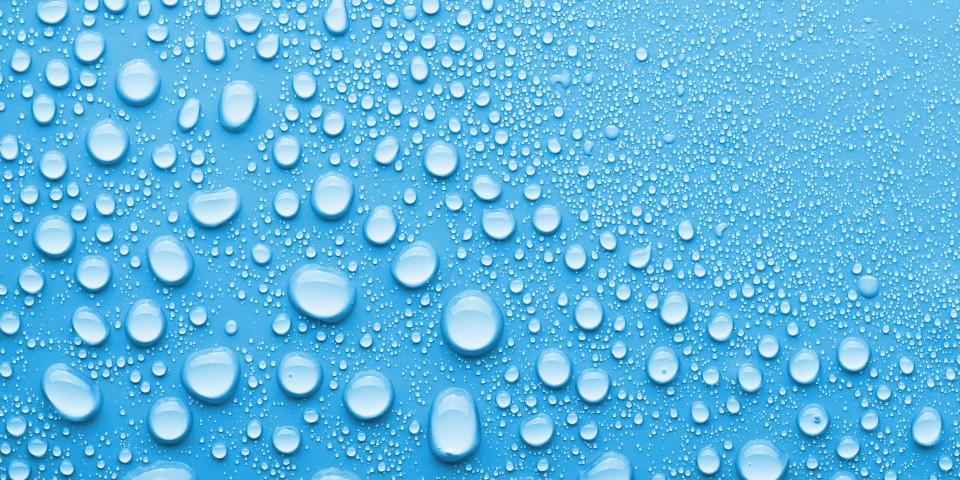
Protection against Water Damage
Mar 17, 2023 Read time: approx. MinutesMinute
Watertight with Dispersions
Waterproofing membranes made with cement have proved to be highly effective at protecting buildings against water damage, thanks to an added dispersion that gives them the flexibility to bridge cracks. In VINNAPAS® 754 ED and 764 ED, WACKER is now launching two new products that retain this ability even at temperatures ranging from minus 5 down to minus 20 degrees Celsius.
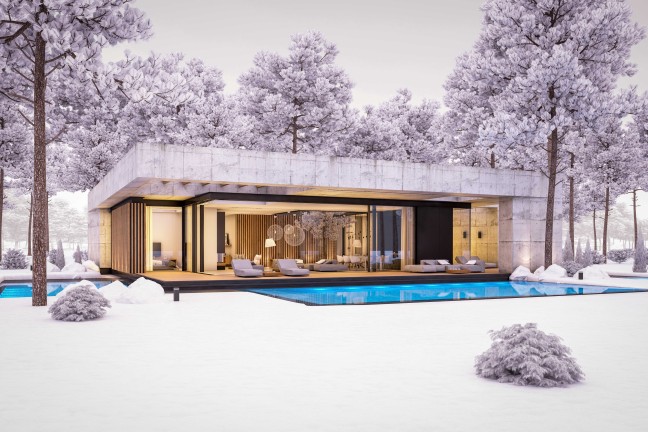
Waterproofing membranes based on cement and polymer dispersions are used to protect buildings from moisture.
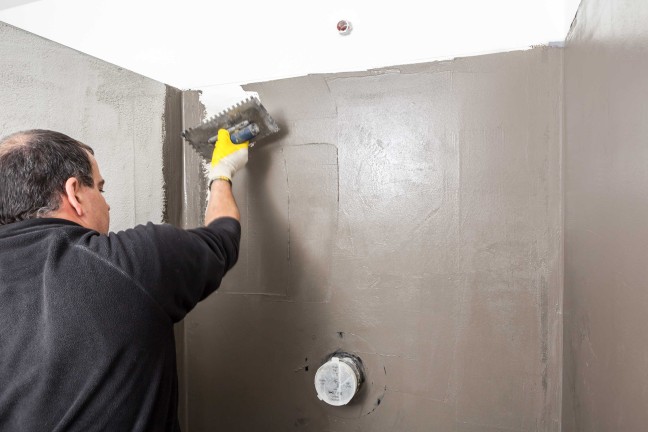
Before tiles are laid in a shower, a craftsman applies a waterproofing membrane.
“Water always finds a way” is an old saying amongst tradesmen. And because this is the case, water tops the list of types of structural damage that are uniquely attributable to a single cause. This is the conclusion reached once again by Bauherren-Schutzbund e. V., a German consumer protection organization for private builders, in its latest study entitled “Development and cost of structural damage.” The average cost of structural damage is around 40,000 euros and can turn many a dream of home ownership into a nightmare.
