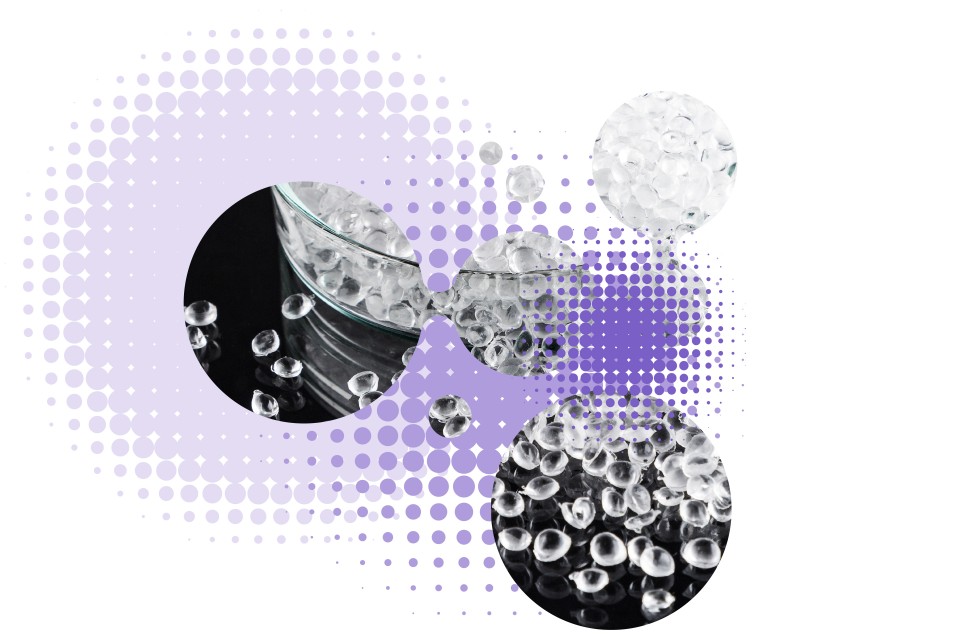
Plastics Technology
Oct 10, 2022 Read time: approx. MinutesMinute
Silicone Additives – One to Three Percent Suffice
Even small amounts of silicone gum masterbatches can improve the distribution of filler in plastic molding compounds as well as their flowability and abrasion resistance. WACKER has developed GENIOPLAST® PE50S08, an additive specifically designed for polyethylene, giving compounders a greater range of formulation opportunities.
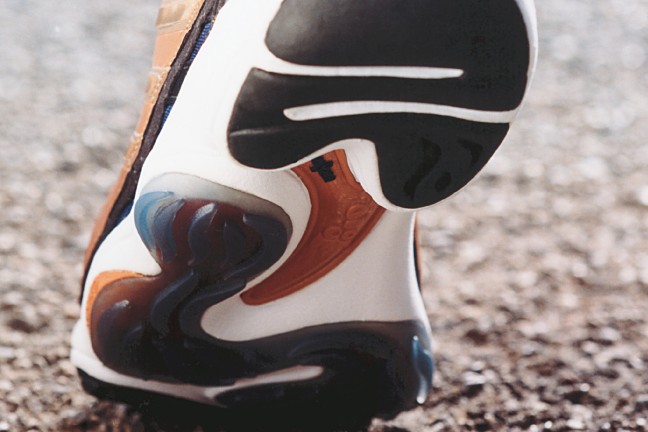
The improved surface properties of polyethylene compounded with GENIOPLAST® PE50S08 are ideal for applications where the material is subjected to strong mechanical loads, such as is the case with running shoe soles.
The market for polyethylene, the most used thermoplastic globally, is highly competitive, with the industry under increasing pressure and facing additional challenges regarding the recycling of polyethylene waste. “Compounders and plastics processors can only stand out in this economically and technically demanding environment by offering superior quality, specialization and cost-savings,” explained Martin Schmid, who manages a business team in WACKER SILICONES’ Performance Solutions business unit. One way to do this, according to Schmid, involves using additives with which the product properties of the plastic can be improved or which can improve the efficiency of manufacturing and processing – both for virgin material and recyclates.
