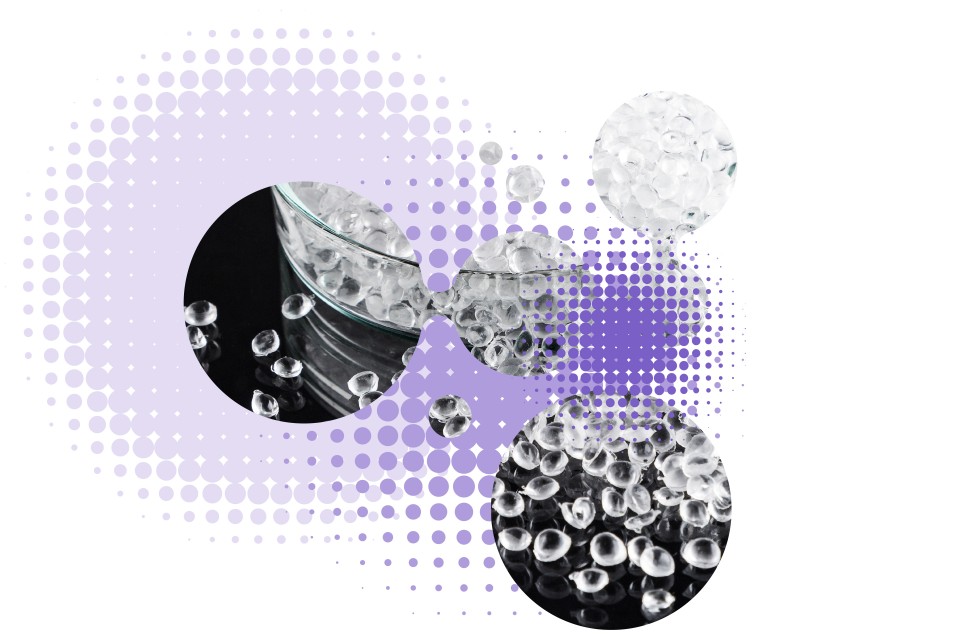
Kunststofftechnik
10.10.2022 Lesezeit: ca. MinutenMinute
Siliconadditive – Ein bis drei Prozent genügen
Silicone-Gum-Masterbatches verbessern schon in geringen Mengen die Verteilung der Füllstoffe in Kunststoff-Formmassen, ihre Fließfähigkeit und Abriebsbeständigkeit. Mit GENIOPLAST® PE50S08 hat WACKER jetzt ein Additiv speziell für Polyethylen entwickelt, das Compoundeuren neue Formulierungsfreiräume schafft.
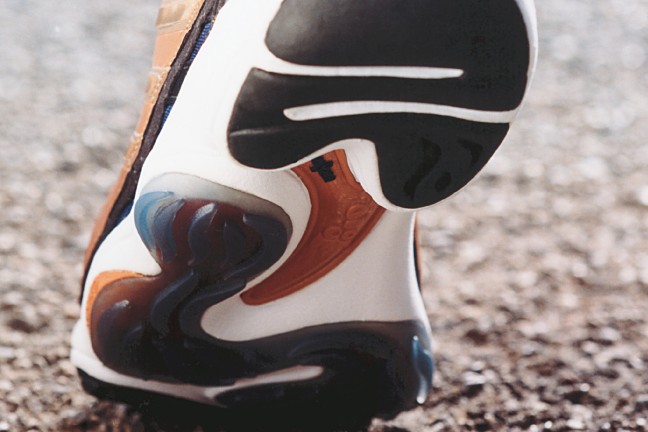
Die verbesserten Oberflächeneigenschaften von Polyethylentypen, die mit GENIOPLAST® PE50S08 compoundiert werden, kommen ganz besonders Anwendungen zugute, bei denen das Material mechanisch stark belastet wird – wie bei diesen Sohlen von Laufschuhen.
Der Markt für Polyethylen, dem weltweit am häufigsten verwendeten thermoplastischen Kunststoff, ist hart umkämpft, der Wettbewerbsdruck nimmt zu und das Recycling von Polyethylen-Abfällen stellt die Branche vor zusätzliche Herausforderungen. „In diesem wirtschaftlich und technologisch anspruchsvollen Umfeld können sich Compoundeure und Kunststoffverarbeiter nur durch überlegende Qualität, Spezialisierung und Kosteneinsparungen behaupten“, erklärt Martin Schmid, der bei WACKER SILICONES ein Business Team im Bereich Performance Solutions leitet. Einen Weg dazu, so Schmid, erschlössen Additive, mit denen sich die Produkteigenschaften des Kunststoffs verbessern lassen oder die in der Lage seien, die Herstellungs- und Verarbeitungsprozesse der Formmassen effizienter zu gestalten – und dies sowohl bei Neuware als auch bei Recyclaten.