“Water damage is often particularly egregious because you frequently don’t notice it until it’s too late – such as when the masonry is already soaked through,” says Dr. Harald Zeh from WACKER POLYMERS' Application Technology department. Discoloration then occurs, accompanied perhaps by mold growth and flaking plaster. In the worst case, if the steel inside the concrete begins to rust badly and the structural stability is compromised, the entire building fabric is at risk.
Waterproofing membranes have proved invaluable at protecting against this type of damage: They feature hydrophobic properties that enable them to repel water. These membranes bond to all kinds of building materials, are easy to trowel on, for example, and easy to apply around various shapes and installations.
Flexible layers
Special dispersions have been developed by WACKER POLYMERS for this purpose. When these are combined with cement and fillers, which are only capable of presenting a brittle matrix on their own, the result is a flexible layer that is able to bridge structural cracks – this is essential for providing lasting protection against water.
“We use terpolymers based on vinyl acetate, ethylene and other, hydrophobic and flexible monomers here,” explains Dr. Michael Faatz, Technical Service Manager at WACKER POLYMERS. “They boost the elasticity of the cement and allow the coating to stretch.”
But the ability to stretch is a function of temperature. At low temperatures, the glass transition temperature of the material may be breached and in that event the polymer will lose its elasticity. The membrane is then no longer able to bridge any cracks in the building fabric and starts to tear. Once the temperature climbs above freezing again, water is able to penetrate unhindered into the brickwork.

Building components are reliably protected from water penetration with modern, flexible waterproofing membranes.

