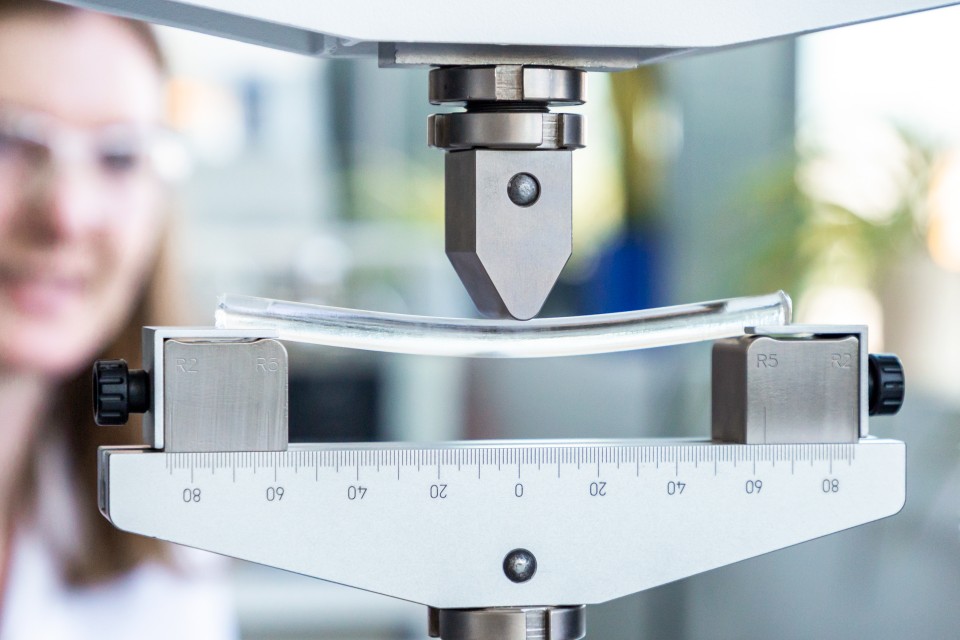
Silicone resins
Ready for production: SILRES® H60 permits rapid and automated impregnation.
Oct 17, 2022 Read time: approx. MinutesMinute
Reliable Thanks to Silicone Resins
Stator windings of electric motors are often impregnated with resin to increase the motor’s high temperature resistance and ensure a long service life. Now, WACKER has launched SILRES® H60, which – by curing extremely rapidly – is suitable for mass automotive production, among other applications.
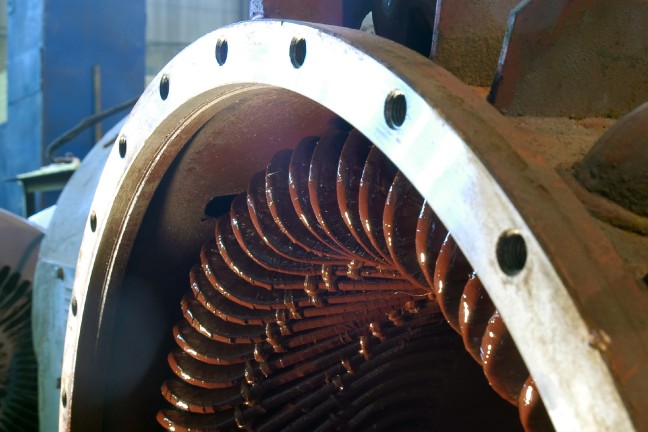
Preformed coils for electric motors of railway vehicles: such large stators are impregnated with SILRES® H62 C by vacuum-pressure impregnation.
The market for electric cars has been picking up speed for about two years. The industry report of the German Center of Automotive Management states that 13 percent of all the new cars registered in Germany in 2021 already featured an electric drive. China, the biggest market for battery-powered cars by far, shows similar market shares.
If confidence in electric cars is to keep growing, they must be just as reliable, robust and long-lasting as their combustion-driven counterparts. The conditions for this are promising, since an electric motor comprises only 250 parts – compared with the 2500 components of a combustion engine, Electric cars are therefore considered low-maintenance.
But these components are of course subject to strict requirements – for example on the wire-wound stators that are often used in electric motors. Impregnation of the windings, which consist of lacquer-insulated round copper wires, is the last step in stator manufacturing. For impregnation, a resin is used that cures to form an electrically insulating thermoset. The impregnation resin, which is liquid during application, penetrates into the gaps between the individual windings and into the interstices of the winding. Once the resin has cured, the windings are coated with solid resin.
