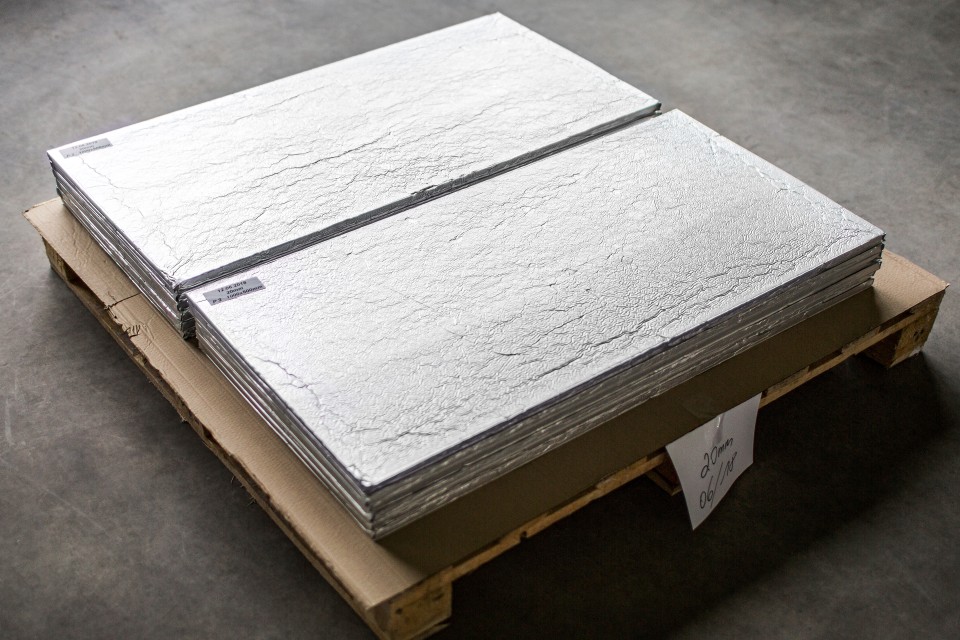
Nichts isoliert so gut wie das Nichts
01.10.2018 Lesezeit: ca. MinutenMinute
Vorteile im Vakuum
Vakuumisolationspaneele (VIP) sind die Spitzenleister im Bereich der Dämmtechnik, zumal wenn sie mit pyrogener Kieselsäure HDK® von WACKER gefüllt sind. Die Ilsenburger Firma Vitec fertigt VI-Paneele individuell auf Anforderung – für den Einsatz in Brandschutztüren, Kühlräumen oder auf dem Bau.
Vakuum, so nennt man in der Physik die Abwesenheit von Materie in einem Raum. Als Faustregel gilt, dass durch das Absaugen der in einem Isolationspaneel verbleibenden Luft die isolierende Wirkung eines Dämmstoffs um den Faktor sechs bis sieben steigt.
Das Prinzip dahinter ist denkbar einfach: Die Vakuumierung unterbindet den durch die Gasmoleküle der Luft bewirkten Wärmetransport und ermöglicht extrem niedrige Wärmeleitfähigkeiten von weniger als 0,004 W·m−1·K−1. So lassen sich Dämmplatten realisieren, die gerade einmal zwei Zentimeter dick sind, aber so gut dämmen und isolieren wie nicht vakuumierte Platten von 12 bis 14 Zentimetern Dicke. Die Einsatzmöglichkeiten sind vielfältig: Thermoverpackungen, Kältegeräte, Kühlräume, Warmwasserspeicher, Brandschutztüren, Fassaden, Böden und Flachdächer werden mit Vakuumisolationspaneelen (VIP) gegen Wärme und Kälte gleichermaßen geschützt.