Waterproofing membranes are tested for watertightness at the Burghausen Technical Center.
It is therefore essential that the waterproofing membrane contain the right dispersion for the intended application. “With this in mind, we developed two new dispersions that retain their elasticity down to minus 5 and minus 20 degrees Celsius,” says Dr. Zeh. VINNAPAS® 754 ED, for example, meets the Class O1 requirements of EN 14891 for flexibility and product crack-bridging capacity down to minus 5 degrees Celsius.
For its part, VINNAPAS® 764 ED retains these properties even down to minus 20 degrees Celsius, thereby satisfying the Class O2 requirements of the same standard. The temperature at which the material’s flexibility diminishes is even lower again, at around minus 30 degrees Celsius.
Neither product requires any additional solvents, plasticizers or film-forming agents. Therefore, according to an evaluation by the German Institute for Risk Assessment, they may even be used for contact with drinking water and are suitable for two-component waterproofing membranes used to seal swimming pools, basements and bathrooms, as well as water pipes, sewers and tunnels.
Crack-bridging test and tensile adhesion bond test with VINNAPAS® 754 ED
In accordance with EN 14891 for “Liquid applied water impermeable products for use beneath ceramic tiling bonded with adhesives,” VINNAPAS® products for waterproofing membranes are tested for their crack-bridging ability, their tensile adhesive strength, and more.
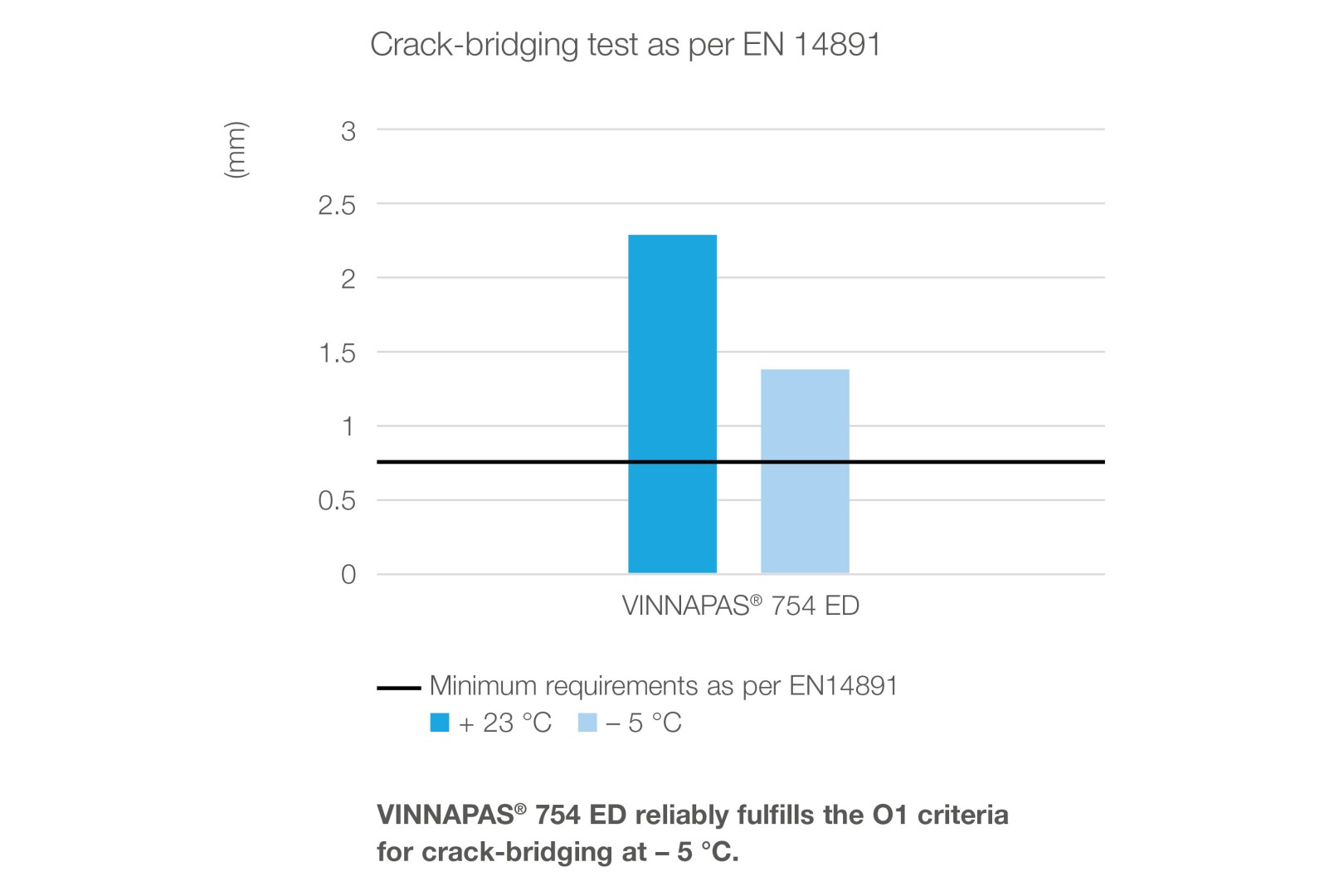
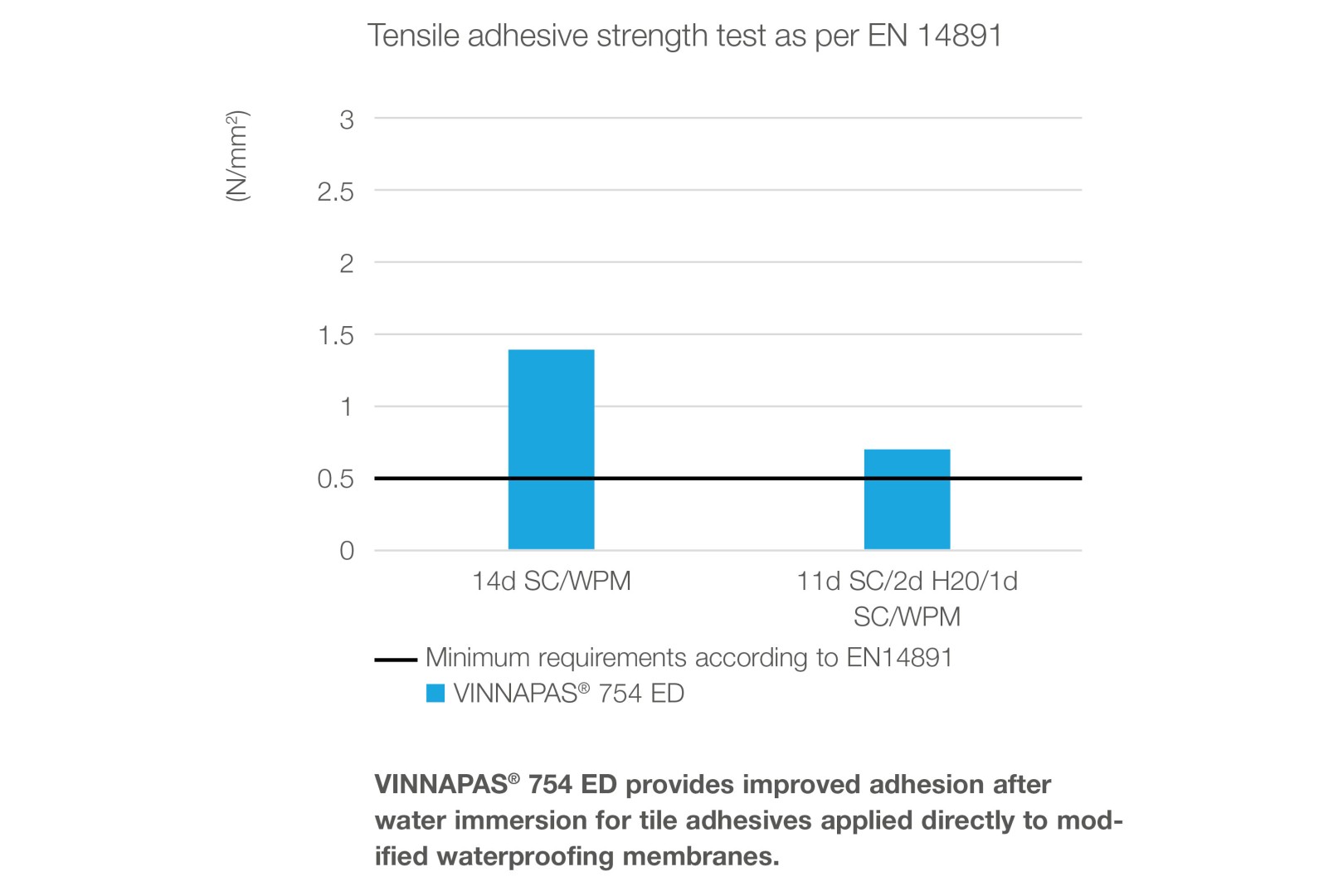
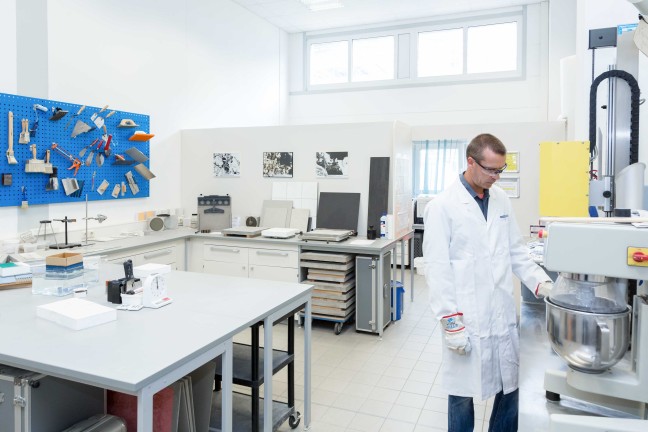
Modification with a polymer dispersion makes the cement flexible. In the construction laboratory (top) in Burghausen, waterproofing systems are produced and their crack bridging ability is subsequently tested in accordance with DIN 14891 (below).
Early customer involvement