“It is well known that silicone-based winding impregnations provide the electric motor with exceptionally high thermal resistance and a long lifetime,” explained Dr. Klaus Angermaier, head of WACKER SILICONES’ Industrial Solutions business team for the European and Latin American markets. Impregnation with a solvent-free phenyl silicone resin is considered particularly effective. Such impregnation resins were only available as one-component products until now, since they were time consuming and laborious to process.
A solution is provided by the new phenyl silicone resin SILRES® H60, which has been in WACKER’s portfolio since early 2021. “This two-component product is characterized by a high curing rate,” explained Dr. Christian Ochs, head of the applications laboratory at WACKER, who was responsible for developing this silicone resin. “SILRES® H60 was specially developed for trickle impregnation. It allows fast, automated impregnation processes to be set up, which can be easily integrated into a mass production line for electric motors,” adds Dr. Ochs.
Podcast
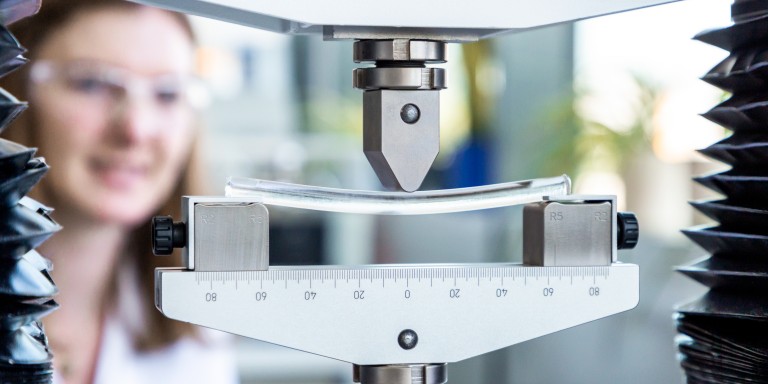
Silicone-based impregnation provides an electric motor with extremely high temperature resistance and a long lifetime.
“Silicone-based impregnation provides an electric motor with extremely high temperature resistance and a long lifetime.”
Dr. Klaus Angermaier, head of the WACKER SILICONES Industrial Solutions Business Team
Impregnation improves the properties of the stator in various ways:
1. It optimizes the electrical insulation.
2. It mechanically reinforces the entire winding as the resin bonds the individual windings and wire layers together. Fixed in this way, the windings can no longer move with respect to one another, thus eliminating vibrations and abrasion. This prevents damage to the primary insulation of the copper wire windings. The primary insulation generally consists of a very thin lacquer coat.
3. The impregnation promotes heat dissipation from the copper winding to the stator laminations, thereby improving thermal management and increasing the heat resistance of the stator – an important effect, since overheating is one of main causes of motor failure.
4. The resin protects the winding against moisture, salt spray and other external media.
Manufacturers of electric motors can adjust the properties of the impregnation to their needs by choosing a suitable resin. “With many electric motors, it is quite sufficient to impregnate the windings with an organic resin, such as an unsaturated polyester or epoxy resin,” said WACKER chemist Christian Ochs. However, for motors expected to face considerable stress from heat or media, optimum protection can be achieved with a phenyl silicone resin.
Cured phenyl silicone resins are thermally and chemically resistant. They age more slowly than organic resins under the effects of temperature and weathering. Their high durability is especially salient in the impregnation of windings particularly of motors that are subject to strong electrical currents during operation and are compact in size without active cooling. As a result, silicone resin impregnation imparts high operational reliability to the motors even under overload conditions.
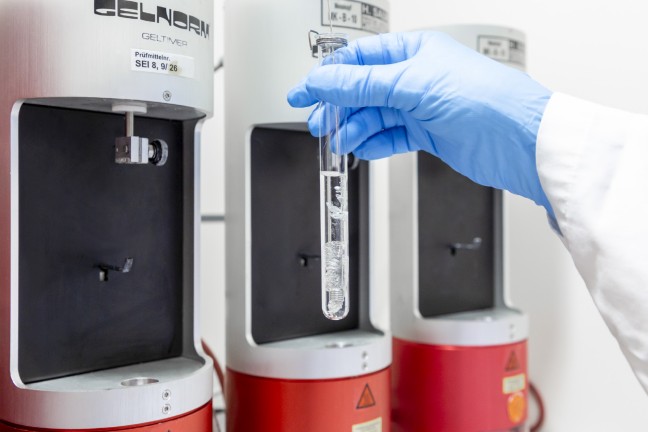
Measuring gel time: the reactivity of WACKER silicone resins is measured in a lab. Graphs of these data can be found below.