Seit Langem setzt die Kunststoffindustrie Siliconadditive in Polyethylen und anderen Thermoplasten ein. Die zugesetzten Silicone wirken einerseits als Prozesshilfsmittel, indem sie Reibungseffekte reduzieren und die Fließfähigkeit der Polymerschmelze verbessern, andererseits beeinflussen sie aber auch die Qualität der Kunststoffartikel, indem sie die Oberflächenreibung verringern.
„Vorteilhaft gegenüber organischen Additiven ist die sehr niedrige Oberflächenenergie der Silicone, die für eine hohe Aktivität an Phasengrenzflächen verantwortlich ist – und damit für ihre thermische Beständigkeit und ihre Tieftemperaturflexibilität“, erklärt Oliver Fuhrmann, der bei WACKER in Burghausen ein anwendungstechnisches Labor für Siliconadditive leitet.
Herkömmliche Siliconadditive haben dennoch einige Nachteile: Niedrigviskose Siliconöle etwa tendieren dazu, aus dem Kunststoff zu migrieren. Das ausgetretene Silicon erschwert nachfolgende Bearbeitungsschritte. Hochviskose Silicone – nichtreaktive ultrahochmolekulare lineare Polydimethylsiloxane, kurz als Silicone Gums bezeichnet – migrieren zwar praktisch nicht aus dem Kunststoff, lassen sich jedoch schlecht in Thermoplaste einarbeiten. „Dieses Problem lösen unsere Silicone-Gum-Masterbatches“, betont Oliver Fuhrmann. „In diesen Formulierungen wird ein thermoplastisches Polymer als Träger für das Silicone Gum eingesetzt, das mit dem zu modifizierenden Thermoplast kompatibel ist.“ Als festes Granulat ließen sich diese Masterbatches dann gut verarbeiten.
