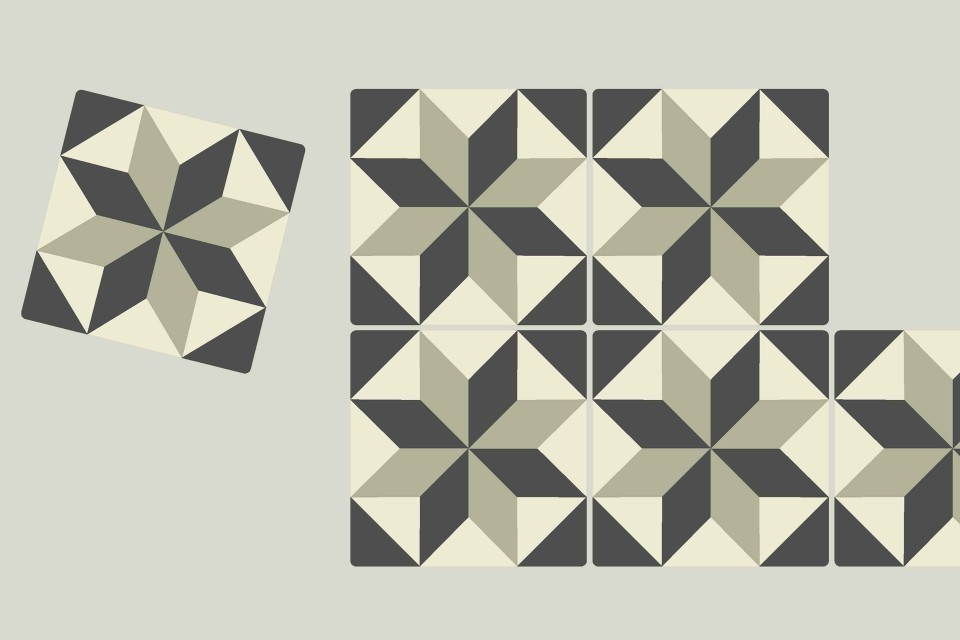
The best way to tile a wall or a floor is to engage the services of an experienced tiler. And to use the right tile adhesive, i.e., one that combines flexibility and adhesion. The same applies to external thermal insulation composite systems. For even greater synergy between man and mortar, WACKER has tweaked the workability of its dispersible polymer powders.
Mar 10, 2023 Read time: approx. MinutesMinute
Mortar for effortless tiling
Some mimic parquet, others look like limestone or imitate marble – tiles are amazingly versatile. In XXL size, as a playful mosaic or extravagantly shaped as hexagons, they give bathrooms, kitchens, hallways and living rooms totally different looks. Since tiles open up almost endless possibilities in terms of design, shape and material, and are also very resilient and easy to clean, they rank among the most popular floor coverings worldwide, accounting for some 50 percent of the total. And that trend keeps rising: in Asia alone, the total area of tiled floors, walls and facades is expected to increase 7 percent by 2025; and four percent respectively in Europe and the Americas.
7%
This is how much tiled floor, wall and facade areas are expected to grow by 2025 in Asia alone, the continent with the world’s largest construction volume.
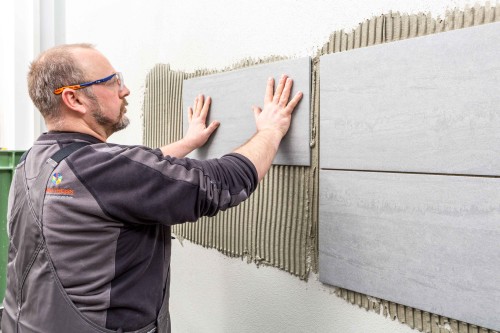
Trendy large-format tiles require especially skilled tilers and a stable mortar that fixes the tiles with pinpoint accuracy.
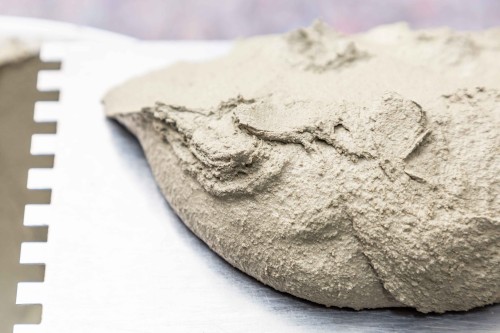
A smooth mortar makes the tiler’s work easier, because it can be troweled on more easily and with less exertion.
“Tiles are becoming more sophisticated, whether we are talking about large tiles, very smooth porcelain tiles or tiles that have a distinctive pattern on the front,” says Dr. Barbara Müller, a marketing manager at WACKER POLYMERS in Burghausen. “This means that tile adhesives, too, have to keep evolving to keep up.”