Solvent-Free Classic
Renowned for its good impregnation, the one-component phenyl silicone resin SILRES® H62 C from Wacker Chemie AG has a proven record of over 35 years in traction motors of electric rail vehicles. As far back as the 1970s, this resin system was being used by the Swiss manufacturer Brown, Boveri & Cie (now ABB) for electric locomotives, and from the 1980s for the high-speed trains that were a new technology at the time. Since 2007, this system has also been used in drive motors for hybrid and electric cars. Unlike many organic impregnating resins, this product does not contain either solvents or reactive diluents. The liquid formulation is usually applied at temperatures between 60 and 80 °C and cured at temperatures between 170 and 200 °C, with the material being crosslinked by a platinum-catalyzed addition reaction.
“Despite having notched up an exceptionally long track record, SILRES® H62 C is by no means an outmoded product but continues to be state of the art,” explains Dr. Ochs. For example, new-generation subway trains are being introduced in various cities around the world, with electric motors impregnated with SILRES® H62 C from WACKER.
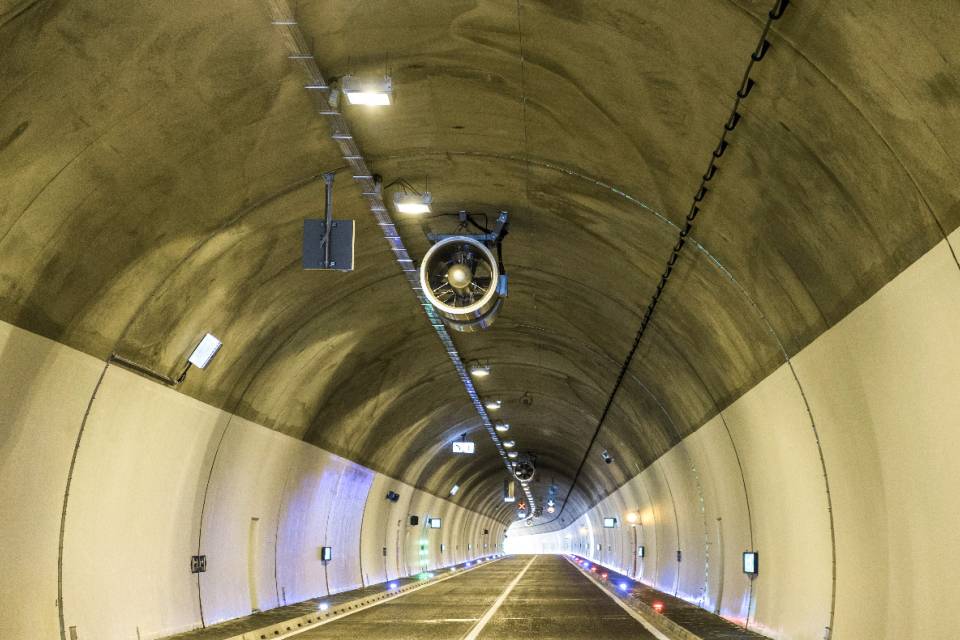
Successful Flame-Proofing
SILRES® H60 is already successfully used in smoke extractor fans that form an important component of fire-protection measures in tunnels. The heat-stable silicone impregnation resin ensures that the fan motors perform reliably in a fire for at least two hours, even at ambient temperatures up to 400 °C, in order to rapidly dissipate toxic fumes and give the rescue services as long as possible to secure and evacuate the hazard area. This corresponds to classification F400 – 120 as per EN 12101-3 and EN 13501-4
As a one-component formulation, SILRES® H62 C contains an inhibitor which slows down the curing reaction. This is advantageous if the resin is applied to the windings by traditional dip coating or vacuum-pressure impregnation (VPI). These processes are mainly used for large machines, for example for impregnating railroad, streetcar and subway traction motors, and for traction motors of diesel-electric haul trucks for open-cast mining. For this, the liquid resin must remain in a processable state during impregnation of the winding, i.e. it must not gel or cure too fast. In the automotive industry, on the other hand, the low curing rate of the one-component silicone proves to be a disadvantage – the slow curing thwarts the goal of impregnating large quantities of stator windings in a short time.