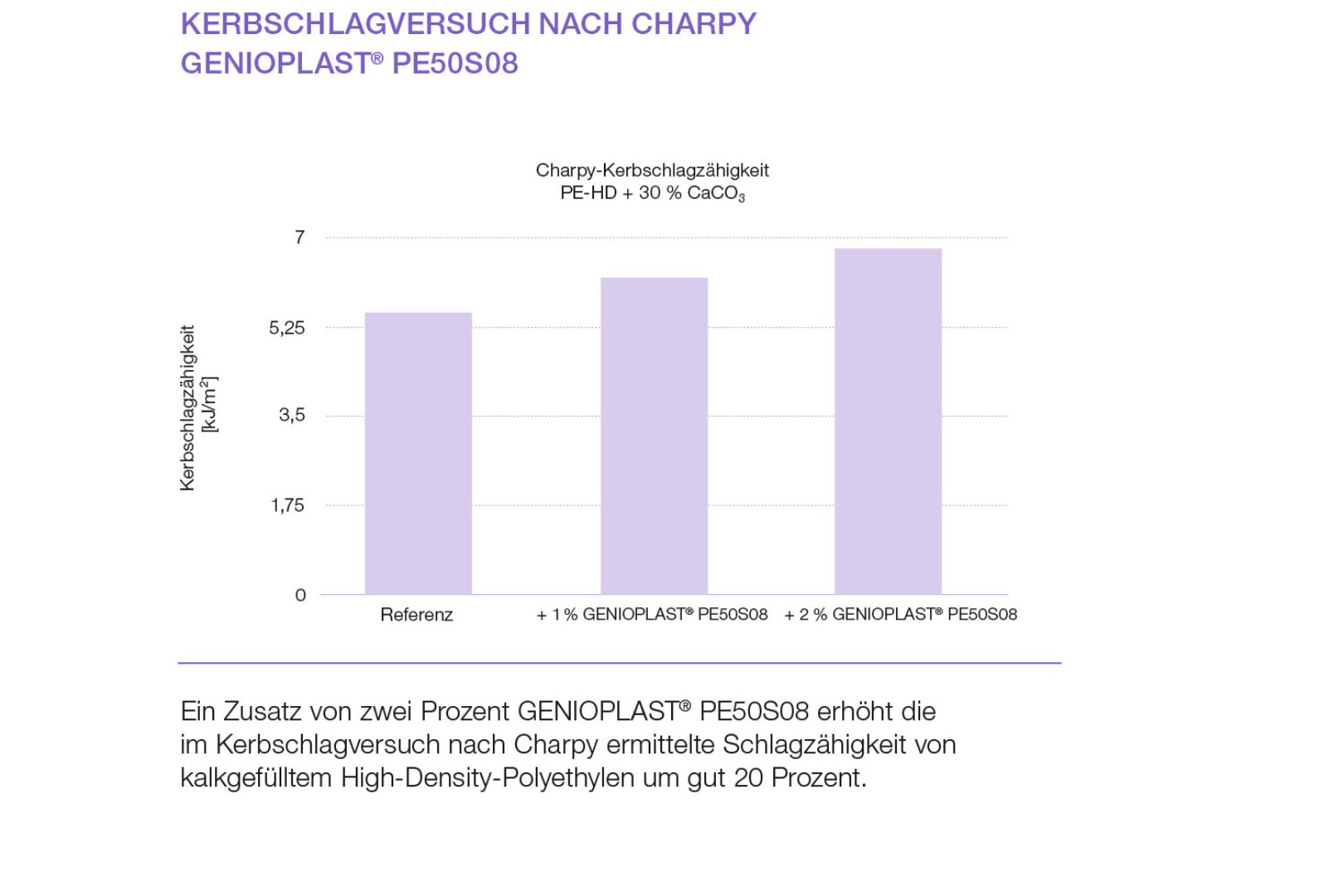
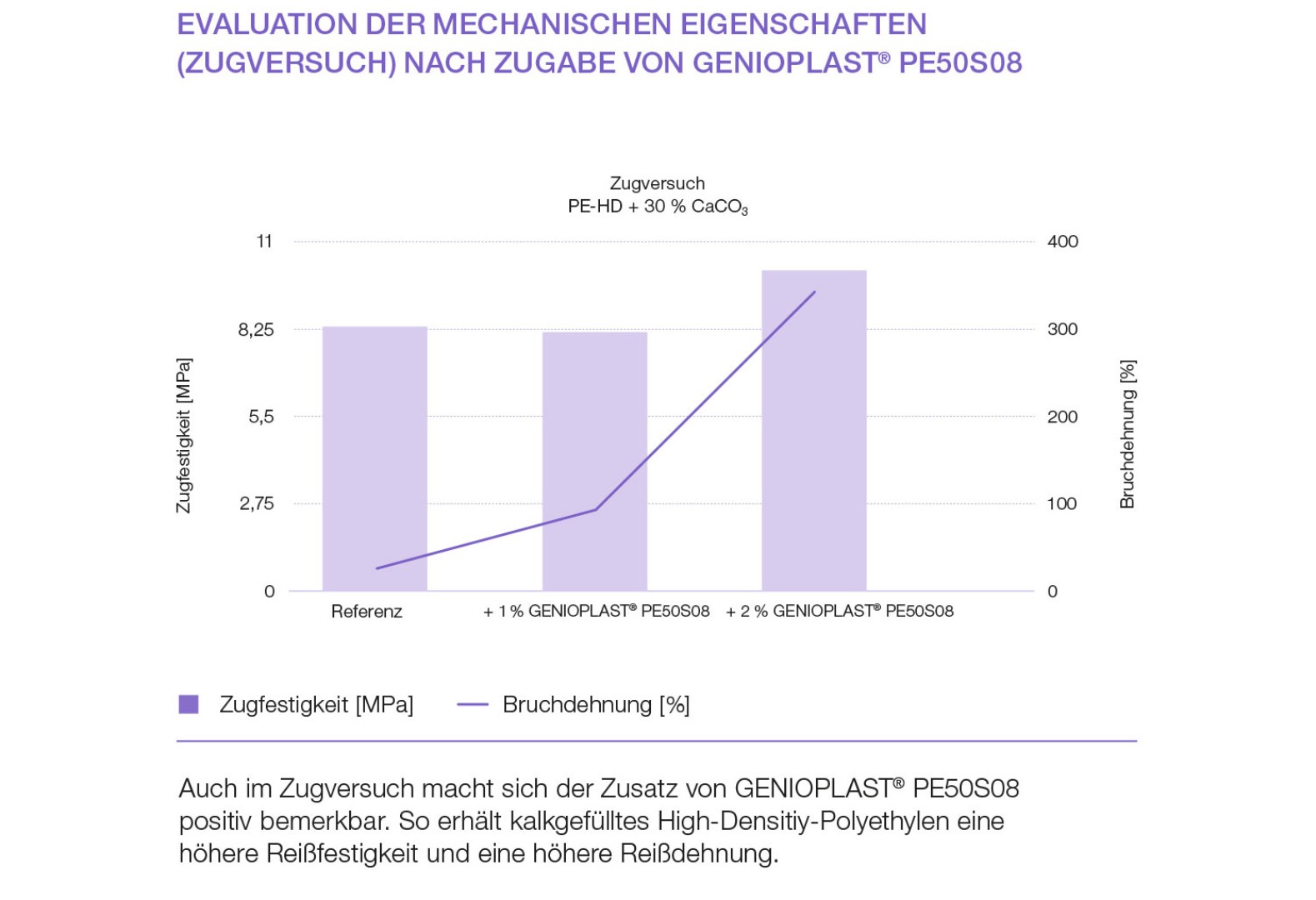

Siliconadditive – hier gebrauchsfertige Pellets – erleichtern die Herstellung verarbeitungsfähiger Polyethylen- Formmassen und verbessern die Oberflächeneigenschaften der daraus hergestellten Kunststoffartikel.
Silicone Gum mit sehr hohem Molekulargewicht
Mit GENIOPLAST® PE50S08 hat WACKER jetzt einen Silicone-Gum-Masterbatch speziell für die Compoundierung von Polyethylen entwickelt. GENIOPLAST® PE50S08 enthält als Wirkstoff einen Silicone Gum mit außerordentlich hohem Molekulargewicht, der in ein Low-density-Polyethylen dispergiert ist. Der Wirkstoffgehalt beträgt 50 Prozent.
Wegen des verwendeten Trägermaterials ist der Einsatz dieses Additivs auf Polyethylen und solche Polymere beschränkt, die mit Polyethylen kompatibel sind. GENIOPLAST® PE50S08 kann auch für Kunststoffartikel verwendet werden, die mit Lebensmitteln in Kontakt kommen.
Das neue Additiv liegt in Form von Pellets vor, die der Compoundeur problemlos mit gebräuchlichen Geräten wie Doppelschneckenextrudern oder Ko-Knetern in das Polyethylen-Basispolymer einarbeiten kann, auch zusammen mit mineralischen Füllstoffen. Hierbei verbessert der Siliconwirkstoff die Verteilung der Füllstoffe und erhöht die Fließfähigkeit der Polymerschmelze. Dies gibt dem Compoundeur neue Formulierungsfreiräume.