Across developed industrial nations, tiles are now being laid using the thin-bed technique, which requires polymer-modified high-tech mortars. Added to which, says Müller, “Users increasingly want mortar that has good workability.”
And this is one more reason why WACKER POLYMERS increasingly focuses on this property when developing new VINNAPAS® dispersible polymer powders. The development laboratories in Burghausen had previously concentrated on boosting the performance of the solid mortar, i.e., after it has hardened. This area is one of the strengths of VINNAPAS® dispersible polymer powders based on vinyl acetate and ethylene (VAE): when the dry mortar is mixed with water, they disperse again, and form polymer bridges as the mortar hardens. These bridges are flexible structures that raise the cohesive strength of the adhesive and enhance the bond with both the tile and the substrate, essentially rendering a brittle building material more flexible.
“While these are important characteristics for tilers, they are actually more interested in the mixed mortar,” says Dr. Klas Sorger, who heads an applications laboratory at WACKER POLYMERS in Burghausen. “For tilers, it’s important that the mortar is easy to mix and easy to apply with their tool, the notched trowel.” The mortar should be smooth and preferably have a creamy consistency. In short, tilers should find it easy to work with.
“Tiles are becoming more sophisticated. This means that tile adhesives have to keep evolving to keep up.”
Dr. Barbara Müller, Marketing, WACKER POLYMERS
Viscosity – an objective measuring factor
However, these are subjective assessments on the part of tilers and not exact variables that can be measured with great accuracy. Translating them into technical parameters and modifying the polymers so as to improve the workability of the mixed mortar proved tricky, as Dr. Sorger recalls: “We focused on the viscosity at our Technical Center in Burghausen, because a low viscosity almost always correlates with low resistance. We therefore functionalized our polymers to reduce the mortar’s viscosity.”
At the same time, however, WACKER’s developers had to keep the existing profile of their dispersible polymer powders in mind, because they did not want to compromise the established positive properties. Ultimately, polymeric binders play a key role in tile adhesives by improving the bond between the tile and substrate, and increasing the flexibility of the adhesive. The latter point, especially, is important in the case of very thin or particularly large tiles that are fashionable nowadays – for example, to accommodate potential stresses arising between the tile and the substrate more readily. In addition, XXL tiles are heavier and therefore harder to affix to walls. Here, too, the adhesive has to meet particularly stringent requirements. “It must possess high sagging resistance. Only then can the tiles be properly fixed in position on the adhesive bed,” explains Barbara Müller from WACKER Marketing. Combining all these properties whilst making the tilers’ work easier was a challenging task, but WACKER’s experts have come up with a solution.
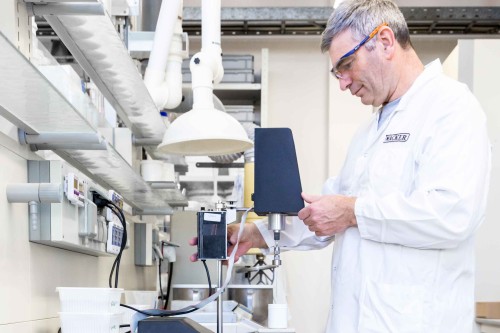
Viscosity test in the application technology laboratory in Burghausen. WACKER functionalizes its polymers to reduce the mortar’s viscosity.
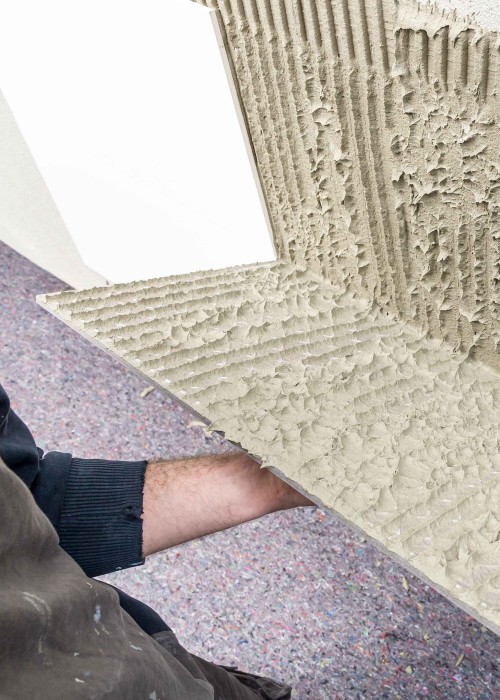
Portfolio expanded by three products
The Group is now adding three new products to its VINNAPAS® portfolio: VINNAPAS® 4419 E is suitable for a wide range of tile adhesives. VINNAPAS® 8819 E is used to produce high-quality mortars for XXL tiles, for example. And, VINNAPAS® 4449 E is a product offered by WACKER specifically for external thermal insulation composite systems.