“The specific properties conferred on waterproofing membranes by our dispersions depend, of course, primarily on our customers’ end products,” explains Dr. Zeh. Since they determine, for example, the ratio in which the VINNAPAS® products are mixed with the cement, WACKER POLYMERS involves its customers early in the development of new products to ensure that these meet the standards that are crucial for professional building protection.
In principle, low-viscosity waterproofing membranes could be used and can even be easily spread with a stiff-bristled brush. That would be the simplest way to apply them. However, the resulting sealing layer would be very thin. More common is a layer two to four millimeters thick, typically applied with a trowel. The viscosity of the waterproofing membrane plays a pivotal role here. For ease of use, it should be as low as possible. But for thick layers, it needs to be high and permit application in a single coat. That creates greater acceptance among craftsmen and makes the waterproofing system more likely to be successful on the market.
Compliance with building regulations
To ensure that all these considerations are taken into account, WACKER subjects new products in development to very extensive tests. “We want to make sure early on in the development process that we are headed in the right direction with our approach and that our customers’ products meet the pertinent building regulations,” explains Michael Faatz. “We formulate waterproofing membranes, apply them to standardized concrete blocks and then test all the important properties on them.”
“Our polymer boosts the elasticity of the cement and allows the membrane to stretch.”
Dr. Michael Faatz, Technical Service Manager, WACKER POLYMERS

The test, which can be performed under standard climate conditions or at sub-zero temperatures (down to -20 °C), is captured on camera.
