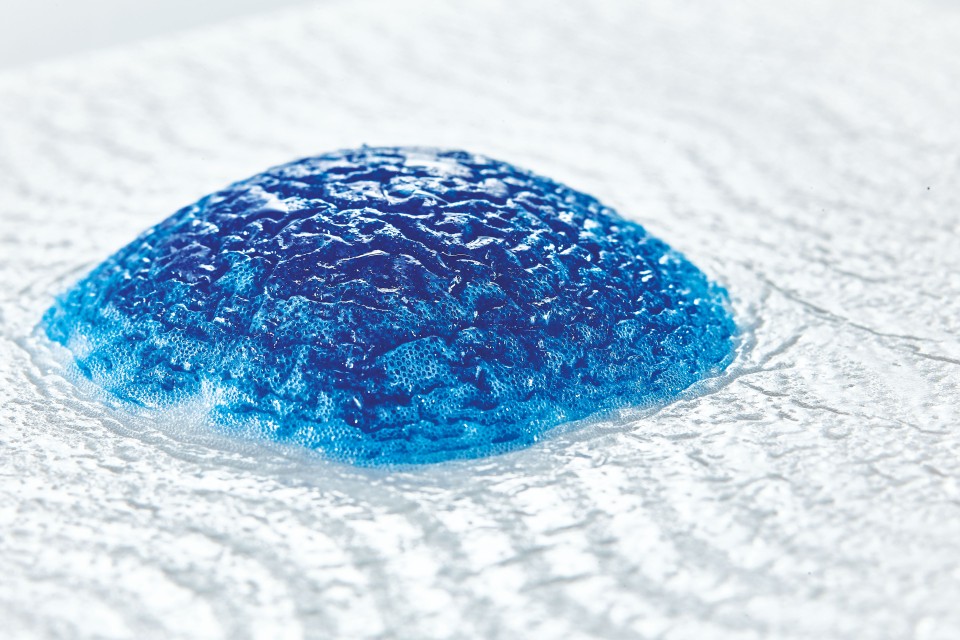
Silicone-Coated Foam Dressings
"Roughly 65,000 people develop pressure ulcers in hospital every year in Germany alone, i.e., pressure ulcers on the skin caused by prolonged lying and reduced mobility."
Space for the Foam
Open wounds heal faster when treated with silicone-coated foam dressings. Freudenberg Performance Materials simplified the manufacture of such wound dressings with a new technology. Indispensable here: silicone adhesives from WACKER.
Many of us still learned from our parents that wounds should be kept as dry as possible – especially to minimize the risk of wound infection. However, even if many lay people and some doctors hold this to be true, numerous studies have since shown that a moist, warm wound environment actually accelerates wound healing. Heat and humidity stimulate cell growth without increasing the risk of infection.
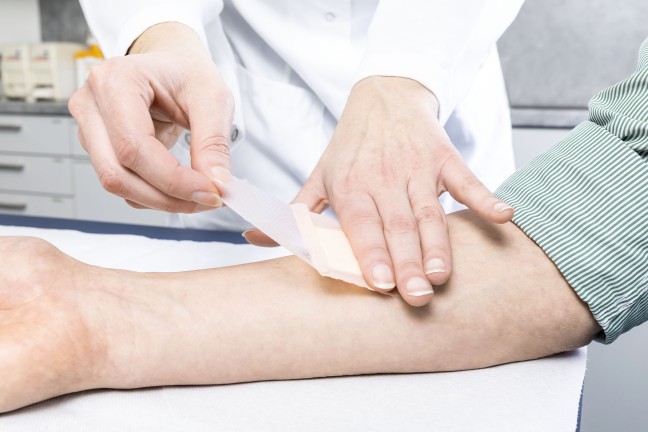
In a silicone-coated foam dressing, several layers of different materials are built up in a laminar structure. The bottom layer of this laminate, the silicone adhesive, fixes the dressing to the skin.