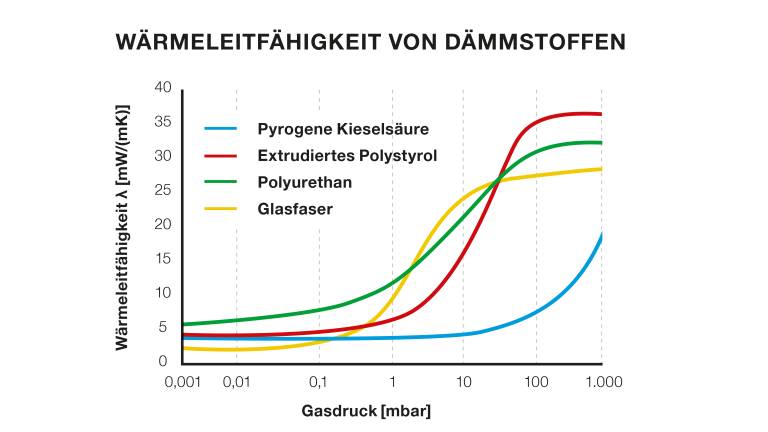
Pyrogene Kieselsäure HDK® dämmt auch bei höherem Gasdruck deutlich besser als vergleichbare Isolierstoffe und weist bei niedrigem Gasdruck zudem die beste Langzeitbeständigkeit auf.
(Quelle: ZAE Bayern)
Mikroporöses Siliciumdioxid
Als Füllmaterialien für VIP eigenen sich Hartschäume, Glasfasern und insbesondere pyrogene Kieselsäure HDK®. „Bei HDK® handelt es sich um eine hochverzweigte, mikroporöse Form von Siliciumdioxid mit unzähligen winzigen Gasporen und damit einer sehr niedrigen Dichte“, erklärt der Chemiker Dr. Jörg Heinlein, der bei WACKER die anwendungstechnische Betreuung für diese Produktgruppe verantwortet. Die hochverzweigte Morphologie von pyrogener Kieselsäure unterdrückt den Wärmetransport auf hocheffektive Weise und ist die Ursache ihrer herausragenden isolierenden Wirkung. Weitere Vorteile von VI-Paneelen mit HDK® sind die sehr gute Langzeitperformance und ihre hohe Formstabilität. Zudem werden im Vergleich zu anderen Füllmaterialien geringere Unterdrücke im VIP benötigt.

Fertige Vakuumisolationspaneele warten bei Vitec in Ilsenburg auf die Abpackung. Durch die Vakuumierung erhöht sich die Isolationswirkung des verarbeiteten Dämmstoffs etwa um den Faktor sieben.

Vor der Vitec-Zentrale in Ilsenburg (v. l.): Hannah Ulrich, Sales Managerin WACKER, Vitec-Geschäftsführer Joachim Luther, Olaf Janßen und Ralf-Geoffrey Frohnwieser, Vitec-Vertrieb, und Dr. Jörg Heinlein, WACKER-Anwendungstechnik.
Start mit Isoliertüren
All diese Eigenschaften weiß auch die Firma Vitec zu schätzen, die im Jahr 2008 aus ihrer Mutterfirma Torlit ausgegründet wurde. Beide teilen sich das neue Firmengelände in Ilsenburg im Harz. Torlit stellt Isoliertüren für Lagerhallen, Kühlräume und andere Bereiche mit erhöhten Sicherheitsanforderungen her; die benachbarte Tochterfirma Vitec wiederum liefert die Vakuumisolationspaneele, die in den Isoliertüren von Torlit verbaut werden.
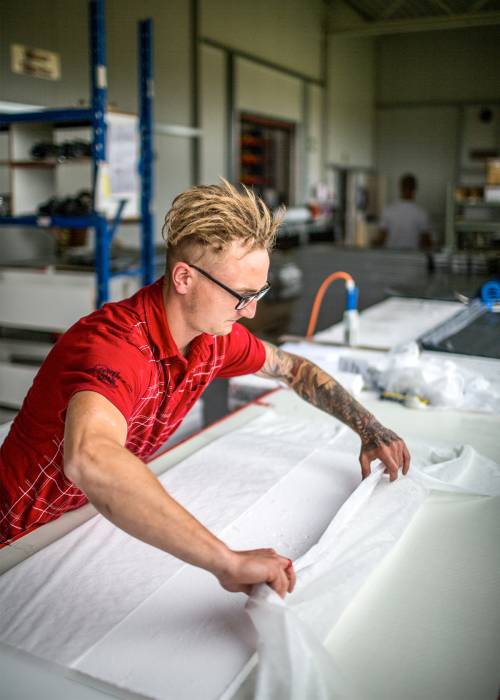
Ein Mitarbeiter bereitet ein Isolierpaneel zur Verpackung mit der Schutzfolie und zur anschließenden Vakuumierung vor.