Durch seine reibungsvermindernden Eigenschaften erleichtert der Siliconwirkstoff die Herstellung der Compounds, also der verarbeitungsfähigen granulierten Formmassen. So wird bei Zugabe des Siliconadditivs beim Compoundieren weniger Energie benötigt. Zugleich kann der Compoundeur einen höheren Durchsatz erreichen. Somit spart GENIOPLAST® PE50S08 Kosten beim Compoundieren ein. Wegen der hohen Wirksamkeit des Silicone Gums genügen Einsatzmengen zwischen einem und drei Prozent.
„GENIOPLAST® PE50S08 trägt zur nachhaltigen Nutzung von thermoplastischen Kunststoffen wie Polyethylen bei.“
Martin Schmid, Performance Solutions, WACKER SILICONES
GENIOPLAST® sorgt für einen gleichmäßigen Prozess
Auch bei der Aufarbeitung von recyceltem Polyethylen bringt der Einsatz des Siliconadditivs Vorteile: Bei den Polyethylen-Abfällen handelt es sich in der Regel um Gemische mehrerer Polyethylentypen, die sich im Schmelzverhalten und in den Fließeigenschaften erheblich unterscheiden. Werden solche Gemische recompoundiert, also erneut zu verarbeitungsfähigen Formmassen aufbereitet und somit stofflich wiederverwertet, kommt es im Compoundier-Extruder zu starken Drehmoment- und Temperaturschwankungen, der Extruder läuft ungleichmäßig. Hier sorgt GENIOPLAST® PE50S08 für einen gleichmäßigen Prozess.