The plastics industry has long been using silicone additives in polyethylenes and other thermoplastics. The added silicones act as processing aids by reducing friction effects and improving the flowability of the polymer melt. They also influence the quality of the plastic article by reducing surface friction.
“One advantage compared to organic additives is the very low surface energy of the silicones, which is responsible for high activity at the phase interfaces – and therefore for the thermal resistance and low-temperature flexibility,” explained Oliver Fuhrmann, who manages an applications laboratory for silicone additives at WACKER in Burghausen.
Standard silicone additives do have some disadvantages: low-viscosity silicone fluids have a tendency to migrate out of the plastic. The exuded silicone hinders downstream processing steps. Highly viscous silicones – non-reactive ultra-high-molecular linear polydimethylsiloxanes, known as silicone gums – practically never migrate out of the plastic, but are difficult to incorporate in thermoplastics. “Our silicone gum masterbatches resolve this problem,” stated Fuhrmann. “A thermoplastic polymer, compatible with the thermoplastic being modified, is used as a carrier for the silicone gum in these formulations.” The masterbatches, in the form of solid pellets, can then be easily processed.
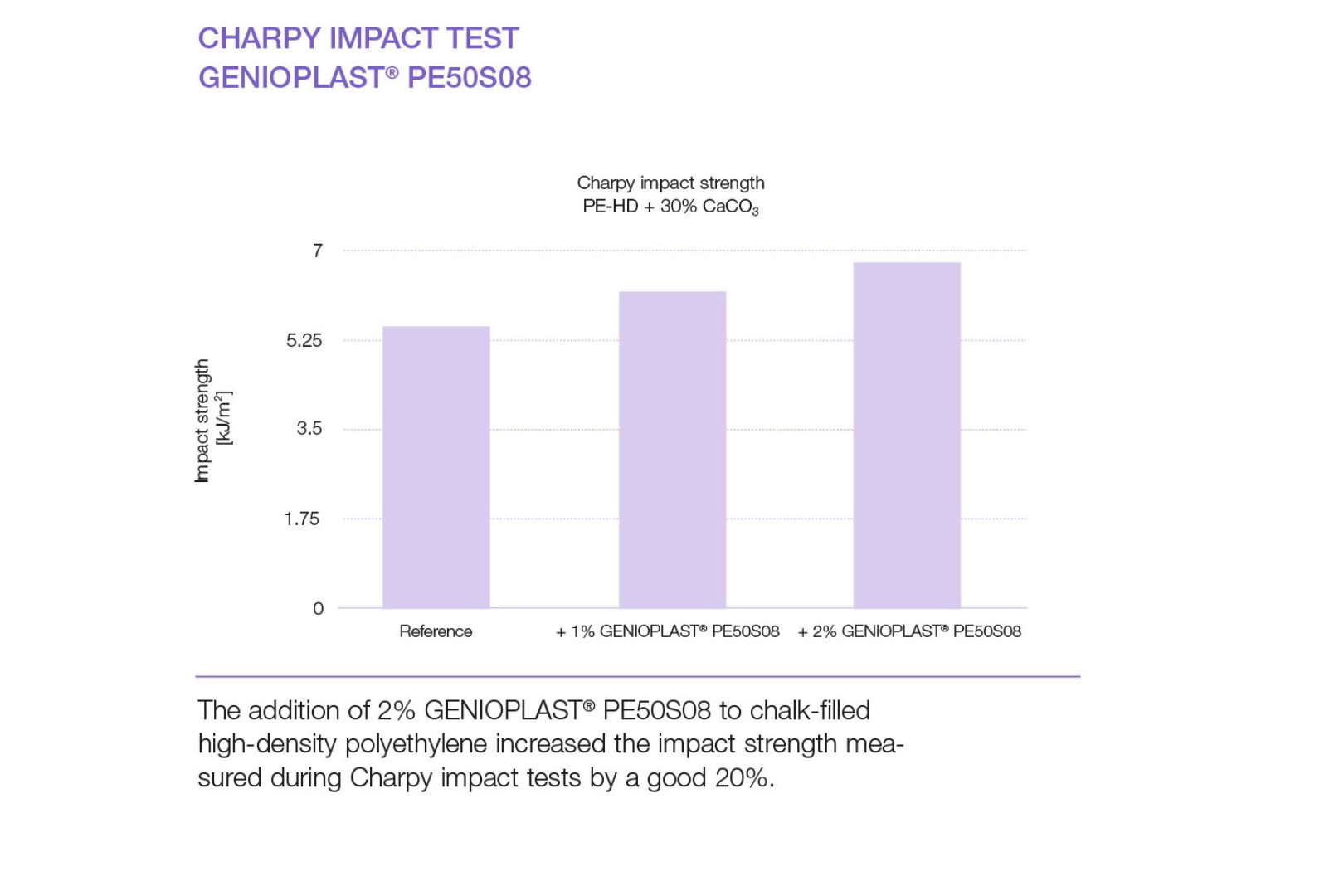
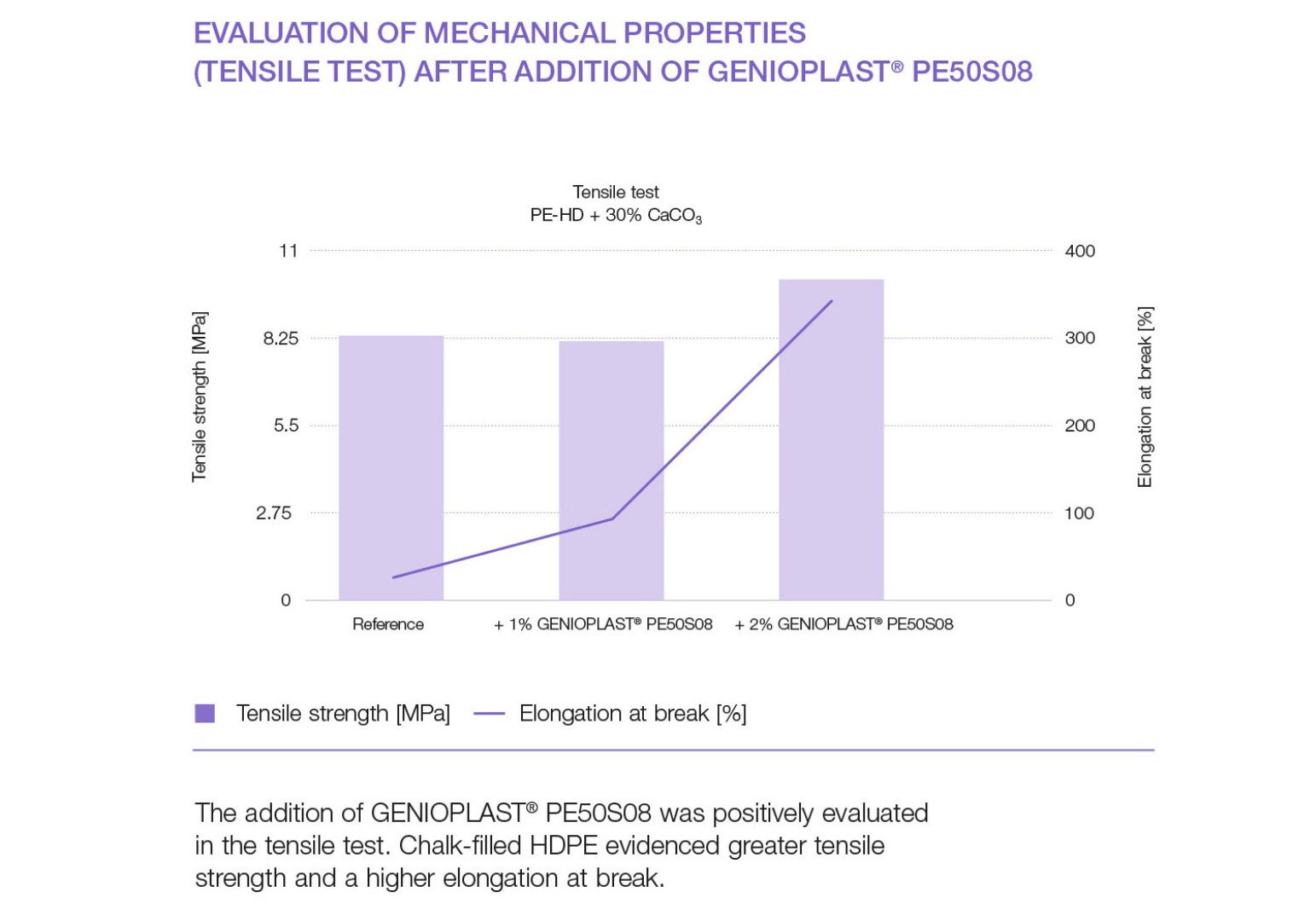

Silicone additives – here as ready-to-use pellets – facilitate the production of workable polyethylene molding compounds and improve the surface properties of the resulting plastic articles.