Der Einsatz von Vakuumisolationspaneelen ermöglichte es Torlit, die Dicke ihrer Türdämmungen von 110 auf 20 Millimeter zu verringern. Ein weiteres wesentliches Argument, HDK® als Kernmaterial für die VIP zu nutzen, nennt Joachim Luther, Geschäftsführer der Firma Torlit und zugleich der aus ihr hervorgegangenen Vitec GmbH: „Normalerweise gilt: Was gut isoliert, brennt auch gut.“ Kieselsäure aber sei nicht brennbar und damit für Brandschutztüren ideal. „Mittels der Kieselsäure haben wir die Dicke unserer Türen reduziert, das Gewicht gesenkt und zugleich die Dämmung und den Brandschutz verbessert“, fasst Luther die Vorteile zusammen.
Als Spezialisten für Brandschutz- und Kühlraumtüren kennen die Torlit-Ingenieure die Vor- und Nachteile vieler Dämmmaterialien genau. Mineralwolle beispielsweise ist beim Einsatz in Kühlräumen verpönt, weil sie Feuchtigkeit zieht und dann ihre dämmende Wirkung verliert. Polystyrol, das meistgebrauchte Isoliermaterial am Bau, erfordert wiederum hohe Dicken. Anorganische Schäume auf Basis von Keramikpartikeln, die mit Phenolharzen formuliert werden, erwiesen sich als recht spröde, kamen aber dennoch in der ersten Generation der Brandschutztüren von Torlit zum Einsatz. Nach einer kurzen Phase des Experimentierens entschieden sich die Torlit-Techniker schließlich vor rund zehn Jahren, fast nur noch Vakuumisolationspaneele in ihren Türen zu verbauen, die mit HDK® von WACKER gefüllt sind.
Bündig eingepasst
Brandschutz- und Kühlraumtüren werden in der Regel auf Anforderung und nach Maß produziert. Auch die darin verbauten Vakuumisolationspaneele werden individuell hergestellt, um sie bündig in die Türen einpassen zu können. Torlit ist deshalb auf eine sehr schnelle und flexible Belieferung mit VIP angewiesen.
„Wir liefern unsere Brandschutztüren in jeder Größe innerhalb von zwei bis drei Wochen – das passte aber nicht mit den Lieferfristen der VIP-Hersteller zusammen, die oft sechs bis acht Wochen benötigten“, sagt Joachim Luther. „Um unsere Türen schneller produzieren und ausliefern zu können, wurde es zwingend nötig, die VIP selbst herzustellen“, berichtet er weiter.
Das Prinzip der Herstellung eines VIP ist einfach: Ein Dämmstoff wird in der gewünschten Dicke – meistens wenige Zentimeter – in einen Folienbeutel eingelegt, vakuumiert und verschweißt. Zur Verarbeitung von HDK® in VIP wird jedoch spezifisches prozesstechnisches Knowhow benötigt, das Vitec sich im Verlauf der letzten zehn Jahre erarbeitet hat. Die wesentlichen Herausforderungen sind,
- die HDK® trocken zu halten,
- große Volumina eines lockeren, staubenden Pulvers aus Gebinden zu entleeren, zu fördern, zu mischen und zu Formkörpern zu verpressen,
- sowie HDK® bei der Verarbeitung gut fließfähig zu halten. Die Kieselsäure sollte frei von Klumpen und Schollen sein, damit möglichst homogene Formkörper entstehen.
Bei Vitec wird HDK® mit Fasern und weiteren Komponenten als Pulvermischung eingesetzt. Die Mischung enthält unter anderem ein sogenanntes Trübungsmittel. Dies dient dazu, Wärmestrahlung, die von außen in den Isolierstoff gelangt, zu absorbieren oder zu reflektieren. Auf diese Weise wird die Wärmeleitfähigkeit des VIP weiter reduziert.