Bei der formgebenden Verarbeitung der Compounds machen sich die prozessverbessernden Eigenschaften des Additivs ebenfalls bemerkbar – unabhängig davon, ob der Kunststoffverarbeiter Formteile im Spritzgießverfahren herstellt oder ob er die Formmassen im Extruder zu Profilen, Schläuchen, Kabel- Ummantelungen oder Folien verarbeitet.
Die prozessverbessernden Eigenschaften stellen nur eine Seite des Wirkungsspektrums von GENIOPLAST® PE50S08 dar. Das Siliconadditiv verbessert zusätzlich die Oberflächeneigenschaften der aus den Formmassen hergestellten Kunststoffartikel, ohne dass der Verarbeiter unerwünschte Nebenwirkungen in Kauf nehmen muss. Die Grundeigenschaften des Polyethylen-Basispolymers wie Zugfestigkeit, Härte oder Wärmeformbeständigkeit bleiben erhalten; die Schlagzähigkeit wird erhöht.
Als typisches Siliconadditiv verleiht GENIOPLAST® PE50S08 der Oberfläche von Polyethylen-Neuware und -Recyclaten eine höhere Glätte. Die glattere Oberfläche wiederum erhöht die Kratz- und Abriebfestigkeit des Kunststoffs.
So lässt sich der Gleitreibungskoeffizient – abhängig vom eingesetzten Polyethylen-Basispolymer – bei Zugabe von zwei Prozent des Siliconadditivs auf Werte unter 0,25 senken, auch bei Recyclaten. Solch niedrige Gleitreibungskoeffizienten werden von Folienherstellern und der Verpackungsbranche gewünscht, damit sich Folien leichter abrollen lassen. Ohne Gegenmaßnahmen haften die auf einer Rolle übereinanderliegenden Folienlagen stark aneinander, was das Abziehen der Folie erschwert. Gelingt es, den Gleitreibungskoeffizienten deutlich zu verringern, können die Folienkonfektionierung und das Verpacken von Waren spürbar schneller werden. Mit dem neuen Additiv sparen die Folienhersteller und -anwender Zeit und Kosten.
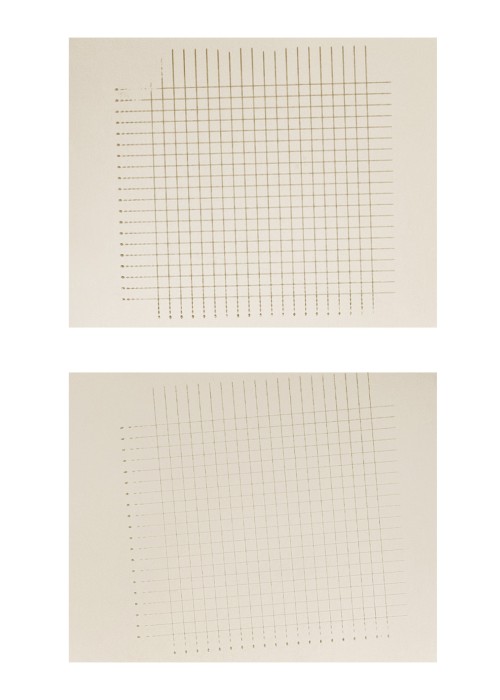
Eine unmodifizierte Polyethylen-Platte weist nach dem Kratztest deutliche Kratzspuren auf (Bild ganz oben). Durch Zugabe von GENIOPLAST® PE50S08 verbessert sich die Kratzfestigkeit erheblich (Bild unten).