Silicone Gum with Very High Molecular Weight
WACKER has produced GENIOPLAST® PE50S08, a silicone gum masterbatch specially developed for compounding polyethylenes. The active ingredient in GENIOPLAST® PE50S08 is a silicone gum with an extremely high molecular weight, dispersed in a low-density polyethylene. Because the active ingredient content is 50%,
Due to the carrier matrix used, this additive can only be used in polyethylenes and other polymers compatible with polyethylene. GENIOPLAST® PE50S08 can also be used for plastic articles that come into contact with foodstuffs.
The new additive is available in the form of pellets which the compounder can easily incorporate, together with mineral fillers, into the polyethylene base polymer using standard equipment such as twin-screw extruders or co-kneaders. The silicone active ingredient improves the dispersion of the fillers and increases the flowability of the polymer melt. This gives compounders greater formulation freedom.
The friction-reducing properties mean that this active silicone ingredient facilitates the production of the compound, i.e. the ready-to-use pelletized molding compound. Less energy is therefore required for compounding when this silicone additive is added. The compounder can also achieve a higher throughput. GENIOPLAST® PE50S08 therefore saves costs during compounding. Because of the high efficacy of the silicone gum, the addition of just 1 to 3 percent is sufficient.
“GENIOPLAST® PE50S08 contributes to the sustainable use of thermoplastics such as polyethylene.”
Martin Schmid, Performance Solutions, WACKER SILICONES
GENIOPLAST® Guarantees a Homogeneous Process
The use of this silicone additive is also advantageous in the reprocessing of recycled polyethylene: such polyethylene waste is usually a mixture of several polyethylene grades which differ significantly in their melt behavior and flow properties. If such mixtures are re-compounded, i.e. reprocessed to become ready-to-use molding compounds, considerable torque and temperature fluctuations occur in the compounding extruder, causing it to run unevenly. This is where GENIOPLAST® PE50S08 ensures the process is more homogeneous.
The process-improving properties of the additive are also clear when we look at the compound-molding process – irrespective of whether the plastics processor is injection-molding parts or passing the molding compound through an extruder to produce profiles, hoses, cable sheaths or films.
These process-improving properties are just one aspect of the versatility demonstrated by GENIOPLAST® PE50S08. The silicone additive also improves the surface properties of the resulting plastic articles without the processor seeing any unwanted side effects. The main properties of the polyethylene base polymer, such as tensile strength, hardness and thermostability remain unchanged, while impact strength is increased.
Like a typical silicone additive, GENIOPLAST® PE50S08 increases the smoothness of products based on virgin and recycled polyethylene. The smoother surface in turn increases the scratch and abrasion resistance of the plastic.
Adding just 2% of this silicone additive reduces the coefficient of dynamic friction – regardless of which polyethylene base polymer is used – to values below 0.25, even for recyclates. Such low coefficients of dynamic friction are desired by film manufacturers and the packaging industry because the film can be more easily unrolled. Without such countermeasures, adjacent film layers on a roll would stick together more strongly, making it more difficult to unroll the film. Significantly reducing the coefficient of dynamic friction would tangibly speed up film packing and product packaging. Film manufacturers and users will save time and money with this new additive.