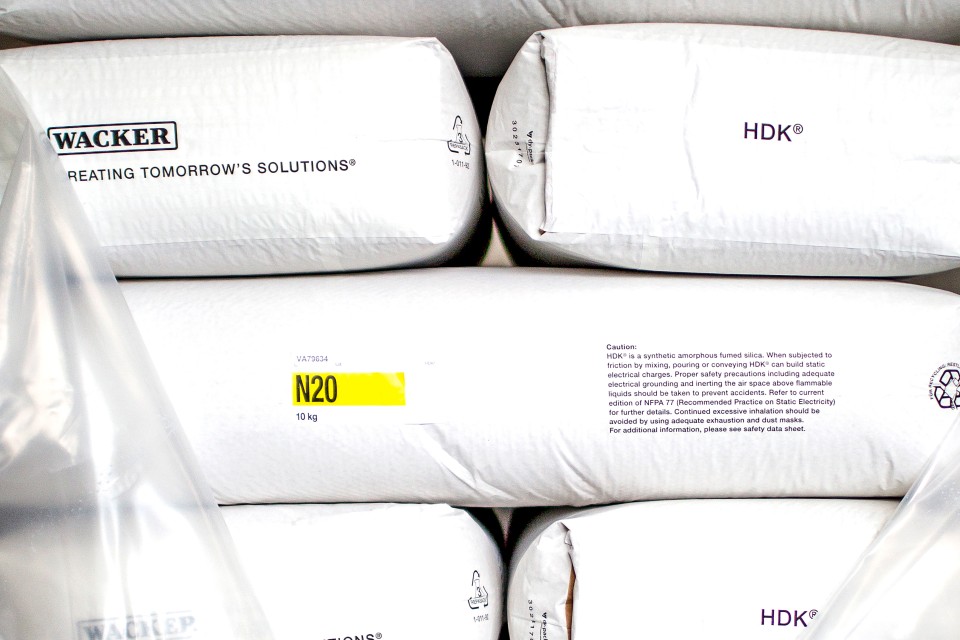
Vorteile von HDK® bei der Verwendung in Vakuumisolationspaneelen (VIP):
• HDK® dämmt wegen ihrer mikroporösen Struktur schon bei geringeren Unterdrücken im VIP hervorragend.
• HDK® zeigt eine sehr gute Langzeit-Dämmleistung.
• HDK® ist ein äußerst robuster Stützkörper, das VIP ist trotz des hohen Außendrucks formstabil.
• HDK® ist nicht brennbar.
• VIP-Kerne aus HDK® können wiederverwendet werden.
Barriere gegen Feuchtigkeit
Nach der Kompaktierung wird der Formkörper aus der HDK®-Mischung in einen Beutel aus Spezialfolie eingelegt. Die Folie besteht aus mehreren dünnen Polymer- und Metallschichten, damit eine möglichst hohe Barriere gegen das Eindringen von Gasen und Feuchtigkeit gewährleistet ist und die VIP möglichst lange ihre Dämmleistung halten. Die Vitec-Techniker gehen davon aus, dass ihre Vakuumisolationspaneele Jahrzehnte Dienst tun können. Auch hier ist HDK® alternativen Füllmaterialien überlegen. So weisen Glasfaser-Kerne und Kunststoffschäume eine – im Vergleich zu pyrogener Kieselsäure – schnellere Alterung auf, weil der Druck im Inneren des Kerns rascher ansteigt und sich dann die Isolationseigenschaften entsprechend verschlechtern.
Für spezielle Anwendungen, etwa zur Isolierung von Flachdächern und Dachterrassen, wo besonders robuste Paneele verlangt werden, haben die Ilsenburger VI-Paneele im Sortiment, die mit einem sehr harten glasfaserverstärkten Kunststoff ummantelt sind. „Da kann man auf der Baustelle drauf laufen, da passiert gar nichts“, sagt Ralf-Geoffrey Frohnwieser, ein Vertriebsmitarbeiter von Vitec.