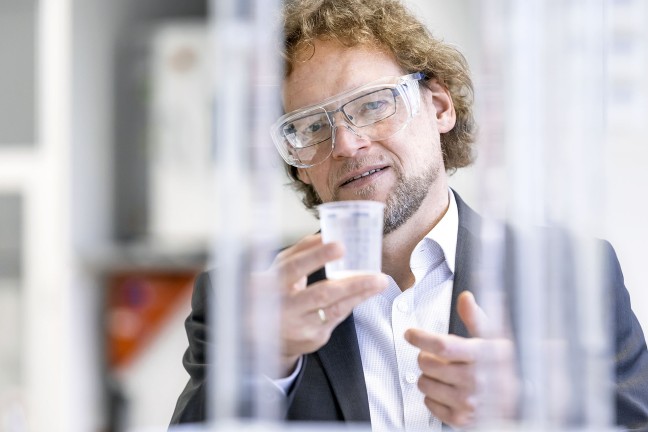
Dr. Thomas Gröer, head of Applications Technology, tests the transparency of a silicone adhesive in his laboratory.
This concept can be realized with silicone-coated foam dressings. Like all hydroactive wound dressings, they regulate moisture in the wound, prevent it from cooling, avoid scab formation, and protect it from environmental influences, thereby creating optimal conditions for healing. Particularly for the treatment of chronic and open wounds – the dreaded pressure ulcer – nursing staff regularly turn to silicone-coated foam dressings.
In a silicone-coated foam dressing, several layers of different materials are built up in a laminar structure. The bottom layer of this laminate, a silicone adhesive layer, fixes the dressing to the skin. An absorbent foam material combined with a water-impermeable but breathable backing film regulates the moisture in the laminate. The absorbent material is often a solid open-cell polyurethane foam. This foam layer absorbs the watery wound secretion – known as exudate – produced during wound healing, thereby preventing the wound edges from becoming softened and bacteria from colonizing the wound. The backing film, in turn, ensures that the wound does not dry out.
Freudenberg Performance Materials, a global manufacturer of technical textiles, has now developed a process for applying the liquid silicone directly to a polyurethane foam. This technology, known as direct coating, is patented. It significantly simplifies the structure and manufacturing process of the silicone-coated foam layer; unlike the conventional process, with this new technology carrier films are no longer necessary.
Freudenberg, based in Weinheim an der Bergstrasse, Germany, found a way to prevent the silicone from penetrating the foam without diminishing the foam's ability to absorb wound secretions. “We developed the foam so that the silicone is available on the surface,” explains Thomas Hofbauer, who was responsible for the preliminary development of this technology at Freudenberg. At the same time, the new coating process ensures that the silicone layer does not cover the entire surface of the foam layer.
For this purpose, during a special process, the silicone adhesive is applied in the form of a wave-like line pattern so that the areas between the lines remain free. “This enables us to achieve two things,” Thomas Hofbauer explains further. “First, the exudate can get into the foam. Second, the foam is given the freedom to expand unimpeded in all directions as it absorbs and swells the exudate – there is no contiguous layer preventing expansion in the direction of the wound bed.”
Silicone is Applied to the Polyurethane Foam
The new technology yields dressings comprising three layers. Because they do not contain a carrier film, they are much more flexible than conventional products and move with the body. A significant advantage for wound healing is that the foam can swell into deeper wounds as soon as it absorbs exudate. “The foam can rest snugly on the contours of the wound, effectively preventing the formation of exudate pooling. This can also reduce bacterial colonization and thus reduce the risk of infection,” explains the Freudenberg expert.
Because fewer process steps are required for production than with conventional technology, the new technology has a positive effect on the sustainability of the dressings: The waste that inevitably results during transfer coating and perforation is eliminated. Fewer intermediate products have to be transported to the production plants, and energy requirements are reduced. In addition, the risk of impurities being introduced into the process chain is lowered.
The developers at Freudenberg also paid special attention to the adhesion properties of the dressing. After extensive testing, Freudenberg Performance Materials opted for high-purity medical-grade silicone adhesive gels such as those offered by WACKER’s SILPURAN® portfolio.