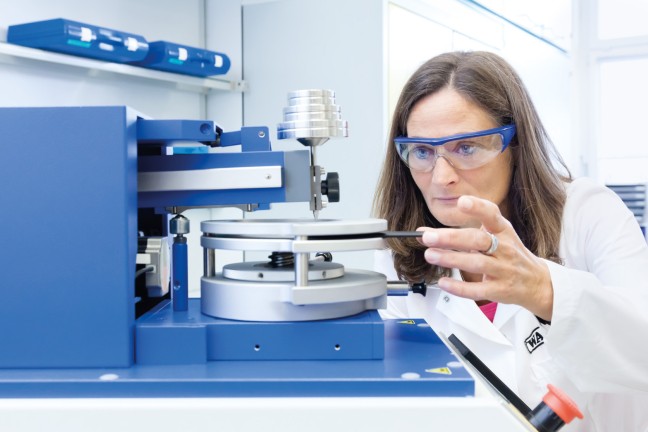
Beim Erichsen-Kratztest fährt eine Nadel mit einer genau eingestellten Kraft und Geschwindigkeit über die zu prüfende Kunststoffoberfläche und erzeugt ein Kreuzgittermuster aus Kratzspuren. Die Kratzspuren werden anschließend näher untersucht und die Farbunterschiede mithilfe eines Farbmessgerätes bestimmt.
Labortests belegen bessere Kratz- und Abriebbeständigkeit
Einen Beleg für die verbesserte Kratz- und Abriebfestigkeit liefern Laborprüfungen, die in den anwendungstechnischen Labors von WACKER durchgeführt wurden. Im Mittelpunkt standen dabei der Erichsen-Kratztest und der Crockmeter-Test.
Beim Erichsen-Kratztest werden mit einem Ritzhärteprüfgerät definierte Kratzspuren in der Kunststoffoberfläche erzeugt und diese anschließend näher untersucht. Im Crockmeter-Test nach DIN EN ISO 105-X12 reibt ein Prüfkopf, der mit einem Baumwolltuch überzogen ist, über die Kunststoffoberfläche und hinterlässt mehr oder weniger stark sichtbare Reibspuren, die visuell beurteilt werden.
Die konfokalmikroskopische Untersuchung der mit dem Ritzhärteprüfgerät erzeugten Kratzspuren zeigt, dass die Kratzer im mit GENIOPLAST® PE50S08 modifizierten Polyethylen nicht so tief sind wie im nicht modifizierten Polyethylen und dass die Kratzer zugleich deutlich weniger stark aufgeraut sind. Folglich streuen die Kratzer einfallendes Licht geringer und erscheinen dadurch weniger hell. Eine Messung der Helligkeit bestätigt diesen Effekt: Helligkeitsunterschiede zwischen den verkratzten und den unbeschädigten Stellen sind im modifizierten Kunststoff geringer, die Kratzer folglich optisch unauffälliger.
Mit GENIOPLAST® PE50S08 lässt sich auch der Abrieb verringern, wie der Crockmeter- Test belegt: Nicht nur Kratzer, sondern auch Reibspuren sind für einen Betrachter weniger stark sichtbar als beim nicht modifizierten Polyethylen.
Zu den Polymeren, die mit Polyethylen kompatibel sind und daher ebenfalls mit GENIOPLAST® PE50S08 modifiziert werden können, zählen die Ethylen-Vinylacetat-Copolymere. Diese kurz als EVA bezeichneten Kunststoffe werden häufig zur Herstellung von Schuhsohlen und Kabelmänteln verwendet. Hier hängt die Wirkung des Siliconadditivs erheblich davon ab, wie hoch der Vinylacetat-Anteil im EVA ist. Indem der Compoundeur ein geeignetes EVA-Basispolymer auswählt und die Additiv-Einsatzmenge optimiert, kann er den Gleitreibungskoeffizienten und den Materialabrieb anwendungsgerecht ausbalancieren. So können Schuhsohlen infolge des verminderten Abriebs länger halten, ohne dass die Rutschgefahr zu groß wird.
Seine prozess- und oberflächenverbessernden Wirkungen machen GENIOPLAST® PE50S08 zu einem effizienten Hilfsmittel bei der Compoundierung von Polyethylen. Zu seinen wichtigsten Anwendungsmöglichkeiten zählen die Herstellung von Blasfolien, das Recycling von Polyethylen-Abfällen und die Extrusion von hochgefüllten Polyethylen-Formmassen – etwa die Extrusion von Ummantelungen für Niederspannungskabel. Diese Anwendung wird möglich, wenn die Kabel keinen besonderen Anforderungen an den Flammschutz genügen müssen.
Bei der Aufarbeitung von Polyethylen-Abfällen kann der Compoundeur durch Einsatz des Siliconadditivs erreichen, dass das Recyclat in seinen Eigenschaften nahe an Neuware heranreicht. „Somit trägt GENIOPLAST® PE50S08 zur nachhaltigen Nutzung eines thermoplastischen Kunststoffs wie Polyethylen bei und unterstützt die Branche beim Aufbau einer Kreislaufwirtschaft“, hebt WACKER-Manager Martin Schmid hervor.