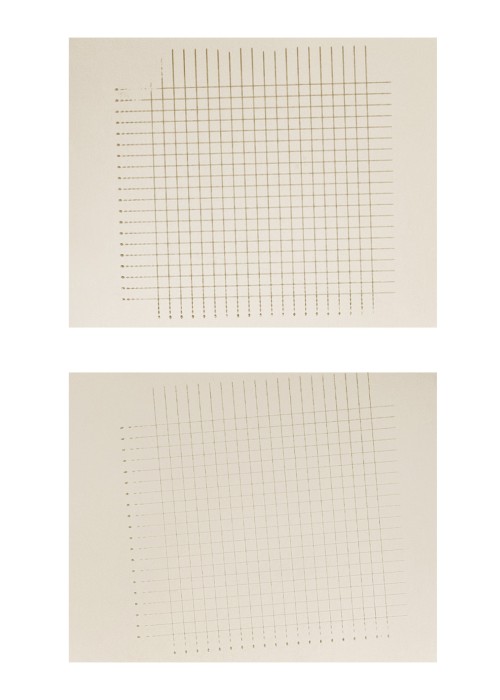
An unmodified polyethylene panel evidences significant scratches after the scratch test (see top image). Scratch resistance was significantly improved through the addition of GENIOPLAST® PE50S08 (bottom image).
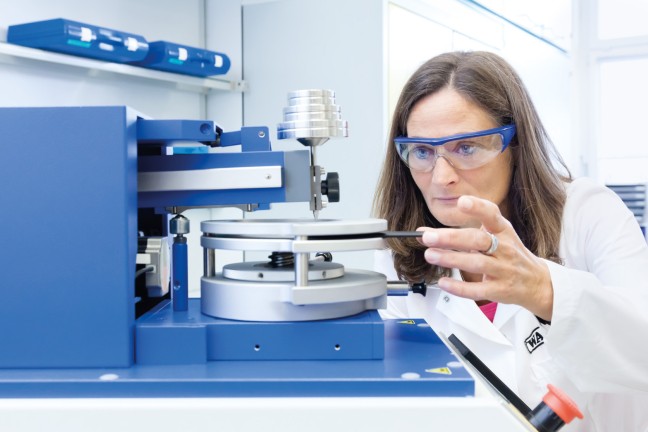
In the Erichsen scratch test, a needle moves at a specific force and speed across the plastic being tested, creating a grid pattern of scratches. The scratches are then examined closely and the color differences determined with a colorimeter.
Laboratory Tests Prove Better Scratch and Abrasion Resistance
Evidence of improved scratch and abrasion resistance was shown by tests carried out in WACKER applications laboratories. The focus here was on the Erichsen scratch test and the crockmeter test.
In the Erichsen scratch test, a scratch hardness tester produces defined scratches in the plastic surface, which are then examined in detail. In the crockmeter test, as per EN ISO 105-X12, a test head covered with a cotton cloth is rubbed over the plastic surface, leaving behind more or less visible friction marks which are then evaluated visually.
A confocal microscope examination showed that the scratches made by the scratch hardness tester in the GENIOPLAST® PE50S08-modified polyethylene were not as deep as those seen in unmodified polyethylene and also that these scratches were significantly less rough. Such scratches therefore scatter incoming light to a lesser extent, so they appear less bright. Measuring the brightness confirms this effect: brightness differences between the scratched and unscratched areas are smaller in the modified plastic and so the scratches are less visible.
GENIOPLAST® PE50S08 also reduces abrasion as proven by the crockmeter test: like the scratches, friction marks are much less visible to the observer compared to unmodified polyethylene.
Ethylene-vinyl acetate copolymers are some of the polymers that are compatible with polyethylene and which can therefore also be modified using GENIOPLAST® PE50S08. This plastic, also known as EVA, is frequently used to produce shoe soles and cable sheathing. The effect of the silicone additive here is greatly dependent on how high the vinyl acetate percentage is in the EVA. The compounder can balance the coefficient of dynamic friction and material abrasion and tailor it to the application by selecting a suitable EVA base polymer and optimal additive percentage. This means that shoe soles will last longer due to reduced abrasion without increasing the risk of slipping.