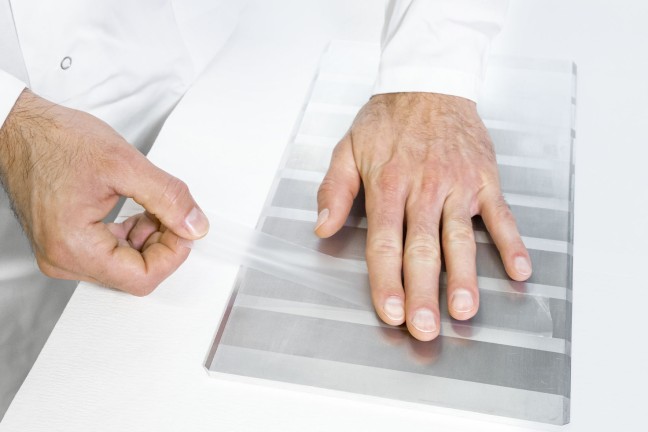
In WACKER’s applications laboratory, test strips of SILPURAN® are prepared to test the adhesive strength of these silicone adhesives for medical applications.
Better Performance with the new Technology
The foam can swell freely into the wound and fit snugly into the contours; with conventional foam overlays, expansion is often limited.

Foam overlay in conventional technology with perforated silicone adhesive layer

Foam overlay with wave-like silicone direct coating
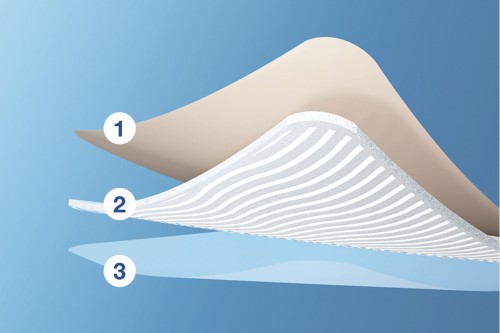
Structure of the patented wound dressing from Freudenberg: 1. Polyurethane film 2. PU foam, directly coated with silicone adhesive 3. Release film
“Silicone adhesives are the materials of choice for the adhesive layer of hydroactive wound dressings,” says Dr. Thomas Gröer, who is responsible for silicone adhesives in WACKER's Applications Technology department. Conventional adhesives stick so strongly that skin cells remain attached to the dressing and are pulled off during peeling, injuring the wound and surrounding skin. This traumatization not only delays healing, but can also cause severe pain – for people with chronic wounds, dressing changes then become an ordeal.
Silicone adhesives are different: As hydrophobic materials, they only adhere to healthy, dry skin, but not to moist wounds. Since they don’t adhere to wound edges or fuse with newly formed tissue, and can be pulled off without great effort, they make low-pain wound care possible.
Silicone adhesives are two-component formulated transparent silicone products that come in a liquid, ready-to-use form, and crosslink at room temperature in a platinum-catalyzed addition reaction to form soft materials with a gel-like consistency. The crosslinked adhesive gels are highly flexible and pliable, but are also elastic. “Together with the low surface energy typical of silicones, the compliance ensures that the adhesion between dry skin and crosslinked silicone gel is built up,” says silicone expert Gröer. “The elasticity of the silicone gel means that the adhesive layer can be easily removed without leaving any residue on the skin.”
Another aspect was important for Freudenberg Performance Materials: The SILPURAN® portfolio comprises silicone gels whose adhesive strength covers the entire range relevant for wound dressings and which can all be gently peeled off the skin. “This allowed us to select the most suitable silicone adhesive for our different foam dressings,” notes Thomas Hofbauer. “Plus it made wound dressings with an adhesive border possible, for which we also manufacture the foam rolls using the new technology.” In these so-called border dressings, there is a silicone coating with high adhesive strength at the back of the cover film, which surrounds the foam layer underneath in the form of an island and comes to rest on the skin surrounding the wound during application.
“The foam rests snugly on the contours of the wound, effectively preventing the formation of exudate pooling.”