“Our customers from the automotive industry prompted us to develop a ready-to-use phenyl silicone resin formulation that would permit a rapid and automated impregnation process, similar to the established one-component product as far as the impregnation effect is concerned,” said WACKER manager Dr. Klaus Angermaier. This became possible thanks to SILRES® H60. This impregnation resin is a two-component formulation based on the same silicone resin prepolymers used in the one-component product.
Since the new SILRES® H60 grade is a two-component product, developers were able to keep the curing time short. For example, an inhibitor as required for one-component silicone impregnation resins is no longer necessary. This eliminated a factor that limits the curing rate. Moreover, besides the platinum catalyst, the experts at WACKER introduced another accelerator for the hydrosilylation reaction. The additional accelerator chiefly becomes active during the initial stage of thermal curing, i.e. it significantly speeds up gelling.
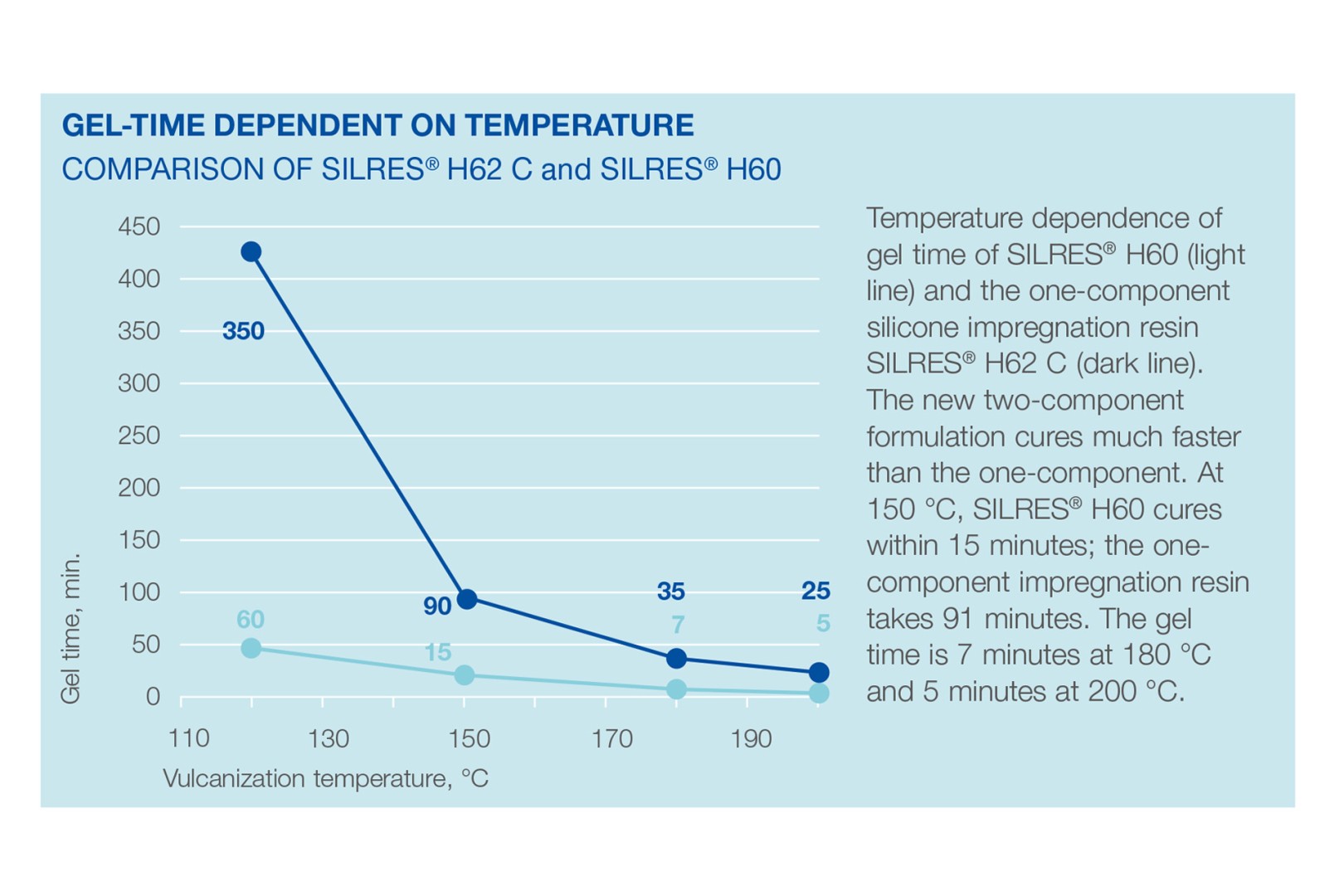
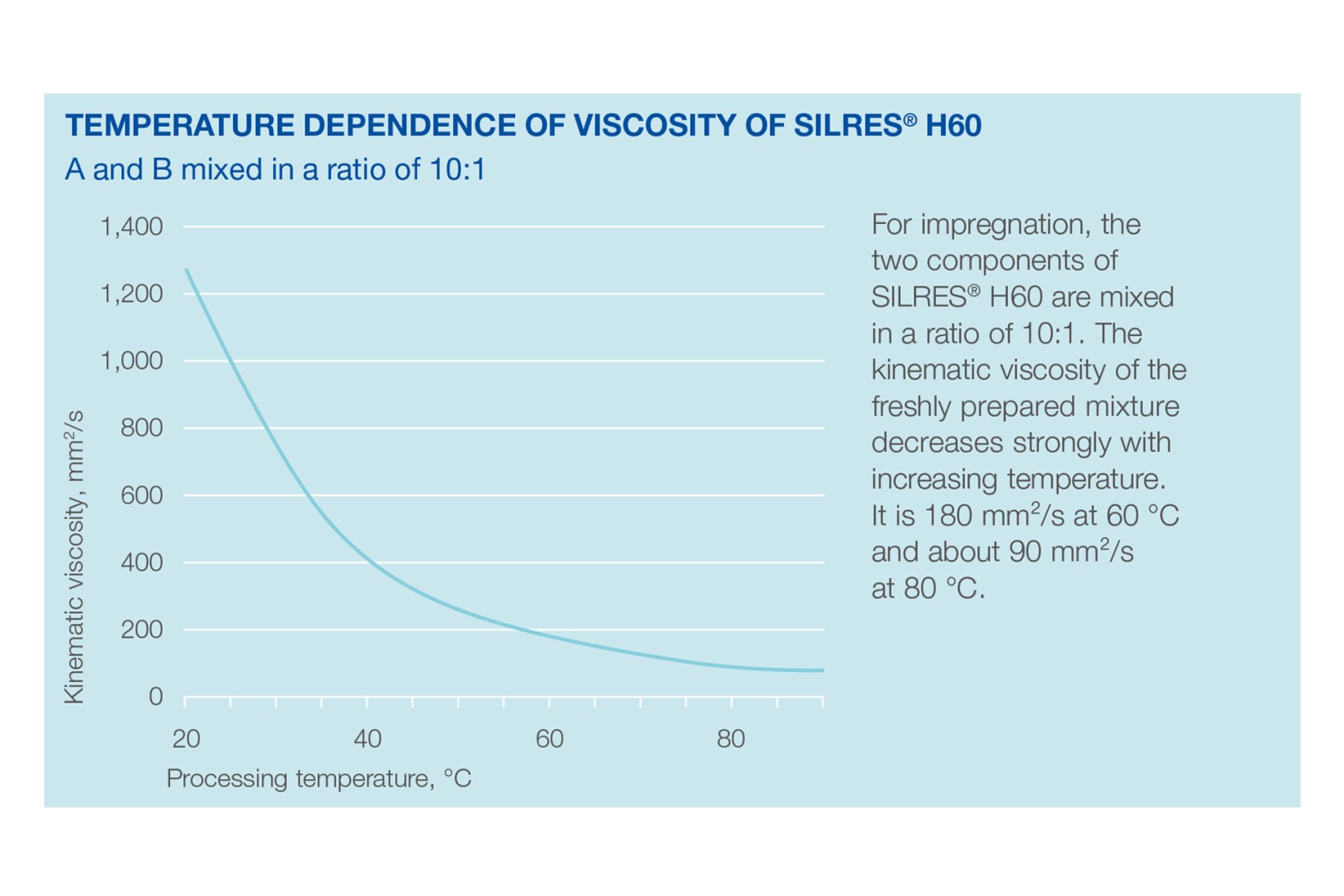
Turbocharging the Curing Rate
This allowed a silicone impregnation resin to be developed with a curing rate comparable to that of organic impregnation resins. The curing time depends greatly on the temperature (see chart, top left). Gel time at 150 °C is thus about 15 minutes. At this temperature, the material is fully cured after six hours. At 180 °C, the gel time drops to five minutes and curing takes just two and a half hours.