Thanks to its process- and surface-enhancing effects, GENIOPLAST® PE50S08 is an efficient aid in the compounding of polyethylenes. Some of the main application options include the production of blown film, recycling of polyethylene waste and the extrusion of highly filled polyethylene molding compounds – such as the extrusion of sheaths for low-voltage cables. This latter application is possible if the cable does not have to meet any specific flame-retardant requirements.
When reprocessing polyethylene waste, the compounder can use the silicone additive to produce recyclates with properties almost identical to those of virgin material. WACKER manager Martin Schmid emphasized, “GENIOPLAST® PE50S08 therefore contributes to the sustainable use of a thermoplastic such as polyethylene, and supports industry in setting up a circular economy.”
Just these few examples have shown that GENIOPLAST® PE50S08 has flung open the door to cost-effective compounding and further processing of polyethylenes. Martin Schmid is convinced: “Compounders and processors will gain saving potentials and achieve better product quality with our new silicone gum masterbatches. These are real competitive advantages.”
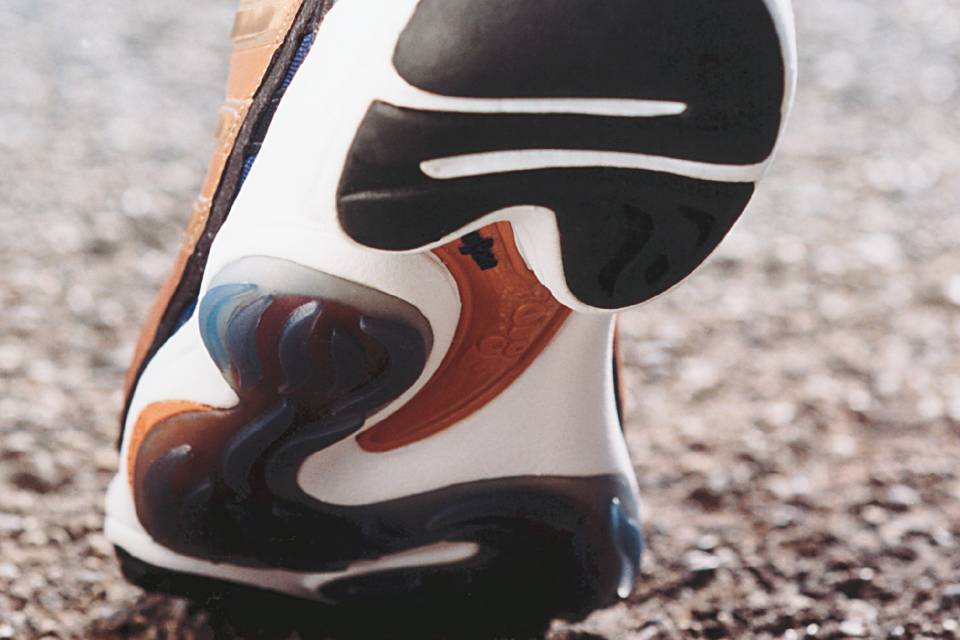
Further Additives for the Compounding of Thermoplastics
WACKER has expanded its portfolio of silicone-based compounding additives with a product – GENIOPLAST® PE50S08 – that has been specially developed for use in polyethylene molding compounds. This portfolio also includes the following products for the compounding of thermoplastic materials: GENIOPLAST® Pellet S is universally suitable for the compounding of all thermoplastics. The active ingredient in this additive is a non-crosslinked ultra-high-molecular silicone polymer mounted on pyrogenic silica. The main application area is for flame-resistant cable sheathing.
GENIOPLAST® PP50S12, a silicone additive masterbatch, improves the scratch resistance of polypropylene articles. The main applications are packaging film, garden furniture and components for vehicle interiors. GENIOPLAST® Pellet 345 is a silicone-based additive for thermoplastic polyurethanes. It bestows a pleasant feel on smartphone covers, wearable wristbands and other articles made with these plastics, and increases their dirt resistance.
Contact
For more information on this topic, please contact:
Mr. Oliver Fuhrmann
Leiter Technisches Marketing
WACKER SILICONES
+49 8677 83-5877
Send message