particle density of the screened samples was then determined in a capillary pycnometer as described in DIN 18124, yielding values of between 2.3 and 2.4 g/cm3. These are lower than the particle density values for a silica sand reference (2.63 g/cm3) and are consistent with a large number of fine pores having diameters between ten nanometers and five micrometers.
Due to the large proportion of fine particles and fine pores in the samples of recycled concrete, tile adhesives based on this aggregate require more mixing water than traditional tile adhesives of the same consistency.
2.63
g/cm3 is the grain density of the silica sand that the WACKER chemists used as a reference sample for their tests.

An Ettengruber long-reach excavator during demolition work. To date, demolition material has mostly been used in low-value applications.
Stronger and more flexible at the same Time
The tile adhesive formulated by Sorger and his team to serve as a reference for these studies fits the C2TE S1 classification defined in DIN EN 12004-1 [5] (C = cementitious adhesive, 2 = highstrength adhesive, T = resists vertical slip, E = open time of at least 30 minutes, S1 = deformable adhesive, where deformation is greater than 2.5 and less than 5 mm). The polymer contained in the adhesive is VINNAPAS® 8620 E, a dispersible polymer powder based on vinyl acetate, ethylene and vinyl chloride that, among other effects, improves the wet strength of the tile adhesive and makes it more flexible.
In the sample formulations, either 25 or 50 percent of the sand in the reference tile adhesive was replaced with recycled concrete, whereby the water needed to be increased to 290 mL and 320 mL, relative to 270 mL for the reference mortar. Virtually no differences were found between the reference and the other samples in terms of sag resistance, viscosity or density – properties that are significant for fresh tile adhesive.
A study comparing wetting capability was carried out as described in DIN EN 1347 [6]: the tile adhesive was applied onto a concrete slab and a tile was laid 10, 20, 30 and 40 minutes later; a force of 50 Newtons was subsequently applied to the tile for a period of 30 seconds. The contact surface between the tile adhesive and the tile was then determined. “This showed that the formulations based on recycled concrete were actually superior to the reference formulations,” Dr. Sorger points out. “The higher the percentage of recycled concrete, the better the wetting capability was.” This is a result of the increased water demand of the mixes containing recycled concrete.
A higher proportion of recycled concrete increased the open time, paralleling the improvement in wetting capability (see graph below). Open time was determined as directed in EN 12004-2 by placing tiles in the adhesive after 5, 20 and 30 minutes and then measuring the tensile adhesive strength. A longer open time makes work much easier for the tiler, as tiles can be laid for longer in the mortar bed.
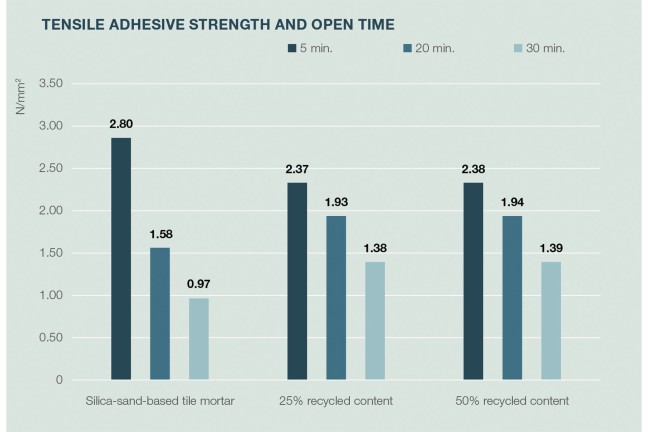
Determining open time by measuring tensile adhesive strength. In formulations based on recycled concrete 2 (center) and 3 (right), tensile adhesive strength was better after 20 and 30 minutes than was the case for the reference. Open times are therefore longer.
“Tile adhesives based on recycled concrete were actually superior in our studies, to conventional formulations.”
Dr. Klas Sorger, WACKER Application Technology

Tiles before installation: The open time describes the period of time during which a tiler can lay the tile in the prepared mortar bed. A higher percentage of recycled concrete in the formulation lengthens the open time, making it easier for the tiler to work.
Beneficial for Hydration
Improved wetting capability and longer open times for formulations based on recycled concrete have no negative impact, either on the initial tensile adhesive strength, or on tensile adhesive strength following storage in water, at elevated temperatures or under freeze-thaw conditions (see graph below). For Dr. Sorger, one possible explanation here is that the finepored particles in the recycled concrete act as something of a reservoir that gradually releases water over time. That is an advantage when it comes to cement hydration. A team at the Technical University of Lisbon studying the use of recycled concrete in mortar production proposed this hypothesis in 2013.
The values for tensile adhesive strength following storage at elevated temperatures are evidence of the considerable flexibility of all of the formulations studied here. This is because storage at higher temperatures generates mechanical stresses due to differences in the coefficients of expansion for the tiles and substrate – the tile adhesive must be able to withstand those stresses. The exceptional flexibility demonstrated here can be traced to the VAE/VC terpolymer in the formulations. Deformation was determined for the formulations according to EN 12004-2, whereby the values for all of the blends containing recycled concrete were the same as those for the reference, within experimental error.
The studies were later repeated using tile adhesives in which the screened, fine-grained fraction was drawn from recycled concrete that the Ettengruber company produced a half year after the originally used batch. Fortunately, the results of the previous study could be reproduced using these tile adhesives, “This suggests that the quality of the two batches of recycled concrete was quite similar,” stresses Dr. Sorger. Recycled concrete can replace silica sand in tile adhesives, thus helping to conserve natural resources – that’s the conclusion reached by WACKER chemists after their extensive research.
“Whether the use of recycled concrete as an aggregate in tile adhesives actually reduces the end product’s carbon footprint and also makes economic sense for dry-mortar manufacturers, however, depends very much on the underlying conditions, such as the manufacturing processes of the recycled concrete, the origin of the electricity needed to crush the building material and the transport routes,” adds Linn Mehnert from WACKER POLYMERS’ Sustainability team. Also, sufficient quantities of recycled concrete of consistent quality need to be available near the dry-mix mortar production sites, for example, she noted.

In the Application Technology laboratory in Burghausen, tile adhesive is applied to a concrete slab and its wettability is then tested at specific time intervals.

Testing of the
- initial tensile adhesive strength
- and the tensile adhesive strengths after water storage,
- hot storage,
- and freeze-thaw cycles.
Results for formulations 2 and 3 based on recycled concrete (center and right, respectively) were not significantly different from those for the reference formulation 1.
Contact
For more information on this topic, please contact:
Mr. Dr. Klas Sorger
Senior Technical Service Manager
WACKER POLYMERS
+49 8677 83-8115
Send message