Thomas Hofbauer, Freudenberg Performance Materials
Dressing changes easier for Nursing Stuff
The laminate sheets, which are manufactured without an adhesive border, are suitable for further processing into wound pads. These pads are designed to be held in place with a gauze bandage or other secondary fixation during wound care. In these cases, the silicone adhesive layer merely serves as an application aid to make dressing changes easier for the nurse: Like a helping third hand, the adhesive layer holds the pad in situ on the wound so that the nurse has both hands free to apply the secondary fixation. A silicone gel with relatively weak adhesion is used for the adhesive layer of such pads.
Border dressings, on the other hand, are applied without secondary fixation. Here, the silicone gel used at the adhesive edge with its high adhesive strength ensures a long wearing time. “In border dressings manufactured with our technology, the foam island is coated with a weaker-adhesive silicone gel. This means the dressing can be removed very gently from the wound, despite the stronger adhesive edge,” says the Freudenberg expert.
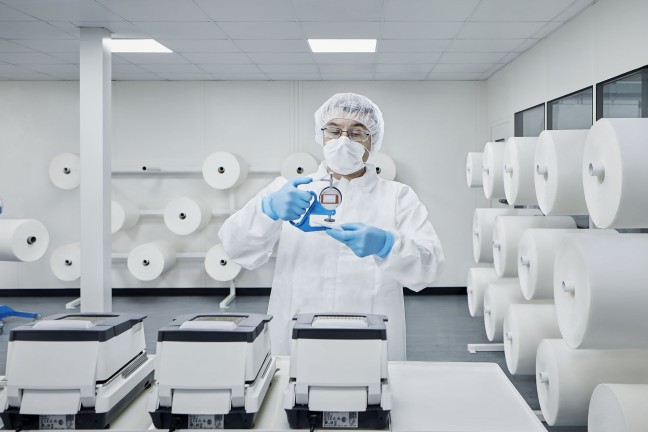
Freudenberg Performance Materials maps the entire process in the cleanroom compliant with ISO 13485, setting new quality standards for this product combination.
The Weinheim-based company also intends to use SILPURAN® adhesive gels for another project. “Silicone-coated foam dressings are also used as a precaution to prevent injuries or skin lesions – for example, to prevent pressure ulcers. Directly coated foams can also be an ideal primary layer for this application,” Thomas Hofbauer is convinced. The foam layer In these dressings is additionally laminated with a cushioning layer. Here it is important that the dressing can not only distribute the pressure optimally, but at the same time gently adhere to the skin and absorb sweat or other body fluids. In addition, the dressing allows regular skin checks and can be used many times over. “A silicone bonding gel is indispensable here,” emphasizes Thomas Hofbauer.
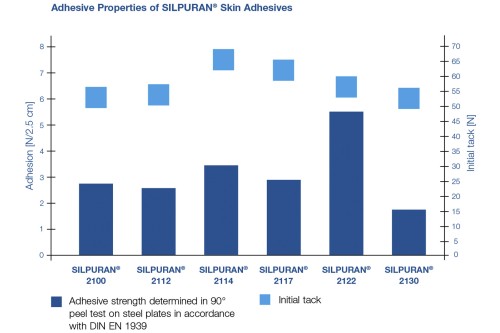
SILPURAN® ADHESIVE GELS
SILPURAN® silicone adhesives have a proven track record as adhesive gels in professional wound dressings spanning many years. These gentle silicone gels that adhere reliably to the skin make changing dressings pain-free and atraumatic. They have a water-repellent surface, but are permeable to water vapor. The individual silicone adhesive grades in the portfolio differ in their adhesive strength. All SILPURAN® silicones from WACKER have passed selected tests for biocompatibility according to ISO 10993 and US Pharmacopeia Class VI. Like all SILPURAN® silicones, silicone adhesives are manufactured according to WACKER’s proprietary Clean Operations standard.
Contact
For more information on this topic, please contact:
Mrs. Andrea Bogner
Senior Marketing Manager
Industrial Solutions WACKER SILICONES
+49 89 6279-1375
Send message