What all three dispersible polymer powders have in common is that they enhance the workability and consistency of fresh mortar. “This has been confirmed by the many test users we invited to our Technical Center at Burghausen while we were building test walls,” stresses WACKER chemist Klas Sorger, for whom feedback from the field is invaluable. “The tilers found the mortar to be more pliable and visibly less viscous during application. They didn’t need to use as much force when mixing or troweling the mortar and they needed less pressure to place the tiles in the mortar bed – and that was precisely our goal.” Using less force is not only more convenient for tilers, but it is also easier on the joints, such as elbows, which are typically prone to injury in this trade.
The tile adhesive specialists in Burghausen have also succeeded in ensuring that, despite the reduced viscosity, the polymer-modified mortars feature not only improved sagging resistance, but also high wetting capability. This is evident when the tiles are lifted up: the back side is completely wetted with the polymer-modified mortar – proving that a permanent bond to the substrate is ensured. “This property comes to bear primarily in the case of large or very thin porcelain stoneware tiles,” explains Müller. “Here tile adhesives which can do a little more are needed – such as our new VINNAPAS® 8819 E.”
Less stress during installation
Another element import to users is open time. This is the period of time within which the tiles should be laid in the adhesive before it begins to set. It should be at least 30 minutes. Anything longer than that is welcomed by tilers for they can then cover a larger area with adhesive and lay the various tiles in place without the mortar already starting to harden.
"This will appeal particularly to users in warmer regions or in summer, because higher temperatures cause the mortar to set faster," says Dr. Sorger. "High temperatures mean that craftsmen have to work faster or can only work on small areas at a time and have to adopt a more piecemeal approach. With our new binders, we're helping them gain more time."
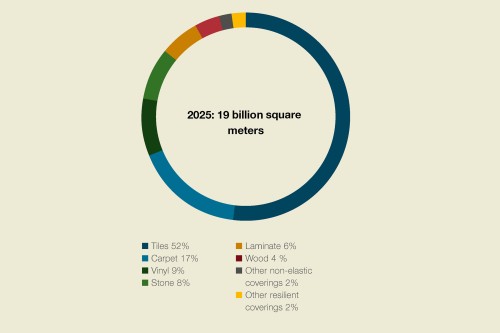
MARKET FOR FLOORING WORLDWIDE 2025
Worldwide, tiles already account for some 50 percent of all flooring – and this figure is set to rise further until 2025. Lagging behind in second place is carpeting.
Source: Markets & Markets, Global Flooring Market, June 2020

While the range of talents tile adhesives have to offer is extensive, mortars for external thermal insulation composite systems, or ETICS for short, need to have even more attributes, adds Müller from the Group’s marketing department: “VINNAPAS® 4449 E is our response to the issue of workability here. But this dispersible polymer powder additionally renders the mortar highly flexible and impact resistant. Outdoors, which is where ETICS are used, this is crucial for providing good resistance to weathering stresses.” At the same time, the VAE polymer acts as a stable yet flexible bond between the individual layers of the protective facade insulation.
And sustainability is another area where the VAE-based binders score points. Although dispersible polymer powders are just one component in formulations for tile adhesives and ETICS mortars, more and more positive properties are accruing to them. “To an extent, depending on the formulation, manufacturers may even be able to dispense altogether with certain additives they previously had to use for the sake of greater workability,” Dr. Sorger points out. “In particular, where these are not very readily available locally or regionally, this proves to be not merely an economic advantage, but also a logistical one.”
Less than 30
minutes is the minimum open time the industry requires before the tile adhesive begins to set.
In general, VINNAPAS® dispersible polymer powders contain no components or plasticizers of concern and are free of volatile organic components (VOCs) – they do not emit any potentially harmful substances. “With our three new products, we have managed to take what was already an outstanding portfolio and made it just that little bit better. Thanks to the improved workability, we have become even more visible to the actual users, i.e., the tilers and craftsmen, whereas before we tended to work behind the scenes,” say the two WACKER experts, summing up their successful VINNAPAS® new additions.
“Tilers and craftsmen found the mortar to be more pliable and visibly less viscous during application.”
Dr. Klas Sorger, Application Engineering, WACKER POLYMERS
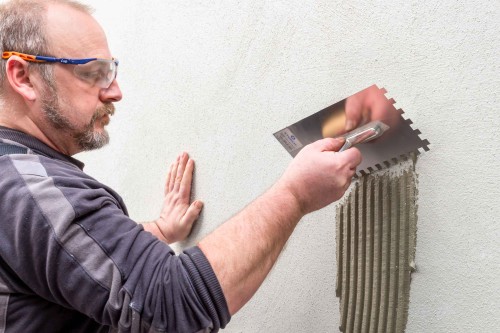
The notched trowel is used to apply the tile mortar to the wall.
Contact
For more information on the topic, please contact
Mrs. Dr. Barbara Müller
Senior Marketing Manager
WACKER POLYMERS
Send message