The two components are mixed in a ratio of 10:1 for processing. The viscosity of the mixture depends greatly on temperature (see chart, top right): at 25°C, the kinematic viscosity is about 1,000 mm²/s, and drops by a factor of 10 when heated to 80 °C. This effect is used in the impregnation process. Both the resin and the winding are preheated to minimize the resin’s viscosity and ensure it penetrates rapidly into the winding during impregnation. In practice, the temperature is usually maintained at 60 °C.
Like the traditional, tried-and-tested product, the new two-component silicone resin is also free of solvents and reactive crosslinkers, and cures in a platinum-catalyzed addition reaction to form a thermoset of 65 Shore D hardness.
The cured transparent resin has a non-tacky, hydrophobic surface. With a dielectric strength of 27 kV/mm, measured as per IEC 60243-1 (23 °C, 50 Hz, air as ambient medium), the resin is a very good electrical insulator. The material is largely chemically inert and resists aging and long-term thermal loads. It permanently withstands temperatures up to 200 °C, such that a winding impregnation with SILRES® H60 corresponds to thermal insulation class H and higher according to EN 60085. For short periods, the resin also resists temperature spikes significantly above those of the determined continuous service temperature.
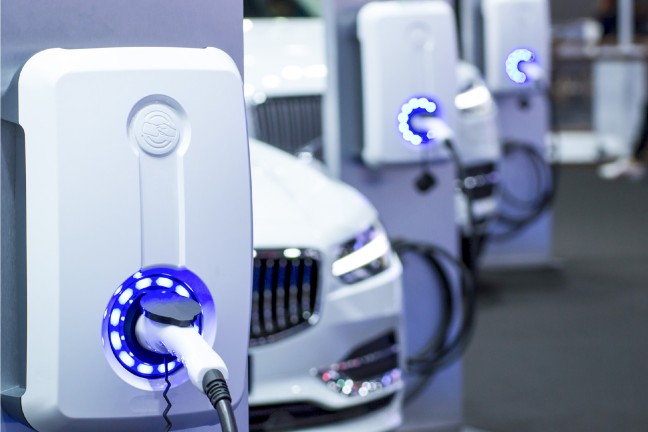
Silicones play an important role in electromobility. Parts of electric motors are impregnated with silicone resins, for example, to cushion mechanical and thermomechanical stresses.
Trickle Impregnation
Thanks to its rapid curing, SILRES® H60 is ideal for trickle impregnation of copper round-wire windings. The new resin, because of its short gel time, is not suitable for dip coating or VPI.
For trickle impregnation, the stator is clamped on a mandrel at a slight angle and rotated around its own longitudinal axis. The impregnation resin is continually dripped through multiple dispensing nozzles onto the winding head of the continuously rotating stator. Gravity and capillary forces draw the liquid into the winding and, together with the rotational movement, ensure that the resin is evenly distributed in the stator. At the same time, the rotation keeps the liquid resin in the coil, preventing the impregnation resin from flowing unused out of the stator. After trickle application, the still-rotating stator passes through a heating zone, where the resin is gelled and cured.
This offers a fast, economical and neat process for achieving a high impregnation quality with low resin-application rates. Trickle impregnation is performed in fully automated systems. The art of the resin processor consists in correctly setting all the process parameters of the trickle impregnation unit – from the application rate of the resin, through the tilt angle of the winding and the rotational speed, to the temperature and timing programs for curing. Modern trickle impregnation units can be easily integrated into electric-motor manufacturing lines.
“SILRES® H60, for the first time, offers electric motor manufacturers a phenyl silicone resin for winding impregnation that can be processed and cured as rapidly as an organic resin,” said Dr. Angermaier, summing up the advantages of the new product. “It will open the door to rapid large-scale production of highly reliable and durable drive motors.”
Contact
For more information on this topic, please contact:
Mr. Dr. Christian Ochs
Technical Marketing
WACKER SILICONES
+49 8677 83-7358
Send message