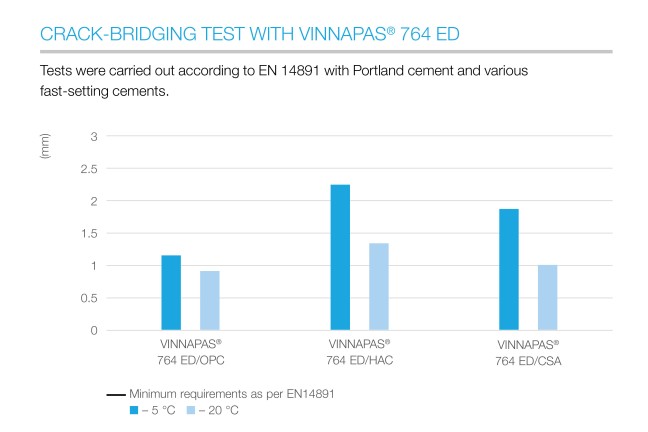
Crack-bridging test with VINNAPAS® 764 ED
Tests were carried out according to EN 14891 with Portland cement and various fast-setting cements.
Consider, for example, the protection of concrete against water pressure. This is tested by conditioning a specimen for four weeks under normal climatic conditions and then exposing it to a 1.5 bar head of water – equivalent to a 15-meter water column. No leaking of any kind is permitted.
The ability to bridge cracks in the structure is also tested on standardized concrete blocks in the laboratory. This is done by breaking the specimens in a specific way and clamping them in tensile testers. A camera then monitors the applied force until the waterproof layer tears.
“We put a lot of effort into these tests so that we can really be sure that we’re developing a marketable product,” explains WACKER chemist Dr. Zeh. “We acquire a great deal of know-how for our customers that we share with them. This means they can be confident that they can create standard-compliant applications using our products.” And, for their part, the property developers know that their buildings can be effectively protected against water damage, a fact that is reflected in their sustainability and value retention over the long term.
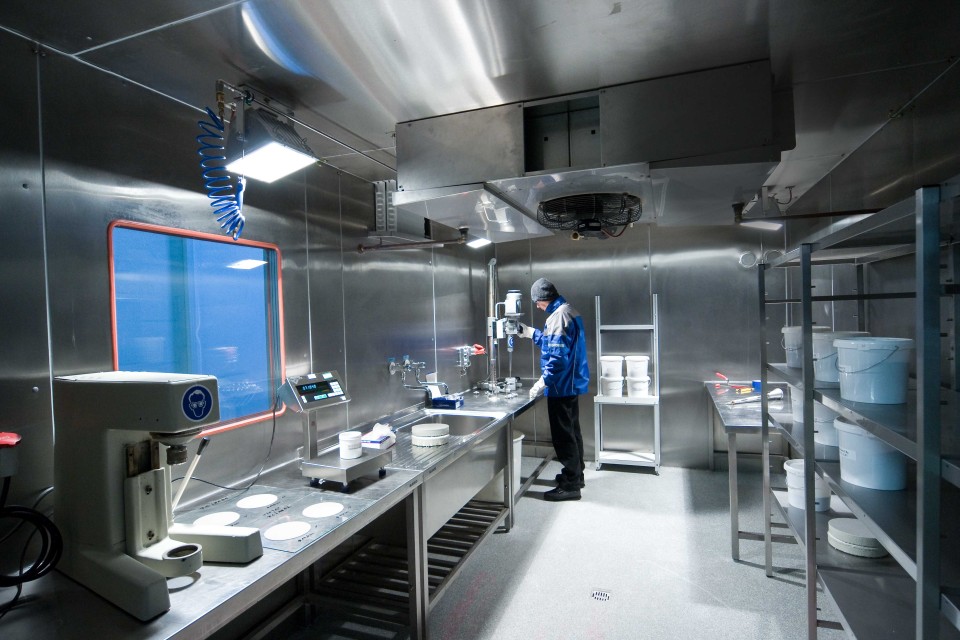
-30 °C
WACKER’s climate chamber in Burghausen tests the properties of waterproofing membranes at extreme low temperatures.
Only at such low temperatures does the material gradually lose flexibility when formulated with VINNAPAS® 764 ED.
Contact
For more information on this topic, please contact:
Mrs. Kerstin Bichler
Senior Marketing Manager
WACKER POLYMERS
+49 8677 83-2728
Send message