Für Gebäudedämmungen werden auch VIP angeboten, deren Randbereich aus rund zehn Millimeter herkömmlichen Dämmstoffs (XPS) besteht und somit noch bearbeitbar ist. „Auf diese Weise lassen sich die am Bau üblichen Toleranzen ausgleichen“, sagt Frohnwieser. Darüber hinaus wird so der Wärmetransport im Bereich der Stöße zwischen den einzelnen VIP unterbunden. VIP für die Dach- oder Fassadendämmung werden individuell gefertigt und zusammen mit Verlegeplänen an die Handwerksbetriebe geliefert.
„Pyrogene Kieselsäure brennt nicht und ist damit für den Einsatz in Brandschutztüren ideal.“
Joachim Luther, Geschäftsführer, Vitec GmbH
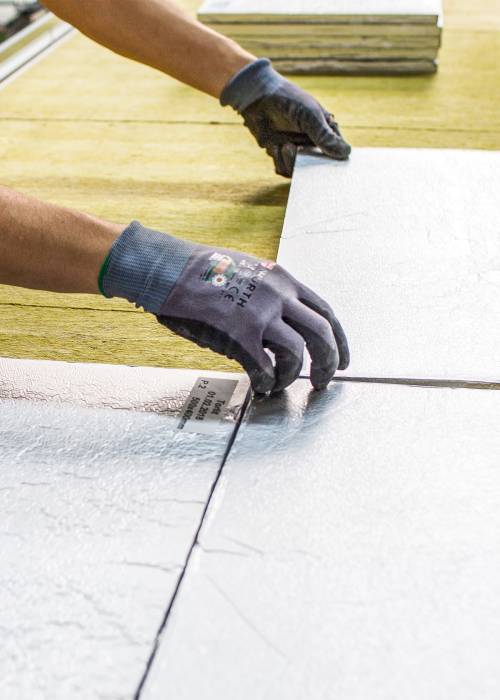
Für den Einsatz auf dem Bau stellt Vitec Vakuumisolationspaneele auf Maß her und liefert gleich die Verlegepläne dazu.
Spezialcontainer für alte Lithium-Ionen-Batterien
In jüngster Zeit konnte Vitec zudem eine innovative Lösung für Sammelcontainer von verbrauchten Lithium-Ionen-Batterien erfolgreich realisieren. In diesen Sicherheitscontainern werden verbrauchte Akkus von Elektroautos, Elektrofahrrädern oder größeren Elektrogeräten gesammelt und dann zum Entsorgungsunternehmen transportiert. Beim Transport sind strenge behördliche Auflagen zu beachten. Denn Lithium-Ionen-Akkus können sich potenziell selbst entzünden, was zu Bränden mit hohen Temperaturen von über 1.000 Grad Celsius führt. Die Container müssen so beschaffen sein, dass ihre Außenwände in einem solchen Fall nicht heißer als 100 Grad Celsius werden. „In diesem Projekt konnten wir unsere Stärken im Metallbau und bei der VIP-Fertigung in optimaler Weise zusammenführen und mit unserem Partner einen Sammelcontainer entwickeln, der alle Anforderungen des Kunden ebenso optimal erfüllt“, sagt Olaf Jansen, Vertriebsleiter von Vitec.
Im Container sind die VI-Paneele passgenau angeordnet, sodass eine Innenkammer mit sehr guter Dämmleistung entsteht. Durch eine Kaschierung mit Blechen sind die VIP zudem vor Verletzungen geschützt, die etwa beim Beladen entstehen können. In solchen und ähnlichen Anwendungen sieht Olaf Jansen die Zukunft der Firma Vitec, die flexibel und spezialisiert bleiben soll: „Wir setzen nicht auf Masse, sondern auf individuelle Fertigung und Weiterveredlung.“
Kontakt
Mehr Informationen zum Thema erhalten Sie von
Frau Hannah Ullrich
Sales Managerin
Pyrogenic Silica WACKER SILICONES
+49 152 093 519 30
Nachricht senden