Schon diese wenigen Beispiele zeigen: GENIOPLAST® PE50S08 stößt das Tor zu einer kostengünstigen Compoundierung und Weiterverarbeitung von Polyethylen weit auf. „Mit unserem neuen Silicone-Gum-Masterbatch können Compoundeure und Verarbeiter Einsparpotenziale erschließen und eine höhere Produktqualität erzielen“, ist Martin Schmid überzeugt. „Das sind echte Vorteile im Wettbewerb.“
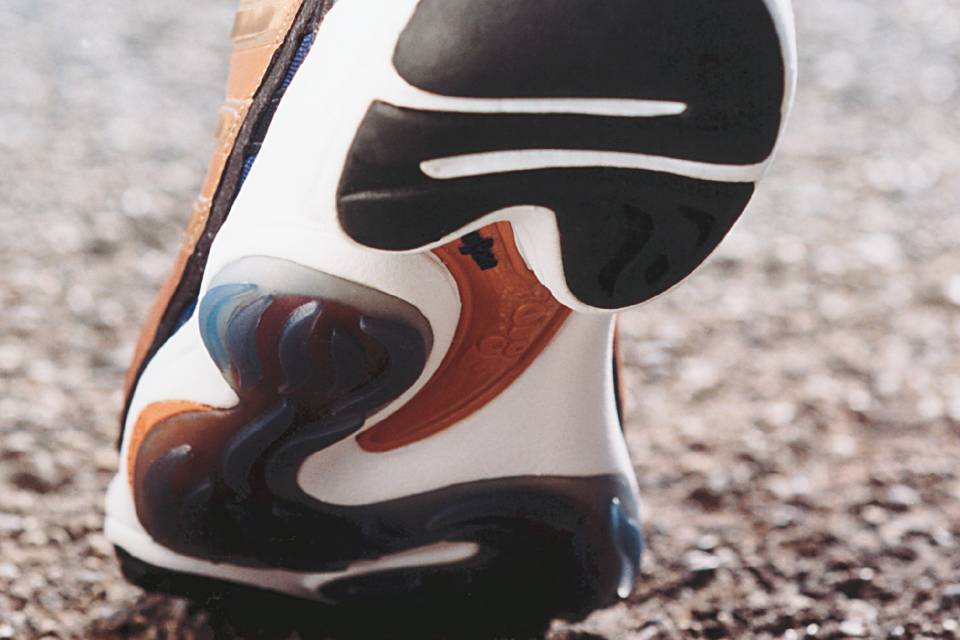
Weitere Additive für die Compoundierung thermoplastischer Kunststoffe
Mit GENIOPLAST® PE50S08 ergänzt WACKER sein Portfolio siliconbasierter Compoundier-Additive um ein Produkt, das speziell für den Einsatz in Polyethylen-Formmassen konzipiert wurde. Für die Compoundierung von thermoplastisch zu verarbeitenden Kunststoffen umfasst das Portfolio folgende weitere Produkte: GENIOPLAST® Pellet S eignet sich universell für die Compoundierung sämtlicher Thermoplaste. Als Wirkkomponente enthält das Additiv ein unvernetztes ultrahochmolekulares Siliconpolymer, das auf eine hochdisperse Kieselsäure aufgezogen wurde. Haupteinsatzgebiet sind flammfest ausgerüstete Kabelummantelungen.
GENIOPLAST® PP50S12, ein Siliconadditiv-Masterbatch, verbessert die Kratzfestigkeit von Polypropylen-Artikeln. Die wichtigsten Anwendungen sind Verpackungsfolien, Gartenmöbel und Bauteile im Automobil-Innenraum. GENIOPLAST® Pellet 345 ist ein siliconbasiertes Additiv für thermoplastische Polyurethane. Es verleiht Smartphone-Hüllen, Wearable-Armbändern und anderen Artikeln aus diesen Kunststoffen eine angenehme Haptik und verringert ihre Verschmutzungsneigung.
Kontakt
Mehr Informationen zum Thema erhalten Sie von
Herr Oliver Fuhrmann
Leiter Technisches Marketing
WACKER SILICONES
+49 8677 83-5877
Nachricht senden